German show for machinery
Also, download this story from the electronic issue here
European machinery specialists will showcase a range of machinery at the upcoming Fakuma show to be held in Friedrichshafen, Germany, from 14-18 October.
Pelletising
- An underwater pelletiser that removes dirt and fine particles from process
water is said to drastically reduce power usage in water filtration and cut overall
pelletiser energy use by 10-17%, according to Nordson BKG. The Optigon water
filtration system eliminates the need for a separate fines-removal sieve, which
in standard systems requires a secondary, dedicated water pump. Instead, all
filtration is provided by a Polygon drum filter, where the 70-micron screens are
finer than the 150-micron screens used in standard systems. Driven by a small
motor, the drum rotates within the water that is circulated in the pelletising
system by the main process water pump. By eliminating the secondary pump,
the Optigon water filtration system uses 1,440 KW/year (measured at 8,000
hours), as against 44,000 kW and 98,480 kW for the company’s Opti-Line and
Poly-Line systems, respectively. Other energy-saving measures available
as optional include the insulation of the water system to prevent heat loss;
and insulation of the die plate heating flanges, with energy savings of 30%
compared with standard die plates.
- PSG‘s Maag Pump Systems, Automatik Pelletizing Systems and Maag Filtration
Systems will be presenting a complete system for polymer production in the
mid-tier output range. The system consists of the extrex 90 extrusion pump,
the CSC-RS 116 arched screen changer and the new Sphero S underwater
pelletiser system. The latter caters to compounding, masterbatch and recycling
applications in outputs from 700-3,000 kg/hour, with manual pressure setting
and pneumatic pressure control. The system requires no rails and can be
positioned with a swivel arm. An improved water bypass construction ensures
faster production start-up. Further exhibits are the Primo 200E dry-cut strand
pelletiser with its cantilever bearings and an extra-large cutting width of 200
mm for compounding of thermoplastics and the production of masterbatches up
to 1.5 tonnes/hour. Also on display is the extrex GDP twin outlet gear pump for
individual supply of melt to two different nozzle blocks.
- ProTec Polymer Processing will present the Solido LFT system for producing long fibre-reinforced thermoplastics (LFT) with fibre lengths corresponding to pellet lengths. The industry standard of 7-25 mm is produced via the pultrusion process. With Solido, the glass or carbon fibre strands are first isolated in the impregnation tool to create the filaments, followed by impregnation. The LFT pellets are said to produce components with improved surface quality and high mechanical strength, with a fibre content of up to 60% by weight and plant sizes of up to 1.2 tonnes/hour. LFT pellets can be injection moulded and used for applications previously reserved for thermosetting plastics. Automotive engineering in particular is currently a field of application for LFT but in the future even bioplastics can be "upgraded" in this way, says the firm.
Extrusion/Thermoforming
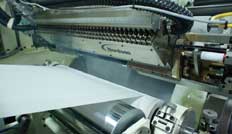
- Research by US-based Nordson Extrusion Dies
Industries has led to the development of a technology
that resolves the issue raised by low melt strength
polymers. The trials were carried out at Sung An
Machinery (SAM) North America’s technology centre.
SAM manufactures machinery and accessories for the printing and converting industry for paper, film, and
foil in South Korea. Components of the technology
include dies with lip lands that are shorter than the
industry standard, allowing the gauge profile of the
coating to be controlled. A suite of secondary internal
deckle blades, sized for various polymers allow for
fine-tuning of the edge profile of the polymer as it
exits, minimising bead formation. A short radius
is effective for LDPE while longer radii stabilises
the thickness profile near the edges with polymers
having less melt strength. Meanwhile, the “microrod”
designed by the company is half the standard
diameter allowing for less lateral movement of the
melt, thus less edge bead formation. The short lip land
and micro-rod are available in new dies specified by
converters while the suite of exchangeable secondary
deckle blades is available on a custom-designed basis.
- Italian producer of automatic coilers for small/large
flexible pipes FB Balzanelli is able to produce palletisation
systems to optimise the packaging and storage process of
various types of pipes. In addition to its TR series coilers
with two opposing reels – the first system developed by
FB Balzanelli – today the company's palletisation systems
are built to allow clients to manage multiple production
lines simultaneously. It has supplied 850 units worldwide
to date.
- Ettlinger Kunststoffmaschinen will launch the ERF500
melt filtration, designed for a maximum output of
5,000 kg/hour. This is an addition to the ERF200 and
ERF250 sizes
that achieve
outputs of 1.5
tonnes/hour and
2.5 tonnes/hour
respectively. The
compact ERF500
is able to handle
contamination
of up to 18%
by weight.
