Also, download this story from the electronic issue here
Indonesia’s rise to become the world’s tenth largest economy, contributing 2.3% of the global economic output, according to the World Bank, has not been easy. Much like its ASEAN neighbours, the country has been riddled with political blizzards and out-dated policies. But current efforts are backing the economy to be one that is globally marketfriendly, says Angelica Buan in this report based on interviews with exhibitors at the recently concluded Indoplas show in Jakarta, Indonesia.
Shedding the economic strategies that were binary to old politics, the more recently reformed government has been more appreciative of the role of the country’s broad consumer base that is buoying up its industries. The industrial sectors, especially manufacturing and mining, contribute largely to the country’s annual GDP growth, which currently is estimated by the Asian Development Bank at 5.7%, to top 6% by 2015.
Under manufacturing, Indonesia’s automotive and packaging segments are strong growth performers.
At the recent Indoplas show, with Indoprint and Indopack events held simultaneously from 3-6 September in Jakarta, it was clear that the two segments were the target markets for many of the 400 exhibitors from 20 countries.
A real-time barometer that the country’s local market is in competitive form in terms of production quality, capacities, and output, the triad events hosted international pavilions, including countries like Germany, Austria, Taiwan and Singapore.
According to Singapore-headquartered Messe Düsseldorf Asia (MDA), co-organiser of the event, international firms outnumbered local exhibitors. A 20% increase in the number of first-time exhibitors was also noted this year, with some 25,000 visitors to the four-day event.
Vital market for Germany and Europe
According to MDA and its co-organiser, Jakarta-based PT Wahana Kemalaniaga Makmur (Wakeni), there were more German exhibitors this year than the previous show held in 2012. The increase is an indicator that Indonesia has become an important market for the German plastics (and rubber) machinery makers.
Claudia Frey, Deputy Managing Director of the German Engineering Federation or VDMA, said that Germany’s highest export volume to Indonesia, exceeding EUR95 million, was in 2012. This was an increase of 65% against the previous year, she told PRA.
But Indonesian imports of plastics and rubber machines last year decreased by around 20%. All major suppliers from abroad were hit, according to Frey. However, it is looking better this year. “Based on the latest data published only a few days before the Indoplas event, there was a 59% increase in shipments from Germany to Indonesia for the second quarter of 2014,” added Frey.
She went on to say that Germany ranks third among the most important suppliers of plastics and rubber machinery to processors in Indonesia, with a considerable share in overall imports.
Indonesia’s increased demand, brought on by rising quality requirements of its growing population, makes the country a favourable market, as well as a supply source of plastics (and rubber) products.
Jurgen Rehkopf, Managing Director of Reifenhäuser Singapore, a part of the Germany-based Reifenhäuser Group, said that packaging applications have a substantial market not only in Indonesia but in Asia, too. “The Asian market follows urbanisation and growth in population, which are also suitable factors for increased demand for food packaging.”
Frey added, “This is why more German manufacturers – not only from the field of plastics and rubber but also from the printing and packaging industries – work on establishing new contacts with partners in Indonesia and on nurturing existing partnerships.”
Exhibitors on a quest for more sales
Meanwhile, a number of European exhibitors from Italy, Switzerland, Turkey and the UK, as well as representatives from Asian countries like China, Thailand, Japan and India were on a mission to identify the potentials of the domestic market.
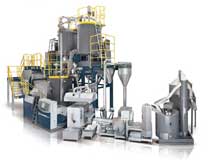
Austrian plastics recycling machine producer Erema, a first-time exhibitor, introduced to Indonesia its Intarema, which is 100% Austrian-made and boasts the “globally patented Counter Current technology”. According to spokesperson Tony Djunardy, the machine that was launched at K2013, “gives more output, is energy efficient and easy to operate.” Its other offering, the Vacurema for bottle-to-bottle food-grade recycling system, already has several installations in Indonesia, indicating that Erema is not a new player in the market.
Another first-time exhibitor, Italian Gamma Meccanica, also introduced its recycling systems. It was promoting the Eco Clean system, which removes printing ink from the surface of flexible films, which is not common to a number of other recycling systems. “Our machine has the capability to recycle even printed plastics,” said Erwin Forstner, Sales Manager, who also affirmed that the technology is European.
German extrusion blow moulding machine manufacturer Kautex, another first-time exhibitor, serves a variety of sectors from automotive to industrial and packaging. Erol Evcimen, Sales Manager, said that in Indonesia there are around 15 Kautex machines installed for producing consumer packaging, automotive, industrial and speciality products.
Extrusion machinery maker Reifenhäuser Singapore showcased the Evolution Ultra Cool (from the Evolution series), an operator-friendly and high-output cooling system with the broadest range of blow-up ratios. It is also able to increase the output of FFS lines by up to 30%, depending on the film structure.
ExxonMobil Chemical’s Vistamaxx and Santoprene polymer solutions are already being used for CPP packaging films in Indonesia. Philip Chew Chia Way, Managing Director of Singapore-based GME Chemicals, distributor for ExxonMobil Chemical, said that the domestic market is bristling with political stability and brisk consumption.
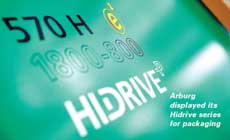
Germany-headquartered injection moulding machine maker Arburg presented its Allrounder 570H packaging series at the show. The machine belongs to the high-performance hybrid Hidrive series and features a clamping force of 180 tonnes with injection units of 400, 800, 1300 and 2100.
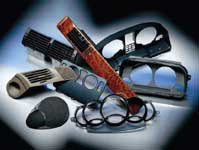
For Herrmann Ultraschalltechnik, its ultrasonic welding technology is able to serve three important segments: namely, automotive, packaging, and medical. Kai Broek, Regional Sales Representative, said that the automotive segment is stronger in Thailand than in Indonesia. “Packaging is Indonesia’s turf, while the medical segment is strong in Malaysia and Singapore.”
