Erema to introduce RegrindPro for thick wall regrind at Fakuma
To enable recyclates to be used 1:1 as a substitute for virgin material, two crucial factors need to be taken into consideration. On the one hand, sufficient raw recycling material has to be available and, on the other hand, it has to be possible to process this material economically to make recycled pellets with customised property profiles.
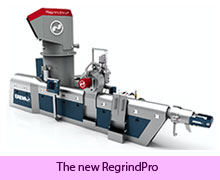
Thick-walled regrind has enormous potential in this respect as the input material for recycling – sufficient quantities are available and, above all, they are clean sorted. Reprocessing the recycled pellets from regrind without any problems and ensuring the functional properties of the end products which are made from them, however, requires a specific recycling process – one which conventional systems on the market have so far not been able to accomplish with due thoroughness.
Austrian firm Erema now has the solution for precisely this purpose: the new Intarema RegrindPro plant system for all types of thick-walled regrind material.
Recycled pellets based on regrind material are an excellent alternative to virgin material for plastics processors. Most of all because of the fact that regrind is easy to sort and separate and is thus available as a clean sorted input stream for the upstream recycling process. Raw material sources include thick-walled packaging such as HDPE blow-moulded bottles from the hygiene and cosmetic sectors and also thermoformed and injection-moulded articles made of polypropylene and polystyrene such as closure caps, cups, fruit containers and butter tubs. Plastics from waste electrical and electronic equipment (WEEE) and products from the automotive sector such as bumpers, battery packs, engine piping, etc. also have great potential in terms of reutilisation.
The material streams are, therefore, available in sufficient quantities for the use of recycled regrind as a substitute for virgin material and, compared to film, they are also available in a more clean-sorted form. Processors are, however, also interested in the rheological properties of these recyclates allowing trouble-free subsequent processing and the assurance of the functional characteristics of their end products. Besides the mechanical aspects, above all surface quality, dyeability and smell are decisive quality factors. This places particularly high requirements on the recycling process which commercially available systems have not always been able to meet so far.
Challenge: regrind recycling
Due to its high bulk density (200-600 kg/m³) and the fact that it is free-flowing, regrind is, as a rule, easy to dose in an extrusion system and requires no additional compacting and size reduction. The challenge, however, lies particularly in melting the thick-walled regrind particles in a gentle way, as they require more time to heat through and melt compared to thin films. With conventional treatment systems the regrind is dosed into the single or twin screw extruder via a hopper system. A longer processing unit is thus required to melt the cold regrind particles. This increases the residence time in the extruder and the melting process takes place under high shear stress. The polymer structure is destroyed in parts because of this, which has a negative impact on the mechanical properties of the end products. Additionally, the impurities appearing in the regrind material are also reduced in size through the impacting shear forces and filtration efficiency is decreased drastically as a result. Compared to the single screw systems, this effect is increased with the co-rotating twin-screw extruder through up to three times poorer filtration fineness due to the low pressure build-up. The cold-fed single screw systems lack the flexibility to handle the various regrind types such as HDPE and PP with the same quality requirements economically on one system. Additionally, moisture contents of up to 8% mean that energy-consuming pre-drying is necessary on both systems.
The specific treatment process in the recycling of thick-walled input material thus has to be designed to be able to work with different types of regrind (PP, PE, PS, ABS, etc.), with a wide variety of bulk densities and moisture contents, plus strongly varying contaminants such as impurities like rubber, silicone and soft contaminants like wood and paper, plus foreign polymers like PET and PA. These contaminants have to be removed effectively because more and more material is being saved in wall thicknesses also in the production of e.g. bottles and pipes, and the end products are thus more sensitive to defects through contaminants.
According to Erema, processors who use recycled pellets from regrind have to be able to rely on their end products having premium surface quality and that their mechanical properties likewise stay top class. “In order to be able to recycle in line with these criteria the recycling extruder has to be filled with thoroughly warmed regrind particles to ensure first of all exceptionally gentle processing and, secondly, high-performance filtration. And these are precisely the two key functions of our innovative RegrindPro technology."
RegrindPro technology
What makes RegrindPro so special is that unlike other systems the regrind material is heated through already prior to extrusion which increases both flexibility in material selection and filtration efficiency as a result. This is handled by the preconditioning unit which is optimised for the regrind and in which the material is processed in an extremely gentle way by means of a rotor disc with a special tool set-up. Thanks to the slow turning of this rotor disc the thick-walled, moist particles are efficiently dried and degassed with a high filling level and thus longer residence time. Long residence times in the preconditioning unit are important so the regrind is not only dried but also so it has enough time to be warmed thoroughly and homogeneously. An additional benefit of the longer residence time is that powder additives such as CaCO3 can be admixed in amounts up to 20% and, above all, be distributed well.