Another new
launch is the
ECO melt filter,
developed for
film and sheet
extrusion applications, to remove cross-linked and
high-molecular material fractions contained in the
melt, together with any gels or partial impurities. This
melt filter, rated for a contaminant level of 1.5% by
weight, is offered in two different sizes: ECO200 for
outputs of up to 1,000 kg/hour and ECO250 for 2,500
kg/hour. In addition to polyolefin, it is also suitable
for filtering easy-flowing materials such as PET or PA. The central component of both filters is a rotating,
cylindrical filter screen with millions of conical holes
that can be supplied with a wide variety of filtration
levels. The cleaned melt on the inside of the drum is
supplied to the downstream mould via a system of
flow channels. The rotary motion of the filter drum
simultaneously supports the blending and ensures
optimally homogeneous conditions in the melt.
- Illig will showcase its entry-level UA 100Ed sheet
processing machine, designed with a forming
area of 960 mm x 560 mm and manual loading. A
technology developed by the German company
is the central supply of cooling air employed for
cooling of formed parts. Apart from that, it will have
on display the UA 100g, with a forming area of 960
mm x 660 mm. Two options are available to expand
the basic machine: an additional upper table and
the “loose” part control required for demoulding
of parts with more pronounced undercuts. Other
highlights are the vacuum pump, reinforced cooling
fans with four adjustable air exhaust elements, as
well as ceramic infrared heater elements employed
to heat up the material to forming temperature, with
elements equipped with a special black glaze, thus
reducing energy by up to 30%. The PLC control is
equipped with a high-resolution TFT screen and the
new task-oriented user interface.
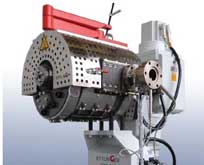
Auxiliary
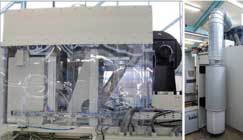
- Coperion K-Tron will present its patented BSP-135
Bulk Solids Pump (BSP) feeder on a pivoting base,
with positive displacement action and vertical
rotating discs that create feeding ducts. It will also
showcase its gravimetric batch blenders that are
available in sizes from 0.5-25 kg and include up to
eight main feed elements depending on the unit.
Each unit is designed with an integrated loading
platform for mounting material loaders or vacuum
receivers. The blenders include a metering and
weighing system for controlling all ingredients of every batch to the desired amounts and it is
not averaged over multiple batches. Besides the
vacuum receivers, the gravimetric batch blender
is equipped with a powder feeder. The latter is
designed to optimally handle difficult materials such
as pigments, sticky, bridging or flooding powders,
fibres and fiberglass. The volumetric feeders are
available in different sizes from 0.01 cu dm/hour to
1,600 cu dm/hour.
- Italy headquartered ancillary equipment producer
Moretto will showcase its Eureka system including
a Flowmatik airflow management and distribution
system, the OTX hopper drier and the X Max dryer.
Moretto’s Eureka system has been developed
over a 13-year period of testing, leading to what
company Founder/CEO Renato Moretto describes
as “the most ambitious project in the history of
dehumidification during my 45 years carrier in
the plastics world”. Moretto says the work Eureka
appropriately describes how the three elements
of the system have finally “closed the loop” to
form an efficient drying system. It is also said
to be the only drying system that can process
10,000-12,000 kg/hour of material in compounding,
extrusion and PET processing, boasting up to 56%
lower energy consumption than traditional drying
systems. The end product has been redesigned
and calculated utilising the power and AI of the
high-end Leonardo computer (one of only three in
Europe), says Moretto. X MAX dryer is based on
Moretto’s patented X technology and incorporates a
multi bed single molecular sieve desiccant system
providing constant -65°C to -85°C dew point. A key
enhancement is its multi-stage centrifugal blower,
developed by Moretto since the initial launch in co
operation with Padua University. The X Max 916
model, for example, is said to provide up to 1,600
cu m/hour drying capacity at 300 mbar pressure
with low electricity consumption of 13.2 kWh.
The truncated cone-shaped OTX (Original Thermal
Exchanger) hopper dryer is available in 28 sizes and
is said to be 40% faster.
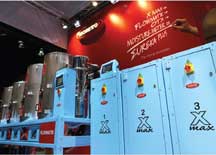