Also, download this story from the electronic issue here
With the industry under pressure to increase recycling targets, highlighted are a research into automated sorting of regrind; a case study of a recycling partnership in Europe; a brand owner’s entry into the commercial recycled materials market and new PCR grades for the automotive sector.
Sustainability in the plastics sector includes the recycling process, with materials that are produced to be on par with the performance and cost efficiency of virgin materials. This, besides brand owners and OEMs fulfilling the rising end-user demand for materials and applications with enhanced environmental sustainability.
Automated sorting of regrind to be feasible
Researchers at the LMU University in Munich, Germany, have developed a new process for automated identification of polymers, facilitating rapid separation of plastics for re-use.
The new patent-pending technique involves exposing plastics to a brief flash of light that causes the material to fluoresce. Photoelectric sensors then measure the intensity of the light emitted in response to the inducing photoexcitation to determine the dynamics of its decay. Because the different polymer materials used in the manufacture of plastics display specific fluorescence lifetimes, the form of the decay curve can be used to identify their chemical nature.
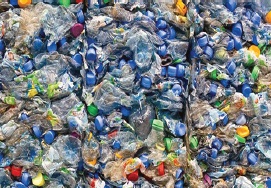
Unless the sorted material is of high purity, reheating of recycled plastic in the reuse process, can, however, lead to alterations in its properties. Contamination levels as low as 5% are sufficient to significantly reduce the quality of the reformed product.
Since polymers tend to be immiscible , as they are chemically incompatible with one another, remelting of polymer mixtures therefore often leads to partitioning of the different polymers into distinct domains separated by grain boundaries, which compromises the quality of the final product. For this reason, high-quality plastic products are always manufactured exclusively from virgin grades and not from recycled material.
The new method, however, could change this since the use of fluorescence lifetime measurements permits the identification and sorting of up to 1.5 tonnes of plastic/hour, thus meeting the specifications required for an industrial scale process.
A 100% film from PCR – partners work hand-in-hand
For an efficient recycling plant, machine makers usually work together to ensure a competitively-priced end-product ensues from the waste.
Size reduction equipment supplier Herbold Meckesheim, together with Austrian recycling equipment supplier Erema, designed a plant for Poligroup in Bulgaria, which has been in operation since September 2013.
It produces 30-micron film made from post-consumer recycled (PCR) content, such as LDPE agriculture film waste, LLDPE agriculture film waste and household waste film, obtained from automated sorting plants. The reason for this mix is that the LDPE forms a homogeneous material with an unchanging melt flow index (MFI). The LLDPE improves the physical properties, and the household waste-film is a competitively priced material.
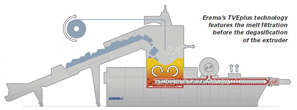
To recycle waste from different types of films, the process becomes more complex. Almost 50% of the agricultural film is contaminated with sand, pebbles, as well as small screws. In order to separate this, Poligroup uses downstream equipment: size-reduction in the washing line and a pre-washing unit.
Meanwhile, household waste film is a mix of several different plastics and the real challenge is the separation of unwanted plastics. This is where Germany-based Herbold’s expertise comes in as it is said to be the only wet film recycling equipment supplier that has hydro-cyclone separation able to achieve this. Plastics that are heavier than water will be separated from plastics that are lighter than water.
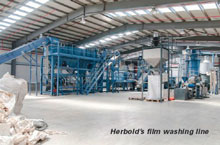
A further advantage of this method is that the high amount of water used, together with the revolving forces of the hydro-cyclone, ensures that the recyclate film is given a very good washing. Furthermore, organic deposits are easily removed by washing. In contrast, LLDPE films from consumer packaging often come with labels and it is a real challenge to remove them, more so since LLDPE films are ideal as a feeding material for recyclate used for the production of new film.
Economically speaking, only certain waste can be used for recycling and that is one of the reasons why a plant manufacturer and operator usually work hand in hand.
The parties say that an existing collection and separation system is ideal. Without this, a recycler can only use recyclate that has been imported from countries where the waste materials are collected and recycled. It is also possible to collect mixed post-consumer waste and to separate it. But this is expensive and the quality of the recycled material will be affected.
The washing line at Poligroup’s site transforms agricultural films and consumer packaging films into recycled material that will then be used for the production of bin liners, protective sheets and construction sheets.
