TPEs are silently taking over
Also, download this story from the electronic issue here
Thermoplastic elastomers (TPEs) have found a discreet way to take over the world. The interior of cars, that rubber ducky, toothbrushes, shoes, they are all made of TPEs. We barely notice them, but they’re everywhere.
These materials are replacing rubber in many industries. Bulk of the demand is from the automotive industry, but TPEs are also used in the building and construction, engineering, footwear, wires and cable, medical, and many other industries. The TPE production is a billion dollar industry, and is only expected to grow within the next five years.
Manufacturers play a key role since they have and continue to innovate TPE, so that it can replace thermoplastics and natural rubber in many applications. Unlike rubber, TPEs are fully recyclable. They possess good mechanical properties and have a lower density than other classes of polymers, such as polyvinyl chloride (PVC) and cross-linked elastomers (EPDM).
While the material is manufactured in multiple regions, the supply mainly goes to the two major markets: Asia and North America. Combined, the two regions took up 70% of the TPE market in 2014, according to Markets and Markets.
Asia Pacific was the highest consumer of TPE, accounting for 40% of the total consumption last year. Grand View Research says that rapidly-growing countries like India are the major players, making a combined total of 66% of the regional demand. North America is the second-largest market for TPE, backed by its automotive industry.
A study by Markets and Markets projects that in 2020, the TPE market size will grow to US$27.8 billion with a CAGR of 8.5% over the next five years. A large chunk of the market - US$11.9 billion to be exact – will come from the automotive industry. Asia will still have the highest demand because of the increasing car sales in countries like India and China. Asia Pacific will still be the market leader by 2020.
Freedonia Group came up with similar predictions. The group said China is already the highest consumer of TPEs by volume. The country’s demand will grow at 8% CAGR until 2017.
Other regions will also have an increased demand for TPE. Africa and the Middle East region currently have the lowest demand for TPE, but will see an improvement by 2017. Western Europe will also have its share of market growth, but will have only a small share of the global demand.
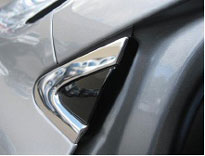
The group also says that by 2017, Styrenic block copolymers (SBCs) will be the leading TPE type, as it is today. Growth will be slow since the market is already saturated with SBCs. POEs or polyolefin elastomers will grow fastest because they are new and steadily accepted as additives for packaging adhesives and plastics. TPVs, or thermoplastic vulcanisates, will also be strong since the material is expanding from the automotive industry to other fields like consumer and medical products.
TPEs used in sustainable material
For more than five years compounds from TPE specialist Kraiburg have been used in Wopex pencils from manufacturer Staedtler. Since January 2015 the company also offers coloured pencils from the Wopex series with a soft component that comes from Germany-headquartered Kraiburg.
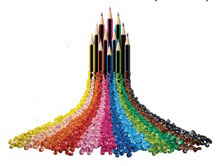
The special feature of the pencils is the sustainable production process: the base material is a natural fibre composite material, with 70% wood and 30% polymers and additives. Since the compound from Kraiburg’s Thermolast K portfolio already demonstrated good adhesion to the wood-polymer material of the Wopex pencil, the TPE is also applied to the coloured pencils, by means of co-extrusion.
TPE based on SBC for automotive sector
TPEs will be high in demand as automobile makers push to reduce their vehicles’ weight. One example of TPE use comes from car windows that can be framed more economically and more securely with a novel TPE based on styrene block copolymers (TPS), as opposed to rubber seals. Advantageously, the typically low viscosity of TPS leads to reduced glass breakage and allows thinner glass to be used.
TPS has especially enjoyed stellar growth in the automotive and industrial sectors in recent years as well as in the consumer and medical sectors. A key advantage of TPS is its production flexibility, which opens it up to a diverse range of products. TPS are physically blended formulations that can be customised via the choice of additives, dyes and other thermoplastics.
The number of individual ingredients usually ranges from five to ten and can be varied so as to influence properties, such as appearance and weathering resistance or ease of processing. Another plus is that TPS articles can be produced economically by injection moulding
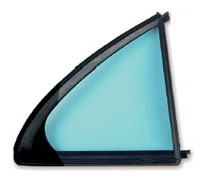
The walls of TPS articles can be up to 10% thinner than commercial TPEs, a fact which reduces the cycle time. Adding to the growth of TPS has been the fact that they can be co-injection moulded, especially with thermoplastics. Manufacturers are now also turning increasingly to TPS for new parts that offer new features.
TPS is also much less demanding in terms of processing parameters than other TPE materials, such as TPVs (thermoplastic vulcanisates) and TPUs (thermoplastic polyurethane elastomers).
As a result, they are not expected to experience significant loss of UV resistance at critical processing parameters, e. g. in components exposed to high shear rates or elevated temperatures.
Thus, these new high-Flow materials meet all the requirements imposed by automotive manufacturers. With a change of viscosity but all other typical properties retained, TPS can now be moulded around even thinner glass and laminated panes. It is already being used for applications that involve very long flow paths, for example, moulding around rear windows and vehicle roofs. The novel compounds boost flow lengths by 34% compared with those of previous TPS compounds. Because the cavity pressure can be lowered from, 1,000 to 550 bar, and the melt temperature lowered by 35°C, cycle times can be cut by 10%.
Medical sector taking an interest
While the automotive sector commands the highest use for TPEs, medical market is also growing. Taking this into consideration, Swedish supplier Hexpol TPE, part of Elasto, has expanded their range of Mediprene TPE compounds for plunger seals in single-use syringes.
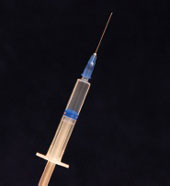
Niklas Ottosson, Medical Technical Manager for Elasto commented, “Over recent years there has been a rise in demand for singleuse syringes and a clear move from rubber to TPE for plunger seals.”
The grades are sterilisable with gamma, EtO and steam and representative grades have passed cytotoxicity tests according to ISO 10993-5 and biocompatibility tests according to USP Class VI. The grades are also available in a range of hardnesses from 43 to 73 Shore A. The TPE seal, which is mounted on the end of the plunger, needs to provide a leakproof seal with the syringe barrel, and TPEs are said to offer low compression set helping to maintain seal integrity.
The grades are available as translucent or coloured compounds, made from medical grade raw materials.
Alongside their material advantages, because of the cost and speed at which they can be manufactured, the TPEs are being specified as an alternative to thermoset rubber. Consistent shrinkage also allows for tight dimensional tolerances with fewer process steps and without the need for additional operations such as trimming.
(PRA)Copyright (c) 2015 www.plasticsandrubberasia.com. All rights reserved.