Italians will again form a large contingent at the upcoming K2013 show in Düsseldorf, Germany, taking up 26,000 sq m of space at the exhibition, which will be held from 16-23 October.
Macchi’s COEX5 POD 2600
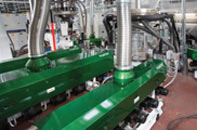
In the current times though certain industry segments are down, but the flexible packaging sector is carrying on with its regular business.
What’s changing is that, over the past years, many improvements have been made to the traditional monolayer and simple coextruded film machinery market. Moving to coextruded structures allow to combine significantly improved shelf appearance with good mechanical resistance while maintaining optimal performances. Additionally, coextrusion allows downgauging since it can provide stiffness and film strength combined with excellent holding force. End users and brand owners know that they can do more with less, at improved production efficiency, and they may expect a tendency change from their traditional suppliers.
Extrusion machinery maker Macchi’s COEXflex 2600 five-layer line on display can be described as a five-layer coextrusion of the “POD concept” (POD= Poly-Olefin Dedicated), designed to be a sustainable system to produce at high output rates, thinner and better films.
The details of a machine concept that covers so many aspects of the film coextrusion technology do not exclusively address shrink films but flexible packaging and web converting as well, as all may benefit of the very same advantages, says Macchi.
This is why the coextrusion platform is engineered to coextrude a 1-2-4-2-1 structure through a 500-mm die achieving – depending on selected formulations - output values in the range of 900-1100 kg/hour, according to the firm.
New design and concept features will be presented at the show, some of them being an “absolute” first, such as a new cooling ring and IBC anti-block arrangement, which is being under tight wraps.
On the hardware side, the five-layer coextrusion line that Macchi will present is not a “revised and adapted” barrier line. Since inception, these lines have been designed to process polyolefin, meaning that from screw design and die geometries these are “mission-specific projects”, says Macchi. The key advantage of a five extruders system is in the possibility to re-design a film structure without the limits and the burdens of a traditional approach.
“The new output and production control enable customers to get the most throughputs from the capacity of its equipment, tools, and employees. Reducing downtime, make-ready and increasing yields can result in an effective gain in plant capacity.”
Macchi will have a number of distributed electronic features, enclosed in the recently unveiled Easy Control 4 Profinet man-machine computerised interface to achieve a perfect control of all the parameters.
“When running a coextruder in the capacity range of 1 tonne/hour, the key is to control and reduce energy consumption per unit of production, determine the primary factors that impact energy efficiency of machinery and capture and manage critical quality-related events. Better understand of the energy requirements of your complete production process increase traceability, data accessibility, transparency, and reporting accuracy.”
EPS insulating boards
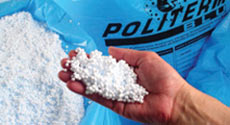
Started up in 1981 by Paolo Stabellini, Modena-based Edilteco supplies technologies for EPS thermal insulation. "Years marked by an endless research on concrete and polystyrene led us to develop technologies that did not exist, targeted at sustainable and energy saving buildings,” said Stabellini. He added, “Companies can therefore buy turnkey production lines of materials for the thermal insulation of buildings.”
The firm counts Algeria, India, Romania, South Africa, Tunisia, Sweden and Turkey as some of its markets. It has also set up offices in Belgium, France, Spain and Argentina.
It will showcase Politerm Blu, said to be a superlight material made up of EPS and an additive (Edilteco Insulating Additive). The firm says it has “conquered the China market, where we will soon be expanding production to ready mix mortars (Politerm Blu + cement in one bag).”
In black and white from Bandera
Extrusion machinery maker Bandera will showcase a fivelayer coextrusion line for the extrusion of white and black (PE or barrier) film with symmetrical structure and with coPA or EVOH barrier in the middle layer, and also for lamination and flexible packaging.
