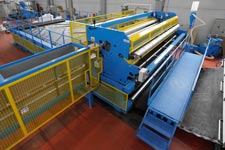
Amut, an Italian extruders and plastic extrusion machines specialist, has recently manufactured and tested a plant for the production of HDPE dimpled sheet, which measures a net width of 4 m, for a Russian customer, being one of the biggest producers of materials for the building sector.
The HDPE dimpled sheet is largely used to protect and provide drainage for the underground walls and it is the latest solution for the proper protection and ventilation of the waterproofing mantle between cement foundations and ground, according to Amut, adding that its versatility makes it essential for the realisation of buildings in zones where water presence is particularly high.
The line has a capacity higher than 1,700 kg/hour and it offers the possibility to produce articles using all 4,000 mm ; or by applying a central cutting, to obtain two coils of 2,000 mm each, or even four coils of 1,000 mm each (a coil maximum diameter of 490 mm).
The linear kinematic speed is equal to 12,5 m/minute, while the thickness range varies from 350 to 1,000 g for every sq m.
The line, based on an EA 180 single screw extruder with L/D 45, is able to process material in granules as well as trims/flakes or post consume HDPE bottles, and ensures uniform feeding, even when processing raw materials have different granulometry.
The line is composed of the following sections: loading system; raw materials dosing unit, single screw extruder with a plasticisation capacity of more than 1800 kg/hour and equipped with a vacuum vent system with closed loop circuit for water, used in case of material coming from post consume bottles at the extraction of volatile components; continuous screen changer with increased screening; gear pump with high pressure, capable to process also potential types of polymers; with a high molecular weight; flat die with melt exit width higher than 4.300 mm, so perfect to produce the maximum width even on low potential thicknesses of the finished product (< 300 g/sq m).
It has a special calendering/forming group with particular solutions. Such width, combined with the linear speed demanded by the contract production guarantees (10 m/minute of finished product), requested an accurate study of the two main forming rolls cooling flows made by means of recirculation/thermoregulation pumps; as well as a system for forming vacuum distribution capable to satisfy the different needs connected with the requested types of finished product.
Since the line can process 100% of post consume material, even the vacuum group had to be designed with condensation/reduction systems for the extrusion fumes, which are potentially present as a pollutant in the melt and certainly problematic in the vacuum circuit.
Downstream the calendering/forming unit, an unwinding/lamination station has been installed to allow the introduction of 4-metre wide geotextile materials. This station is complete with a distribution system of the hot melt glues used for different support/reinforce materials adhesion.
The end-line is composed of an automatic winder complete with a bench for the finished coils unloading/stacking.
The plant is also equipped by complementary and ancillary equipments such as a group for the bilateral unwinding of the advertising/signalling strap directly applied during the forming phase; a grinding group for trims complete with a transport system to convey the ground material directly in the raw material loading/mixing zone.
A proprietary software, developed and tuned specifically for this line particular exigencies, controls and checks all activities and parameters, by storing and monitoring the whole production process.
(PRA)