Updated version: Japanese machine makers pull out all the stops - See more at: http://www.injectionmouldingasia.com/nov2014/leadfeature1.html

The Japanese International Plastics Fair (IPF) show, held in Tokyo’s Makuhari Messe, from 28th October to 1st November, had 776 exhibitors (470 from Japan and 306 from overseas) exhibiting over a gross space of 54,000 sq m.
The organiser, IPF Association, of the triennially-held show expects a better turnout of visitors this year (with a target of 45,000 visitors), compared to the 2011 show (43,745 visitors). The lower visitorship in 2011 was attributed to the earthquake in Japan.
Three years on, the industry sector is in an upbeat mood, resulting in a promising turnout of 6,107 visitors (of which 1,145 were foreigners) on the first day (28th October), against 5,882 visitors (of which 770 were foreigners) on the first day of the show in 2011.
Below are some highlights from the 2014 event:
- Fanuc is making its entry into the automotive sector, having focused on selling its machinery to the connector and precision moulding sectors. It has introduced what it says are “cheaper, in between sized models” as well as a two-component model (130 and 220 tonnes clamping force) targeting automotive parts makers. It also displayed a machine for liquid silicone rubber (LSR), its first. Another highlight was robotic system integration, with a robot inserting metal parts in micro connectors, inside the machine.
- JSW displayed a machine incorporating die slide technology that allows hollow parts to be welded in the machine, which means no other ancillary equipment like a welder is required. It is targeted at the automotive market, for making parts like windshield washer tanks.
- A veteran in LSR moulding (of over 30 years), Nissei Plastic Industrial showed its NEX180III-5ELMN model with the newly developed SPPS (spiral plunger system) for small volume, high pressure moulding. It uses an inline screw (first-in, first-out concept) and combines it with a newly designed plunger metering injection unit. The 180-tonne machine was moulding a magnifier, processing two types of LSRs with different hardness and a PA66. Another highlight is the NEX110III-12EG electric machine updated with a “gas generation control moulding system” (a trend replicated by other machine makers). Basically, it features a special screw and smart feeder to prevent moulding defects (burns and short shots), arising from gas generated when processing plastics like PC, for instance.
- Of the five injection moulding machines at Toshiba Machine’s booth a special mention goes to the 550-tonne LFormer (550-26BP) vertical machine undertaking glass fibre/carbon fibre in-line moulding technology. Targeted at the automotive sector, for lightweighting and metal substitution, it was shown moulding a PA6 transmission casing with intermeshing carbon fibre (15%) and glass fibre (15%) reinforcements. Calling it hybrid moulding (a phrase used by other machine makers moulding carbon fibre-reinforced plastics or CFRPs at the show), it utilises Lanxess’s subsdiary Bond Laminates’s Tepex sheet material, which is heated by a Heraeus near infrared heater and then pressed by a Satoh Machinery Works press. The sheet is transferred to a mould (Suruga Engineering) where the PA6 material is injected. The direct injection technology, an alternative to heat press and stamp moulding processes, boasts 50% reduction of material costs.
- Toyo Machinery & Metal is also entering the LSR sector (Si-100-675D machine) and CFRP hybrid moulding (ET-80HR2 D75 machine). Another new entrant is the SAG + alpha technology shown on the Si-180 model. The “gas suppression system” includes a newly coated screw (SAG) reinforced with a vacuum system (alpha) to curtail the build-up of gases during plasticising. This is especially useful for resins that require pre-drying, like PET for instance.
- Ube Industries presented its Cav-Change Innovation, which is a multi-shot technology it first showed at IPF 2011. The updated version of the process was shown in a component featuring a stitch design. The coloured stitch moulding, which is back moulded on a foamed elastomer part and is made of PP, replicates actual stitching. The concept is targeted at automotive interiors, but one wonders if these need to be stitched up!
- Sodick premiered its GL (Global Standards) series, demonstrating applications like 3D in-mould appliqué moulding, fine pitch connectors, insert moulding and medical parts. The GL-100 Vent machine features “outgas reduction” made possible with a nitrogen vacuum system. Also on display was a tiebarless 3-tonne all-electric machine (M4-3000) that was moulding a washer part in PA9t material, with a thickness of 0.093 g and weight of 0.057 cc. Though the machine maker has no plans to sell or market the machine, the washer part did make for an interesting display!
- In the auxiliary sector, Yushin displayed a new concept cartesian robot designed to handle complex tasks. Two arms are arranged in a V configuration working in tandem, each with a wrist unit boasting three NC servo-powered axes. The robots were shown arranging letters on a cube on its six sides, as well as picking up a large ball. Though not due for commercialisation just yet, the concept is close to human dexterity and beyond the capabilities of standard traverse robots.
- Another auxiliary equipment maker Matsui Manufacturing’s booth was one of the largest at the show and it needed the space to present its ten different trouble shooting solutions, in line with its push for the Factor 4 concept in facilities. The displays were in collaboration with partners to eliminate resource wastage, increase added value and productivity. Partners included Husky Injection Molding, Frigel Process Cooling, Tria, Moldex3D, Trexel, Showa Denko and OPM Laboratory.
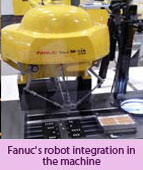
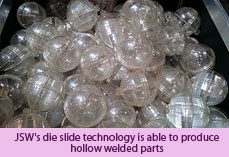
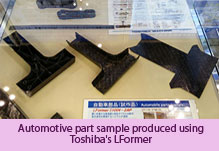
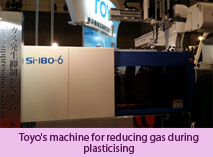
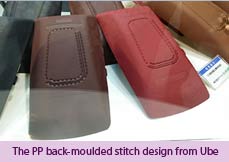
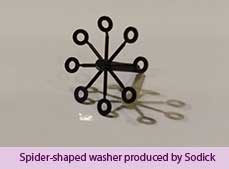
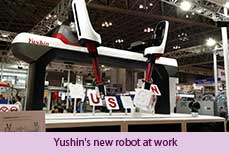
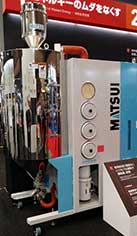