Sidel supplies first aseptic line to Indonesia; to reduce jobs by 10% in 2016
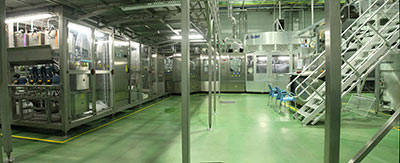
PT Hokkan has installed the first Sidel dry aseptic line in Indonesia and in doing so has expanded its production capacity as a co-packer of non-carbonated healthy soft drinks for the growing Indonesian beverage market. The investment follows the success of the first Sidel line installed at the company - a wet aseptic Combi line - with the two lines now working alongside each other to offer the company increased flexibility in production.
Indonesia is one of the best-performing emerging countries with a GDP growth in 2013 of 5.8%, according to the World Bank. This continuing growth in the economy, together with an increasing population, has led to a significant jump in the consumption of beverages in Indonesia over recent years. For example, from 2012 to 2017, the forecast CAGR (compound annual growth rate) in Asian Speciality Drinks is 8.4%, representing a growth of almost 50% over the whole period. As Indonesia’s growing “middle-class” with more expendable income is looking for new experiences and tastes, the global trend of urbanisation - with more people living within the main urban areas of major cities - is reflected in the country’s consumption patterns which are expected to continue to grow.
PT.Hokkan Indonesia is part of the Japanese Hokkan Group and is a co-packer for the beverage industry, specialising in PET bottles of up to 500 ml. The company’s bottle manufacturing facility is located in Bogor in the West Java Province of Indonesia some 50 km south of Jakarta. It benefits from supplies of fresh natural water drawn from wells and is also close to Sukabumi city with its established distribution network in nearby Jakarta. With the commissioning of its second Sidel Combi line in March 2015, the plant has more than doubled its potential production capacity. The aseptic process makes it possible to manufacture products with a long shelf life packaged in flexible and lightweight bottle designs. PT.Hokkan Indonesia is currently investing further in its R&D laboratory services to extend its offering to potential customers located in the region.
Following the current global trend, Indonesian consumers are becoming more health-conscious, a trend that is set to continue, with younger people in particular already demanding conveniently packaged, healthy products. Dairy products, such as drinkable yoghurts, are already one area that has been positively influenced by the emerging trend, with single-serve, “on-the-go”, rigid plastic formats performing particularly well. PT.Hokkan Indonesia is therefore focusing its business development on milk based products, including milk tea, milk coffee and ‘Matcha’, a popular drink in Indonesia based on a finely ground powder produced from specially grown and processed green tea plants. Matcha, one of the beverages currently produced on the Sidel wet aseptic Combi line, is an excellent example of a product which meets the increasing demands for healthier alternatives. Growing the plants in the shade gives Matcha a higher theanine content which contributes to improved mental focus, while the antioxidant catechine delivered by green tea leaves also provides positive health benefits.
Rather than gaining market share from existing suppliers to the Indonesian market, the Hokkan Group sees itself attempting to create a new aseptic market, in which it strongly believes, for the Indonesian consumer. “From our experience in Japan, we know that aseptic technology can achieve lightweight bottles, a flexible bottle design and long product shelf life. Aseptic technology offers us numerous opportunities for making quality products,” said Masaaki Ikezawa, President/Director of PT.Hokkan Indonesia.
PT.Hokkan Indonesia selected a Sidel PET aseptic line, which included a wet aseptic Combi Sensofill FMa, combining blow moulding, filling and capping in a single integrated system. The company then looked to further extend its production capacities. Recognising the potential that dry preform decontamination technology provides for further cost savings as well as the benefits it offers in environmental terms, Sidel proposed its Sidel Predis dry system, which replaces wet bottle sterilisation and is said to provide 100% decontamination of all preforms using hydrogen peroxide mist, removing the need for water and requiring only small amounts of chemicals. It protects the integrity and safety of any beverage - either high or low acidity - distributed at ambient temperatures, says Sidel.
PT.Hokkan Indonesia decided to adopt this technology for its second Sidel aseptic line. Ikezawa continues - “Our wet aseptic line currently produces milk coffee, milk tea, Matcha, isotonic beverages and teas in six different bottle shapes and in sizes ranging from 250 ml to 500 ml (a total of 15 stock keeping units). The dry aseptic line will produce the same product range, with the ultimate intention of being able to run all bottle sizes on both lines to maximise the flexibility in production. With both lines able to run at speeds of up to 40,000 bottles per hour on all formats, this has more than doubled our total annual production capacity.”
PT.Hokkan Indonesia has also been working closely with the Sidel team on the design and development of new bottles. This includes a focus on lightweighting opportunities, with the collaboration ongoing for the 500 ml bottle to further reduce its weight.
Although the purchase of healthy beverages, such as sour milk drinks and sports and energy drinks, is not yet common practice among Indonesian consumers other than the younger generation, increasing awareness of health issues, accompanied with rising disposable income, is stimulating a change in habits. PT.Hokkan Indonesia expects naturally healthy products, including speciality Asian drinks, powder concentrates, fruit and vegetable juices, functional drinks and teas to grow significantly in sales over the coming years. Packaging formats in the country tend to be ‘single-serve’ now, with most drinks packaged in PET bottles. Demand for returnable glass bottles has declined substantially in recent years, mainly through one producer switching production from glass to one-way PET bottles. The increasing use of PET is down to a number of factors: its 100% recyclability, excellent barrier material properties that allow extended shelf life, bottle design freedom and the greater brand recognition possibilities offered by the package transparency. Being re-sealable, light and compact, the PET bottles are also more convenient for the customer as they do not have to be consumed at one time and are far more suited to the dynamic urban lifestyles of younger Indonesian consumers. The addition of the second aseptic PET bottling line to its production facility will enable PT.Hokkan Indonesia to maximise the opportunities that these market trends offer.
Sidel to cut down staff by 10%
Meanwhile, Sidel will introduce a more streamlined functional structure, in early 2016. As part of this planned reorganisation, Sidel intends to move its headquarters from Zug, Switzerland, to Parma, Italy, its centre for complete lines and filling. The intended transfer is to take place during the course of 2016. The move will result with a 10% reduction of positions across Sidel's global business, affecting 360 employees. It is currently actively engaged in discussions with appropriate employee representatives to work through the planned changes.
Explaining the reasons for the changes, CEO Mart Tiismann, commented: "These planned changes are part of our long-term strategy to focus on delivering the world's best PET complete line solutions and equipment. We want to ensure that we will continue to provide our customers with the very best support to help them succeed, in a highly competitive market, today and in the future."
Cost savings will be reinvested back into the company, says Sidel, adding that it will be developing further technology.
(PRA)Copyright (c) 2015 www.plasticsandrubberasia.com. All rights reserved.