The end-products do not include any virgin resins, and are made of 100% recycled plastic material from the Herbold film washing line.
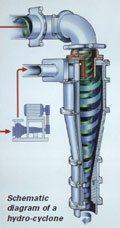
The film recycling plant uses some 0.8 to 1.0 MW/ tonne of power , whi c h corresponds to 0.8 to 1.0 kW/kilo of end-product. The water is also continuously reused. Thus, only 1 to 2 cu m of fresh water/ tonne/material is needed for the regeneration of the circulation water.
Also, in terms of maintenance, at tent ion has to be paid to wear-prone areas, with exchangeable anti-wear plates.
Poligroup’s decision to purchase the Herbold washing plant, with its prewashing unit and hydrocyclone separation, was also due to its high variability, since it is able to cater to highly contaminated and thin films.
The washed and recycled film flakes are then treated with Erema’s TVEplus (1,100-1,200 kg/hour capacity), with LF2/350 laser filter (filtration fineness of 110 microns) and the HG 244 die-face granulating system. Erema says its TVEplus is able to cater to waste with a residual humidity of between 8-12% as well as a high degree of contamination.
At the core of the plant, on the multifunctional cutter compactor with patented air flush module, the material with still a small amount of residual humidity and remaining contamination is optimally recycled. Thus, cutting, homogenising, heating, degassing, densifying, buffering and dosing is able to be undertaken in a single step.
Poligroup also says the advantages of Erema’s equipment are the “easy handling and long service life of the wear parts such as filter screen and pelletiser knives.”
Sony to extend Sorplas to external use
In 2011, electronics maker Sony Corporation’s research on electronics found that electronic devices contained less than 60% content of f i re- retardant regr ind. Taking this cue, it decided to develop its own Sorplas (Sustainable Oriented Recycled Plastic) material, a flame-retardant recycled polycarbonate (PC) recovered from discarded DVDs and optical sheets (light-diffusing films) used in LCD televisions. It contains Sony's own unique sulphur-based flame retardant to achieve a “highly durable, highly heat-resistant plastic” that uses up to 99% recycled materials.
Sony adopted the material in i ts Bravia LCD televisions in 2011, and later on incorporated it into a wide variety of Sony products. Now, it will be offering its Sorplas grade to external use, outside of its group.
Conventionally, flame-retardant recycled PC contains around 55% virgin material and approximately 15% flame retardant. However, Sony says its material is able to achieve flame resistance equivalent to conventional flame retardants but with only 1% addition of flame retardant. This allows the properties of PC to be retained and a higher proportion of recycled materials can be used as a result, while still achieving the properties required. The firm offers three types of grades with various additives: SPL-EC30 – an easy to mould grade; SPL-EC50 – a high impact grade and SPL-R20T – a flame retardant grade. The firm will offer all the three grades at prices similar to conventional PC.
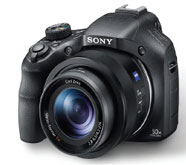
New PCR grades for the automotive sector
Over the past decade, sustainability has been an increasingly important driver of innovation in the automotive industry. Thus, Austrian polyolefins supplier Borealis has introduced three new Daplen PP compound grades composed of PCR and virgin content conceived for interior, exterior and under-the-hood automotive applications.
The new grades will support OEMs and Tier 1 suppliers in their efforts to increase the use of recycled materials, whilst at the same time not compromising on material characteristics, says Borealis.
The three new grades are:
- Daplen ME225SY: with 25% PCR content, 20% talc and 55% virgin material for interior automotive applications such as door and trunk claddings and trims.
- Daplen MD250SY: with 50% PCR content, 20% talc and 30% virgin material, for UTB and exterior applications such as bumper components and exterior trims.
- Daplen MD325SY: with 25% PCR content, 30% talc and 45% virgin material for use in UTB and exterior applications.
For now, the three new Daplen grades are being produced, launched and marketed solely in Europe.
"We see a clear trend towards the use of recyclates together with virgin materials," explains Jost Eric Laumeyer, Borealis Global Marketing Manager Engineering Applications. "Today, answering the call for materials with increased sustainability and increasing resource efficiency is no longer an aspiration, but a business imperative for the automotive industry," he added.
(PRA)