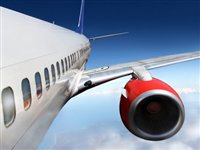
Germany-based chemical firm Evonik Industries plans to build a new plant for its Rohacell polymethacrylimide (PMI) structural foams in Shanghai, China, scheduled to begin operation in the fourth quarter of 2015.
"Our investment in Shanghai reflects a strategic decision to bring our products closer to the customer, as well as our continued commitment to a region that is a key growth market,” said Dr. Joachim Leluschko, Head of High Performance Polymers Business Line at Evonik.
Currently two plants - in Darmstadt, Germany, and Mobile, Alabama, US, – supply customers in Asia. The new facility will be located in Evonik’s Multi-User Site China (MUSC) in Shanghai Chemical Industry Park (SCIP).
Rohacell is already being used in Asia’s aviation industry, including the regional jet ARJ21-700 and also the prototype of China’s first large commercial airliner C919 that is scheduled to enter commercial service in 2018. The high performance foam cores are ideal for the growing advanced composites industry and are enjoying increasing worldwide demand in not only the aviation industry, but also in automotive, electronics, medical technology and sporting goods.
Airbus to use the new material
Meanwhile, Evonik wants to open up new markets for its Rohacell Hero in the aircraft industry. It is already used in many landing flaps, winglets, and fairings on airplanes. In the past there have been limitations in applications where safety is paramount and where parts are exposed to extreme temperature fluctuations and high levels of mechanical stress, such as rudders or landing gear doors. Until now, only honeycomb composites were able to meet these demands.
Now, Evonik says its material can withstand even extreme changes in temperature and high mechanical stress, thereby fulfilling the requirements for external aircraft components where safety is a significant factor. As Joachim Leluschko, Head of Evonik’s High Performance Polymers Business Line, explains, "Weight is a very important issue in aviation and the industry is therefore searching for lightweight solutions."
PMI is usually used as a core material in sandwich structures, which consist of a lightweight core and two thin layers of fibre-reinforced composite material. It is said to be the only foam that is able to withstand the processing conditions found in the production of sandwich components, which sees temperatures of up to 180°C and pressures of up to seven bar.
With Rohacell Hero, Evonik says its researchers have succeeded in developing a PMI structural foam which has an elongation at break that is three times higher than standard materials. As a result, even at temperatures of below minus 55°C it is just as mechanically resilient as comparable honeycomb structures. If damage is caused, for example, by foreign objects being hurled up from the runway, sandwich structures made with this foam exhibit visible dents, which remain local and do not spread.
This means that Hero meets the aircraft industry's stringent requirements, which for safety reasons stipulate that any damage must be visible. The necessary tests, including fatigue tests, were conducted by the Fraunhofer Institute for Mechanics of Materials in Halle (Germany).
The fine-pore material allows complex components to be produced much more easily and more accurately. A weight and cost comparison that Evonik carried out together with an Airbus parts supplier and Airbus subsidiary, Composite Technology Centre (CTC), came to the conclusion that components made from the new structural foam are, on average, about 10% lighter and cost about 20% less to produce than honeycomb structures.
Evonik offers Hero in four different types in varying densities. This range covers applications that are not subject to high stress, as well as weight-sensitive applications and parts that are subject to extreme mechanical stress.
At Airbus, experts have been subjecting the optimised material to thorough tests for two years. At present, the aerospace group expects the first components made from the material to be produced in series in 2015.
(PRA)