Flexible packaging: sorting out the recycling issue
Also, download this story from the electronic issue here
Innovative packaging designs for easier sorting are being sought as the initial basis for effective recycling, says Angelica Buan in this article.
Flexible packaging offers many benefits: it uses less energy and materials than other packaging options, helps extend food shelf life and minimise spoilage, and reduces waste by preserving and protecting products until they are consumed.
With the benefits offered, flexible packaging has outpaced the utilisation rate of other packaging formats like metal, carton, glass or rigid plastics. UK-based Smithers Rapra, in its report titled The Future of Global Flexible Packaging to 2018, expects global consumption to grow 3.5% annually over the next five years, reaching US$231 billion by 2018.
But with the popularity of flexible packaging also follows the issue of recycling, and the issue of recyclability starts from the packaging producers. It is because of the environmental implications attached to consumer packaging that it adheres strongly to corporate sustainability.
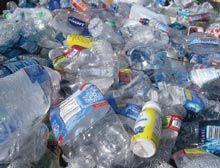
The Organisation for Economic Co-operation and Development (OECD), in its presentation at a conference in Belgium in 2010, Global Forum on Sustainable Materials Management, stated that of the huge volume of waste generated, 60% comes from packaging. A report from Worldwatch Institute, a US-based organisation that tracks key trends in energy, environment, transportation, food and agriculture, economy, and society to inform and inspire the changes needed to build a sustainable world, states that packaging accounts for more than 40% of plastics use.
While production of packaging has skyrocketed, recycling of discarded packaging is lagging behind. It is also made more difficult as some types of plastics are harder to recycle than the others.
Moreover, recycling rates in countries vary. In the US, where there are existing recycling facilities for plastics, only 9% of its waste plastics were recycled in 2012.
The United Nations Environment Programme (UNEP) estimates lower plastic recovery rates for other countries, whereas a high percentage of waste is not collected “but instead littered or burnt in the open”, in Africa (57%), Asia (40%), and Latin America (32%).
Materials are hindering factors
A wide array of polymers are being utilised now for flexible packaging. Some of the most common types are: PET or metallised PET, BoPET, HDPE, PVC, LDPE, LLDPE, PVDC, BOPP, CPP, PS, PP and biopolymers. The common applications for these polymers are flexible beverage containers, metallised foil pouches, twist or cling wrap, blister packs, vacuum packaging for pre-cooked meals, and shrink sleeves, to cite a few.
According to the report, Waste and Opportunity 2015: Environmental Progress and Challenges in Food, Beverage, and Consumer Goods Packaging by non-profit organisations As You Sow and the Natural Resources Defence Council (NRDC), the biggest challenge for building up recyclability and compost ability of packaging are the type or materials used. An example is beverage packaging that is increasingly making use of laminated pouches, shrink wrap, and other flexible plastic packaging, which cannot readily be recycled.
Researching on cracking effective recycling solutions
A recent study, initiated in the US by the Research Foundation for Health and Environmental Effects (RFHEE), a tax-exempt organisation established by the American Chemistry Council (ACC), is aimed at recovering more packaging that is currently destined to landfills as well as investigating the efficacy of existing sorting systems to recycle flexible packaging.
It is backed by a number of key packaging stakeholders including Dow Chemical, PepsiCo, Procter & Gamble, Nestlé Purina PetCare and Nestlé USA, Sealed Air, and SC Johnson, as well as the Association for Postconsumer Plastic Recyclers (APR), the Flexible Packaging Association (FPA), and the Plastics Industry Trade Association (SPI). It, thus, brings together brand owners, manufacturers, and packaging industry organisations that are committed to enhancing recovery solutions for increasingly popular flexible film and packaging options.
The project called Materials Recovery for the Future (MRF) aims to probe the available sorting technologies, including screens and optical scanners, in separating flexible packaging from the mix, such as resealable food packages, pouches for soups, pet food bags, and snack bags.
Jeff Wooster, Global Sustainability Director, Dow Packaging and Specialty Plastics, said, “This new sortation research is critical in helping to close the recovery loop for flexible packaging and we are committed to this collaboration to drive solutions for increased recovery rates.”
Conducting the pilot phase of the research is the test methodology developer Resource Recycling Systems (RRS). It will include baseline testing of the existing sorting technologies commonly used in material recovery facilities, such as screens and optical scanners. A representative mix of the flexible packaging generated by consumers will be created and added at an appropriate concentration to single stream recyclables for testing. This mixed stream will be run through the sorters, and the amount of flexible packaging captured in the resulting bale will be measured to determine sorting effectiveness.
“The research is first to use this methodology to study the movement of films and flexible plastic packaging at material recovery facilities in the US. The data from this collaborative research will help us learn how to recover and divert more valuable resins from landfills,” said Diane Herndon, Manager, Sustainability, Nestlé Purina PetCare.