The line being shown will feature:
- dosing unit with loss in weight continuous metering system, with the possibility to work with 20 components
- TR50 single-screw extruder, TR65 four-side single screw extruder, with AC motors for low energy consumption; bimetallic barrel, thermoregulated feeding zone
- spiral die head with side feeding, with 400 mm diameter die featuring inside flow distributors that allow for optimal results in output at low pressure and fast material change (blend or with masterbatch)
- IBC equipped with eight different sensors, which analyse all the parameters, also including atmospheric conditions, thus allowing to manage the proportional IBC control valve through the software (integrated in the Bandera line supervisor), for a total bubble stability
- double station winding centre: with back-to-back configuration and operational method according to the film size to be produced: surface winding, axial winding (with or without gap control), combined winding as well as counter-rotation winding. Film tension control is realised through highly sensitive loading cells.
- Siemens electronics, with extruders and die head thermoregulation directly managed through PLC, together with Profinet network. The wiring is noticeably reduced, with the result to ease the electric and electronic maintenance. The extrusion line is controlled by one computerised system that allows a centralised management of all the production and operation parameters.
Energy saving thermoformers
Swiss thermoforming machinery maker WM Wrapping Machinery, which is part of the Meico Group, will display a vacuum FC 780 E IM2 thermoformer, from the Speedmaster Plus series. It forms and cuts, using a steel rule die, all in the same forming station. It is equipped with a second cutting press for equipment that requires a second cutting step. In addition, the machine is equipped with a three-axes robot for counting, stacking (with A-B or A-B-C sequences) and removing stacked products.
The thermoformer can carry moulds up to 780 x 570 mm, with the forming unit generating a closing force of 75 tonnes. The standard versions come equipped with motorised height adjustments for both the lower and upper fixed platen. Thus, it can carry moulds with different heights, without the need for adapter plates.
The platen movements, guided on four columns, of the first forming/cutting press and of the second cutting station, are achieved with servomotors that independently drive a double toggle system.
The Stabio-based firm says that motors and drives that are rationally designed, together with an accurate management of the acceleration and deceleration ramps, result in a significant reduction in energy consumption during the production cycle. Also, the use of regenerative modules, during the braking phase of the surface movement, transforms kinetic energy into electrical energy. This energy is returned to the machine's power supply and is used in the thermoforming machine for other applications, instead of being dissipated as heat.
Again, with regard to energy savings, a multi-stage Venturi system is used to create a vacuum, instead of the traditional vacuum pump. It consumes energy only when the vacuum is used during the cycle, in contrast to a pump that operates during the entire production cycle. The heating ovens, with independent longitudinal row adjustments, allow also the individual adjustment resistors, as well as a series of possible partialisations, that can vary depending on the pitch and the type of material to be processed.
An infra-red pyrometer, for reading sheet temperature, is housed in the lower heating oven. With a closed loop circuit, it helps adjust/correct the set temperatures while taking into account environmental variations. This maintains constant the temperature of the sheet.
The forming station is also equipped with a servomotor unit to drive the deep-drawing, which pre-stretches the sheet.
The machine will be displayed with a mould for an APET double eggs container.
The second display from the Desmoformer series is the FT 500 simultaneous form-cut machine with lower tilting platen for moulds up to 570 x 375 mm and a 30 tonne cutting force. It is also equipped with a servomotorplugging system, stacking system with rotating plate used for the removal, count and single row stacking of the thermoformed products.
Especially interesting is the tilting unit of the lower platen, which can rotate 75 degrees. The system uses a combination of servomotor-driven cams and levers and based on an innovative double desmodromic system. This ensures maximum precision and repetition of movements, as well as power calibration during both the movement and cutting phases.
The thermoforming machine will show a 22-cavity mould for a PP conical container with flat edge.
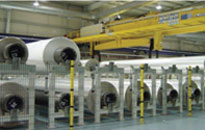
Software for managing blown films
Industrial solutions firm Bonfanti will present a new MES software for the film sector. It can be integrated with the main cutting and scheduling applications and with the main ERP systems, for the complete management of the production tracking and labelling, product traceability, quality management and data collecting.
It will also showcase its automatic handling, storing and packing systems for metallised rolls as well as for packages and labelling systems.