After the preconditioning unit the dried, degassed and thoroughly warmed material is dosed into the directly connected extruder and melted in the short universal screw with minimum shear stress.
Erema's Counter Current technology offers a further benefit here, which is crucial especially in terms of free-flowing materials such as regrind. This is made possible by the screw being filled virtually pressure-free and the fact that it only takes as much as is required at any one time. Furthermore, the melting process with minimum shear stress increases the cleaning efficiency of the melt filter as the size of organic or mineral solid matter is not reduced. This means that even contaminants such as wood and paper can be optimally filtered because, thanks to the gentle process, the fibres do not separate and they remain large enough to be discharged at the filter.
Through the combination of the optimised preconditioning unit with a new, particularly gentle universal screw, RegrindPro additionally offers a high degree of flexibility in the choice of materials, which enables multipurpose regrind processing. This allows the processing of regrind despite varying melting points and energy contents, as in the case of HDPE and PP, using the same system with full output and in a gentle way.
Once the material has been melted, the melt passes through the recently enhanced Erema Laserfilter. Thanks to the redesign of the scraper geometry and discharge system, contaminants are removed even more quickly which reduces fine particles and results in even better filtration performance.
Erema recommends the RegrindPro in a package with Laserfilter especially in the post-consumer sector: "Thanks to the optimised scraper geometry in the Laserfilter, rubber-like, non-melting contaminants such as silicones and linked polymers are removed quickly and continuously from the screen and thus filtered even more effectively." The firm explains further: "Additionally, the principle of Erema's patented TVEplus technology also comes into effect: melt filtration prior to homogenising and degassing. This removes any impurities from the system before they can outgas and prevents the formation of undesired smells."
The RegrindPro configuration can also be combined with Erema's recycling and compounding technology Corema. A way of producing customised compounds directly in a single step on the basis of regrind.
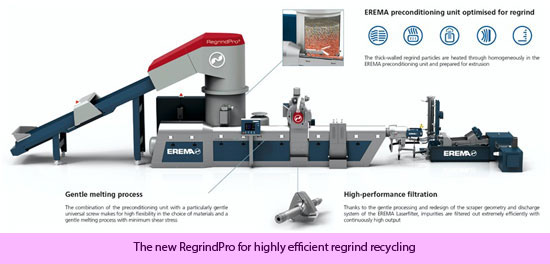
Comparison test confirms efficiency lead of RegrindPro
In a comparison of the filtration efficiency of conventional single and twin-screw systems with the new RegrindPro system, natural PP regrind from the same batch was used as input material on all systems and the respective recycled pellets were then processed to make sample films on an OCS film plant in the analysis laboratory at Erema.
The defects in the films are detected automatically in the process and then categorised according to size and the area of nonconformity is shown in cumulative form. With this sensitive testing method any impurities remaining in the recycled pellets are made visible and can thus be evaluated in terms of both quality and quantity. A large number of nonconformities caused by impurities in the test film also has a negative impact on the subsequent processing of these recycled pellets and leads to mechanical and optical defects in the end products.
The comparison documents the respective defect analysis for the test films produced from the different recycled pellets and shows the cumulative defect area share as a function of the defect size. In contrast to the other technologies the curve for RegrindPro already begins to flatten at nonconforming sizes of 400-450 µm and stays at a constant nonconforming area share of approx. 300 ppm. With the cold-input single and twin-screw systems tested, however, the curve rises and with it the nonconforming area of the film increases throughout the entire area measured significantly to over 1000 ppm. The comparison shows that the recycled pellets produced with RegrindPro are filtered much better and contain significantly fewer and, above all, fewer large impurities. This difference in quality is already visible to the naked eye when you see the film sample. And it is precisely this difference in quality which has an effect on surface quality in subsequent processing of the recycled pellets to make e.g. piping, bottles, automotive parts etc.
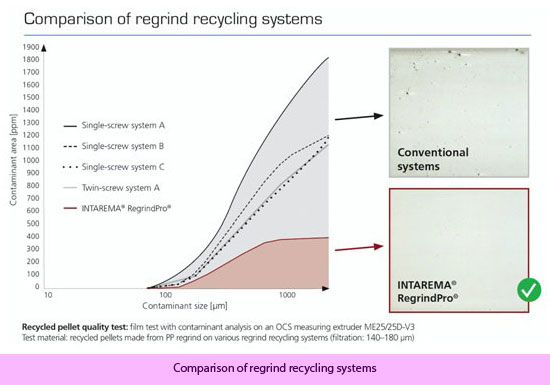
(PRA)
Copyright (c) 2015 www.plasticsandrubberasia.com. All rights reserved.