Next extruders from WM
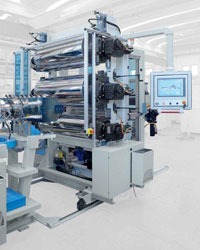
Thermoforming machinery maker WM Thermoforming Machines has introduced a new line of extruders line named N.EXT, said to offer higher productivity, energy savings, less cooling and less installed power, wear reduction, good self-cleaning and the use of a high percentage of regrind material.
The range of extruders include screw diameters of 45-75-90 mm, L/D (length/diameter) ratio of 36 and output capacity range from 450 to 900 kg/hour for PP material.
All the extruders are single screw operated by water-cooled AC motors for high-energy efficiency and low noise emissions. All cylinders and screws are made of nitride steel, but special versions made of bimetal and stellite (tipped hard metal) are available upon request, for the processing of filled materials.
The Swiss firm also says that particular care has been dedicated to the design of the screw profile in order to obtain a better and optimal homogenisation and plasticisation values of the material. The temperature control settings are made through the industrial PC B&R operated by touch-screen.
Special stainless steel covers protect the heating zones and can be easily removed for maintenance. All extruders are supplied with continuous hydraulic screen changers in order to avoid material flow interruption. A separate hydraulic power unit for the filter exchange can also be supplied to be used with other co-extruders.
A gear pump system is supplied as standard on all the main extruders to eliminate the possible pulsations during the melting process, guaranteeing constant and uniform feeding of the extrusion flat die head.
In case of additional extruders, a co-extrusion feed block is installed before the flat die head, in order to distribute the material flow in different layers in function of the sheet characteristics required for the final product.
The extrusion flat die head is provided of a flexible lip adjustable through nuts that works by pulling and pushing to control the sheet thickness, while the deckling bars adjust the sheet width manually.
The vertical calenders are available in different versions, according to the extruder and the required output capacity. The standard version is mounted on a rail while a motorized system provides the correct positioning during the operating cycle. The main structure of the calender is made of three chromed mirror-polished cylinders with the correct hardness degree. The three cylinders are installed on a vertical axis that are individually driven by means of a servomotor. The hydraulic pistons, on the other hand, activate the opening and closing of the upper and lower cylinder. Inside the cylinders, a special multi-principle spiral cooling circuit guarantees the best temperature uniformity on the surface, which is in contact with the extruded material.
The calender is completed by the draft gear made of two rolls located on a vertical axis. The lower roll consist of a chromed surface and is driven by a motor, while the upper roll is rubber coated. Opening and closing operations are achieved by pneumatic pistons. All calenders are supplied with a thermoregulation central unit with three independent circuits. A separate air-conditioned control cabinet completes the extrusion line with easy access for the operator.
The machine parameters are displayed on the user-friendly touch screen operating panel by B&R including a USB port that allows all data storage.
(PRA)Copyright (c) 2015 www.plasticsandrubberasia.com. All rights reserved.