Electric EBM for cosmetic bottles
Extrusion blow moulding (EBM) machine maker Plastiblow will exhibit the servodriven double-station PB10E/DXL. It features a 800 mm mould holder stroke, 100 mm extruder diameter, 300 kg/hour plasticising and a 24-tonne clamping force. It will be producing cosmetic bottles with six cavity moulds on each side and 120 mm centre distance. The extrusion head permits quick colour changes, said to be less than half hour using multi-cavity heads.
A servodriven-three axes robot will pick up the bottles after deflashing and place them on a linear belt conveyor. The machine will also be equipped with an in-line quality control device for the bottles, to check for micro-holes, deformation and obstruction of the neck; including the detection of sprues.
System for removing bottle sleeves for full recycling
Machine maker Amut will promote its de-labelling (DLB) system for post-consumer PET bottle recycling that allows the recovery of PET bottles with PVC or PETG full body sleeve labels; and almost total detachment of the labels, with up to 100% recovery of bottles with full body sleeves.
The labels are removed dry in a continuous process and the bottles conveyed on a conveyor belt and, after treatment, discharged continuously with a screw feeder extractor. The labels are collected in an underlying hopper and conveyed by belt to a compacting press or a container. The separation of any remaining labels from bottles can take place downstream through an air system or a “rotary ballistic screen.”
DLB60 and DLB30 are suitable for treating the entire flow of bottles at the beginning of the washing line while DLB10 can be installed downstream, to treat the rejected bottles from the main NIR sorter.
Piovan wins at leading car maker and obtains patent
At German car maker BMW’s facility, auxiliary firm Piovan supplied two Modula auto adaptive drying systems with multiple hopper assembly. Launched in the market in late 2010, the auxiliary systems supplied to BMW, automatically adjust and control all operating parameters for each individual hopper and hence use only the overall amount of energy strictly required. This is made possible through a specific control software that interfaces the settings for each hopper with the data collected by the sensors installed on the system.

This means that, by using a Piovan patented airflow measuring device, located in the air supply line and at each hopper, the airflow can be adjusted and controlled instantaneously and individually, hopper by hopper. In addition, the total airflow is modulated automatically and efficiently by the central drying unit, equipped with IE3 class blowers, resulting in optimum process operating conditions.
The materials utilised by BMW are mainly blends, with PP or PC base, like PP/EPDM and PC/SAN. The plastic part is first injection moulded and transferred to the painting lines, a sensitive phase of the production process where silicone particles are banned. One very important feature of Modula is the absence of silicone components/parts within the system.
Two sets of Modula were supplied, each configured with single dry air generator and seven drying hoppers with volumes ranging from 600-1,000 l.
The purpose of hygroscopic plastic drying is to reduce moisture content to the required levels. This operation is generally performed by circulating hot dry air inside a drying hopper.
In the case of applications that involve a number of materials of different kinds, a central unit is commonly used to generate dry air, which is then distributed to a series of hoppers, one for each material type, through a duct system. Each hopper requires specific conditions for optimum operation (dry air flow, temperature and pressure) depending on the different material characteristics, such as the type, the required initial and final level of moisture, the hourly material consumption and the granule size.
Modula is available for medium and large capacity applications (200-2,000 kg/hour) and provides energy savings of as much as 50% with respect to ordinary centralised drying systems of equivalent capacity. Modula is Winfactory ready.
Along with Modula, BMW was supplied with Varyo auto-adjustable vacuum conveying systems, MDW gravimetric blenders and Winfactory supervisory system, all Piovan products.
Moretto to showcase new products
Auxiliary manufacturer Moretto says it will be a “container of Italian ingenuity with a new range of products”. Amongst the launches are:
- One Wire 6 (OW6), a self-adaptive and automatic control and management for centralised conveying systems that does not require time and parameters to be set.
- New Teko temperature controllers with increased working temperature but still using water as the medium for heat exchange.
- DGM Gravix gravimetric dosing with the Vibration Immunity System (VIS).
- OTX (Original Thermal Exchanger) with an internal geometry to solve material flow-down problems, using 40% less time and energy compared to standard hoppers.
- Eureka dehumidification system when combined with OTX and two other Moretto technologies features XMax and Flowmatik. The modular XMax dryers cater to up to 32 OTX units. Flowmatik is an integrated automatic system for distributing the process air for OTX systems.
(PRA)