The research is ultimately hankering for the creation of a mainstream recovery solution for flexible packaging. The project proponents are expecting to release the research outcome in the second quarter of 2016.
Meanwhile, the Flexible Film Recycling Group (FFRG), a division of the ACC, is also aiming to significantly hike up the collection and recycling of all flexible films. FFRG comprises major industry players from the entire PE film value chain. Its current members include Chevron Phillips Chemical Company, Dow Chemical, Procter & Gamble, SC Johnson, and Wegmans Food Markets, to name a few.
Investing in recovery systems
The MRF is not the sole study on flexible packaging recovery. Already, numerous undertakings have been funded and carried out by major proponents.
One of these is a fund by UK’s Department of Environment Food and Rural Affairs (DEFRA) that has a specific purpose for improving collection rates of flexible packaging materials, especially packaging containing aluminium (such as toothpaste tubes).
The fund was given in 2014 to a consortium formed by Anthesis LRS, a UK-based sustainability consultancy, in partnership with Enval, Sita UK, Nestlé UK & Ireland, Coca-Cola Enterprises and Tesco UK. The group is tackling flexible laminate packaging, which can contain aluminium and various recyclable plastics that can be challenging to collect and separate for recycling. Among the desired outcomes for the 18-month study is to determine collection solutions and test their viability.
Hatching a unique process for recycling plastic laminates containing aluminium, technology specialist Enval is working with stakeholders to recover as much aluminium as possible. The packaging that is collected will be treated at Enval’s facility near Huntingdon, where the plastic and aluminium will be separated. Dr Carlos Ludlow-Palafox, Enval’s Managing Director, commented that aluminium is highly valuable as it is a versatile material, therefore, “it is important to capture and recycle as much of it as possible.”
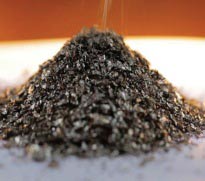
Last year, UK-based resource recovery specialist Axion Consulting led a collaborative project called Reflex that focuses on improving recyclability of flexible packaging, together with stakeholders Amcor, Dow Chemical, Interflex Group, Nestlé UK, Sita UK, Tomra Sorting and Unilever UK Central Resources.
Financed by the UK government’s innovation agency, Innovate UK, the two-year project aims to weave a circular economy for flexible packaging by encouraging participation from the entire supply chain – from polymer and packaging production to waste management and recycling.
According to Axion’s Director, Roger Morton, the project is expected to eliminate the factors that prevent flexible packaging from being recycled. Once that happens, recyclers will be able to close the loop by diverting waste from landfills.
Morton’s approach of effective recovery starts from the design of the packaging. He says that innovative recyclable flexible package designs and materials can enable simultaneous reprocessing of materials. The project will be innovating inks, barrier polymers, packaging designs, and an automated sorting technique.
Moving along the same objective is UK’s Plastics Industry Recycling Action Plan (PIRAP), a roadmap penned by Plastics 2020, a body comprising the Packaging and Films Association (PAFA), British Plastics Federation (BPF), PlasticsEurope and the Waste and Resources Action Plan (WRAP). The target is to ensure a 57% recycling rate, which is in sync with the government’s recycling target by 2017.
The roadmap features strategies to improve collection rates, optimise sorting infrastructure and develop end markets for plastic recyclates.
Waste prevention better than recycling
Pitching the approach that waste prevention is better than recycling is a report titled Potential packaging waste prevention by the usage of flexible packaging and its consequences for the environment, commissioned by Flexible Packaging Europe (FPE) in 2014.
According to resource person, Frank Wellenreuther of the German Institute for Energy and Environmental Research (IFEU), the game plan is slanted on the EU Packaging and Packaging Waste Directive (1994). The latter’s aim is “preventing the production of packaging waste and, as additional fundamental principles, at reusing packaging, at recycling and other forms of recovering packaging waste to reduce the overall quantities of such waste going to final disposal”.
It follows the European Commission’s resolve to use flexible packaging as a means to reducing the amount of primary packaging waste, before other approaches like reuse, recycling and recovery.
The report says that the amount of primary packaging waste that could be reduced by substituting non-flexible packaging with flexible packaging is 26.48 million tonnes/ year. This is more than 60% of the total annual amount of primary packaging waste in EU.
However, with the addition of layers into a flexible packaging structure to enhance its functionality and render cost-benefits, recycling has become an issue too complex for now to resolve in one sitting.
But as long as industry players continue to assert their social responsibility, clear solutions will be unwrapped in no time.
(PRA)Copyright (c) 2015 www.plasticsandrubberasia.com. All rights reserved.