Borouge: air-cooled PP blown film solution
Also, download this story from the electronic issue here
Polypropylene (PP) is a plastic material that has a number of different uses, hence it is always in demand, especially in the packaging sector. The PP market is already a multibillion dollar industry, and is expected to be valued at US$133 billion in 2023. Meanwhile, Middle East producer of polyolefins Borouge provides an account of using air cooled blown film successfully to produce packaging material.
PP market to soar
The world demanded 58.45 million tonnes of PP in 2014. In just seven years, demand is expected to reach 87.35 million tonnes at a CAGR of 5.2%.
The automobile, construction, and packaging industries will be main drivers for growth. PP will be most in demand in the Asia Pacific region, concentrated in manufacturing hotbeds like China, India, and Indonesia.
In Transparency Market Research’s new report titled “Polypropylene Market - Global Industry Analysis, Size, Share, Growth, Trends and Forecast, 2015-2023”, the global PP market was valued at US$81.63 billion in 2014 and is anticipated to reach US$133.39 billion by 2023, expanding at a CAGR of 5.7% between 2015 and 2023. In terms of volume, the global PP market stood at 57,898.9 kilotonnes in 2014.
Rising demand for PP in the packaging industry is likely to augment the global PP market in the next few years.
In terms of volume, the packaging industry was the largest consumer of PP in 2014, accounting for over 45% share. Beneficial properties of PP such as transparency, stiffness, sealability, twist retention, and moisture resistance make it one of the most efficient materials for use in packaging.
Demand for PP is high in Asia Pacific, especially in food packaging, due to increasing population and changing lifestyle. This is because consumers are opting for easy-to-cook or ready-to-eat food. In terms of volume, Asia Pacific accounted for over 50% share of the PP market in 2014 and is likely to be the fastest-growing region during the forecast period, says Transparency Market Research.
Technology for PP blown film
More than half of global PP output is processed into packaging products. The largest sales market is flexible packaging made from PP films.
PP for blown film has traditionally been produced using the water quenched method, where the film bubble is blown downwards and cooled instantaneously using a stream of water in contact with the outer surface of the film bubble.
The difficulty in using PP for air cooled blown film lies in its low melt strength, resulting in very poor bubble stability. Also the film is often splitty and has poor optical properties, due to the low efficiency of the cooling air.
Middle East polymers producer Borouge has been very successful with a PP blown film solution that can overcome the above issues and benefit customers in the flexible packaging industry.
RB707CF is a PP random copolymer material. As a monolayer film, it offers very good optical properties, with a haze value of < 10%, and a stiffness level comparable to a High Density Polyethylene (HDPE) film of density 0.950 g/ cm3. Being a random copolymer, films made of RB707CF can achieve good sealing performance, with sterilisation possible at temperatures up to 121°C.
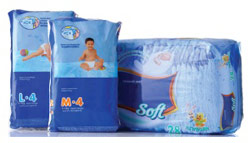
RB707CF can also be coextruded with linear low density polyethylene (LLDPE) on the outer layers without the need for a tie layer. With metallocene LLDPE (mLLDPE) as the surface layers and RB707CF as the core layer in a three-layer co-extrusion film, this structure offers enhanced optical properties and sealing performance with a well balanced stiffness to toughness ratio. Converters originally using LLDPE as the core layer in three-layer co-extrusion films can switch to RB707CF and still have the flexibility to downgauge the film.
Applications that can benefit from RB707CF are very well spread and still growing. The list is long and includes lamination film, food packaging film, bread bag, tissue packaging film, shrink film, cast PP film replacement and general consumer product packaging film.
Bread bag film success story
A customer approached Borouge for an improved solution for its bread bag film business. In order to increase shelf appeal for the final product as requested by the end users, the customer was looking for a film with high optical properties.
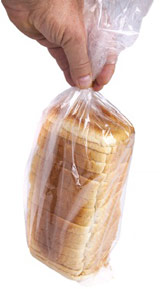
At the same time, the film had to be stiff enough for smooth printing and handling. On top of that, mechanical and sealing performances of the finished film had to be excellent, so that the integrity of the bag would not be compromised.
Borouge recommended RB707CF to be in the film’s core layer, together with PE on the outer layers. Trial runs were successful and the film structure proposed by Borouge was highly appreciated by the customer because it had helped to check all the critical boxes of requirements set by this improvement initiative.
Another important benefit of RB707CF is its flexibility of allowing blown film converters to process PP on conventional air cooled PE blown film lines with good efficiency. This allows blown film converters to enter new application areas that were previously not accessible to them with the PE product family.
(PRA)Copyright (c) 2015 www.plasticsandrubberasia.com. All rights reserved.