Likewise, tapping the automotive market segment is Geiss, a first-time exhibitor that manufactures thermoforming machines.
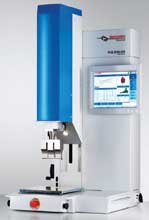
Spokesperson Manfred Geiss said that the 100% Germanmade machines were introduced as turnkey solutions for the local market.
“Automotive is not a core business in Indonesia, but growth in this sector is promising,” he said, adding that the machines reduce energy consumption by up to 40%, compared to other similar systems. “There are as many as 104 options for customers, allowing significant degree of customisation and automation,” Geiss added.
Moretto, an Italian ancillary equipment maker, introduced its latest energy saving dehumidifier and dosing equipment to the local market. Paolo Gasparotto, Business Development Manager, said that the application range for these machines include automotive, packaging, medical, film/profile, and electrical components.
But not all sectors are doing well as observed by some exhibitors in the woven bag sector. Austria-based BSW Machinery (a subsidiary of Windmöller & Hölscher), showcased machines for flat bottom bags as well as for producing water and tear-resistant AD proTex bags used as packaging for free-flowing dry materials. Rene Winkler, Area Sales Manager, said that the woven bags segment is highly competitive in Indonesia due to an overcapacity.
Another woven bag machinery supplier Starlinger, which has an office-cum-service centre that was opened in 2012 in Surabaya, also observed that the woven bags market is becoming tight due to oversupply of bags. “Many of our customers cater to the food, industrial, and construction sectors,” according to Regional Sales Manager Franz Steiner. Aside from Indonesia, the company is also strong in Vietnam, Philippines, Thailand, India, and Pakistan. The firm displayed the RX6 series, which it launched at the Chinaplas held in Shanghai in May this year.
Cost-efficiency overlooked
Since quality and efficiency follow innovation, the latter’s cost becomes a deterrent to buyers of machinery. Some of the exhibiting firms admitted that while many local customers expressed enthusiasm over the technologies demonstrating energy and space savings, not to mention ease of use, many prospective buyers still consider the cost of the machine more than the efficiency.
A few firms interviewed said that most start-up processors would prefer to purchase lower cost machines (such as ones made in China), but would shift to medium and higher-end machines when their businesses take off. Most German, Italian and Austrian machines, for example, are highend machines, and may not be practical for small production runs.
Comparable to markets such as Thailand, Singapore, and China, where receptiveness to more advanced technologies translates to lucrative demand, Indonesia is still not in the league. Some exhibitors suggested that a company has to run higher efficiency machines in order to maximise benefits.
Furthermore, energy efficiency is still not yet a consideration in Indonesia. VDMA, for example, is promoting energy-efficiency via the Blue Competence concept, which encompasses technologies and processes (mechanical and plant engineering) that ensure minimum consumption of energy, sustainability (with reduced emissions and use of resources); while delivering maximum productivity.
VDMA’s Claudia Frey sums it up: “Efficiency means saving resources and, hence, costs.”
High potential but long road ahead
Growth opportunities in the Indonesian plastics industry are not easy to grasp, according to exhibitors interviewed, hinting that setting up offices/plants in the country is not an agenda for the time being.
What is holding back the country from surging ahead? Plant/office set-ups in nearby locations usually suffice to serve neighbouring markets. Besides distributors, ExxonMobil Chemical has a plant in Singapore, and plans to set up an office and distribution centre in Thailand, according to GME Chemical’s Philip Chew.
Kautex has a facility in China. “There are no plans for the company to set up a facility in Indonesia, considering its proximity to the existing facility in Shunde (Guangdong Province),” Evcimen of Kautex explained.
Winkler of BSW also said that the company has no plans of expanding to Asia in order to “stay committed to quality.”
Forstner of Gamma Meccanica opined that consumer spending is comparatively low, despite the size of the population in Indonesia.
Skills gap
There is also the concern of the lack of skilled workers in the plastics processing industry. One company that is doing its part is Arburg. It runs training courses spanning 5-12 months for its workers to hone their technical and marketing skills. Included in the training is being “confident” in speaking the English language.
David Chan, Managing Director of Arburg for the ASEAN region, said that this is a valuable part of the module as this encourages staff to be able to provide information to clients with clarity.
Winkler of BSW Machinery, although not specifying Indonesia, also expressed frustration that availability of skills is a challenge in Asia, in addition to the cost of raw materials.
A new business, the German Training Centre for Injection Moulding Asia, is addressing the skills gap, specifically in the injection moulding industry, by introducing a training system offering ‘Injection Moulding Drivers Licence’ courses. The programme was launched in 2011 by the company in Europe and expanded to Asia this year. According to Rayston Tan, co-owner of the training centre, the module is divided into five stages and covers topics ranging from material and moulds to automation and process knowledge.
“It is important that a worker (operating a machine) is equipped with scientific, expert knowledge,” said Tan, adding that eliminating the “trial and error” practices of most operators who only acquire skills by experience could spare a company from costly delays.
Meanwhile, the country could also learn from various applications that the local industry can tap on based on market demand elsewhere in Asia.
Forstner of Gamma Meccanica said that “demand for insulation materials is good”, although he is not certain of the demand in the domestic market.
“The Asian market is fast growing, nonetheless, very competitive,” said Starlinger’s Steiner, who also suggested stepping ahead of the competition.
With progressive rational reforms still underway in the country, the overall prospect for Indonesia is one that is optimistic. It is just a matter of time that a road once less travelled for big global players will soon metamorphose into a major growth thoroughfare.
(PRA)