Also, download this story from the electronic issue here
Development work on carbon fibre-reinforced thermoplastics (CFRTPs) for the automotive sector is pacing up. Whilst Teijin is working on CFRTPs for high-volume production, Sabic and its partners have developed an advanced additive manufacturing technology to help address the manufacturing challenges processors are facing – the high cost of innovation.
Carbon fibre has ten times the strength but just a fourth of the weight of steel. Composite materials made of carbon fibres and resins are already widely used to reduce the weight of aircraft and other industrial materials. However, conventional thermoset-formed carbon fibre composites are rarely seen in mass production due to the slow takt time.
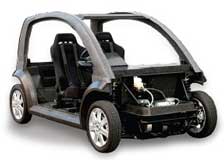
CFRTP for mass production
Nevertheless, in 2011, Japanese supplier Teijin Group built a four-seater concept car with its carbon fibre-reinforced thermoplastic (CFRTP) body structure. The body was formed in one minute and weighs 47 kg, which is a fifth of a comparable steel structure, achievements that represent a new world of mass production applications for carbon fibre composites.
Teijin tackled the problem of slow takt time by developing a thermoplastic resin that softens when heat is applied and quickly hardens when it cools, without losing its desirable properties, allowing it to be press-moulded in a much shorter time. Not only does that make the material ideal for mass production applications, it also means it can be recycled and reused.
Teijin has branded this world’s first CFRTP technology as Sereebo, an acronym for Save the Earth, Revolutionary & Evolutionary Carbon, and is now bringing it closer to commercial use in high-volume production.
The Japanese company says it is currently working with automotive makers worldwide, including General Motors, to accelerate development of Sereebo composites for mass production of reduced-weight vehicles that meet demand for energy savings and CO2 reductions.
The firm is spearheading the collaborative effort, which involves technical facilities in both Japan and the US and a pilot plant in Japan.
Collaborative developments with consumer electronics makers and precision equipment makers are also in progress, and Nikon has already adopted Sereebo to manufacture structural parts for a digital SLR camera.
Teijin says it is targeting sales of its solutions incorporating carbon fibre composites to reach US$1.5 to 2 billion by around 2020.
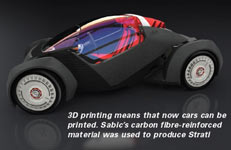
Driving off in a 3D printed vehicle
Elsewhere, a first-of-its-kind concept vehicle has been innovated using advanced 3D printing (also known as additive manufacturing) during the International Manufacturing Technology Show (IMTS) in the US recently.
This fully functional vehicle was printed from scratch and assembled by automotive design firm Local Motors that collaborated with Cincinnati Incorporated, a largescale manufacturing system builder; US Department of Energy’s Oak Ridge National Laboratory (ORNL), a pioneer in advanced materials research; and materials firm Sabic.
This ground breaking event showcases a long-awaited solution to a major manufacturing challenge: how to avoid the significant investments in tooling and time necessary to produce large free form designs.
Sabic’s LNP Stat-Kon carbon fibre-reinforced compound was chosen for its strength-to-weight ratio and high stiffness, which minimises warping during the 3D printing process.
The concept vehicle event stemmed from Local Motor’s Design Challenge, which resulted in the submission of over 200 entries from 30+ countries. The winning concept, Strati, inspired the full sized 3D-printed prototype.
Though Local Motors claims that Strati is the world's first 3D printed car, the Urbee developed in 2010 may lay claim to the title. Urbee is the result of a collaboration between engineering group, Kor Ecologic, which designed the vehicle, and additive manufacturing machine maker Stratasys, which printed all the vehicle’s exterior components. Stratasys used fused deposition modelling (FDM), which creates plastic parts by applying real thermoplastics in layers from the bottom up.
However, Local Motors contends that the Urbee used only 3D printed panels and features, whilst relying on a standard internal structure while it says that every part of the Strati that isn't mechanical is 3D printed.
The company also claims that it is the first time that the main portion of a car has been printed in one piece using direct digital manufacturing. Mechanical components, like the battery, motor, wiring and suspension, were sourced from a variety of suppliers and installed by Local Motors.
First, the body is printed using a Big Area Additive Manufacturing machine from Cincinnati and ORNL. Subtractive manufacturing is then carried out using a CNC routing machine and, finally, the printed portion of the vehicle is assembled with the additional components over two days. Thus, it took five days to build the car: 44 hours to print the car, one day to mill and two days to assemble.
ORNL worked on the large-scale additive machine using the chassis and drives of Cincinnati’s gantry-style laser cutting system as the base, as well as a high-speed cutting tool, pellet feed mechanism and control software for additional capability.
The completed and fully functional Strati was driven for the first time at the show.
(PRA)