TPN Flexpak: embracing new technology
Also, download this story from the electronic issue here
While some companies are followers, others strive to lead. One way of doing this is through innovation and technology. Thailand’s TPN Flexpak, a flexible packaging manufacturer that supplies a host of printed flexible packaging for food and fast moving consumer goods, has chosen to take the latter path.
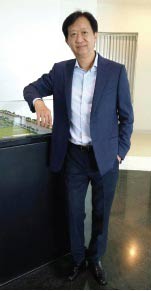
A subsidiary of 60-year old paper products specialist Thung Hua Sinn Group, family-run TPN last year took delivery of not one, but three flexographic presses from Germany-based Windmöller & Hölscher (W&H).
“We took out two old presses and decided to replace these with three brand new machines,” said TPN’s Managing Director Ananchat Thangkasemvathana.
TPN now boasts four Miraflex flexographic printing presses from W&H, which effectively makes it a leader in flexographic printing in Thailand, and maybe even in the region!
While gravure presses have been the workhorse of the packaging/printing sector, in recent years flexo printing has picked up mainly because of its versatility, reliability and speed. Another reason is the productivity.
“With this new technology, we have moved up another notch. We have improved our capacity by 50%,” said Ananchat, speaking to PRA at TPN’s facility in Wellgrow Industrial Estate, Bangpakong.
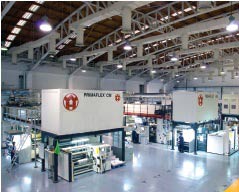
The Miraflex presses offer wide webs (1,270/1,450 mm); eight to ten colour printing; and speeds of up to 400 m/ minute maximum on the machines at TPN. Other features are "maximum efficiency, robust design for quality and register optimisation on thin substrates".
“We also use environmentally friendly non-toluene based inks. These inks use organic pigments and have very low solvent retention, making them safe for food packaging. Our ink formulation and dispensing systems provide a consistent colour every time and batch-to-batch reproducibility,” adds Ananchat.
The company still maintains in its stable of presses a Heliostar gravure printing press, also from W&H, that caters to the demand for smaller print orders, thus allowing for easy job change-overs.
A host of products
Set up 15 years ago, TPN produces film on roll stock, wicketed bags, pillow pouches, stand-up pouches, zipper bags, microwaveable pouches, retortable pouches, side weld bags and shrink sleeves.
Besides the printing machinery, the facility houses film extrusion, prepress, and converting/ laminating equipment. In film extrusion, it has two three-layer blown film lines from W&H, with outputs of 300 kg/hour and 500 kg/hour respectively that produce mainly 500 tonnes/month of PE film.
The other types of film that go into the packaging are sourced from suppliers, totalling up to a usage of about 2,000 tonnes/month.
Adding on investments
Ananchat adds, “In the last few years, we have put in a lot of investment in the facility and have continued to invest, even during the slower global growth and against currency fluctuations.” In fact, over the past three years, TPN has invested up to EUR50 million in plant and machinery.
“When we upgrade our machinery, we are interested in the most advanced technology, especially if it’s something new.” It also helps that Thailand’s BOI (Board of Investment) encourages technology improvements, and offers tax incentives to companies embracing these new technologies. “The good thing about the government policy is that it wants companies to invest in new technology that saves energy, has more automation, produces less waste and is environmentally friendly.”
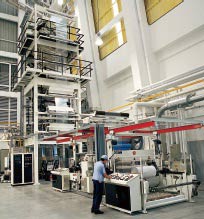
With this encouragement and support, TPN has also automated its operations and managed to reduce its staff force from 500 to 350. “Our aim is to bring it down further, to have more lean operations.”
Meanwhile, TPN’s exports have grown too over the years, with almost 50% of its output exported, through indirect and direct exports. It expects a commendable turnover of EUR40 million this year, from its flexible packaging business.
“We grew 20-30% in the first few years of our business, but now it has reached a plateau and growth is stagnant,” admitted Ananchat, adding that the business contracted by 5% in the first six months of the year due to the slowdown of the economy and contraction of domestic consumption.
Ten years ago, to diversify its product range, the firm set up a medical division. “We have a partnership with a Singaporean company and produce medical devices like pouches.” The controlled environment in place for its food packaging served it well as did the GMP and HACCP certifications, though Ananchat says that medical takes up a small part (4%) of the group’s total business. “A major part, 50%, of our business is for food packaging, followed by consumer products.”
The company has also invested in R&D, with an in-house development unit for developing its own branded packaging. A latest innovation is a steam pouch, a self-venting microwavable pouch, which release steam automatically during the reheating process in a microwave.
When asked what he foresees in the future, Ananchat replied, “The trend in Thailand is for flexible packaging. It is still a big market. And it is an interesting sector to be involved in because it is changing all the time.”
Looking further into the crystal ball, Ananchat says the company will stay close to its agenda of sustainability, by focusing on saving more energy in its operations. “It’s not like the old days. We have to learn from the West where green and sustainable technology is important and follow this trend.”
When asked if there were plans for further capital investments, Ananchat replied, “We always have a plan, but it depends on our customers’ needs and we need to match their requirements.”
He does not rule out investment in blown film lines that cater to more layers, adding “we need to convey to our customers the new technologies available.”
“It is because of our innovative stand that we have been accepted by customers, both locally and internationally. We will continue to keep abreast of the latest trends in printing and packaging technology, to allow our customers to provide quality products,” concluded Ananchat.
(PRA)Copyright (c) 2015 www.plasticsandrubberasia.com. All rights reserved.