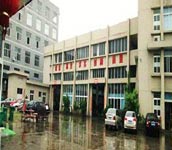
Italian rotomoulding machine maker Persico has expanded its operations in China by purchasing the mould making division of Chinese company EPL, which has a facility near Ningbo. Meanwhile, Persico has also set up a subsidiary in the US, by acquiring Detroit-based Autoplas Systems and will operate from the facility.
In China, the acquired division has been engaged in the design and manufacture of moulds for SMCs and injection moulding since 2006. In the future, Persico Asia will produce not only these products but also other types of moulding tools, including prefixing and edge-folding, currently manufactured by Persico in Italy.
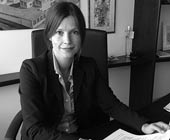
In the US, the firm will continue to manufacture the American company’s existing products – equipment and machinery for the automotive industry, said Alessandra Persico, Managing Director of Persico Automotive. “Additionally, we will start production of our own products – initially for the automotive sector, but subsequently for other industries, as needed by the customers of our other divisions (aerospace/aeronautics, rotomoulding and marine). We are working on more and more projects worldwide, requiring sites close to our customers,” she continued.
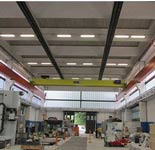
In Italy, Persico has purchased an area of 39,000 sq m near its present facility and to improve its manufacturing efficiency and vertical integration, has also bought two new milling machines.
At the K show, Persico will launch the new Smart machine, a development of its Leonardo system that was introduced ten years ago on the market. The latest Smart model is automated and operates on the same principal of direct heating via electricity and cooling using fans or Venturi devices as well as automation for the opening and closing of the mould, loading the resin and depositing finished parts on a conveyor.
The machines are similar to the traditional single-arm moulding machines, while the aluminium moulds, which are processed on a CNC machine, have a thickness of 5 to 10 mm and are provided with special grooves to accommodate the electrical resistances used to heat them. The moulds are fitted with temperature sensors, internal cooling devices and all the features required by the Leonardo system for process control. In addition, they can be equipped with automatic opening and closing devices and have 16 heating zones to reach a maximum power of 100 kW. The quick mould change prevents machine downtime during this operation. The Leonardo system for automatically controlling the moulding cycle is based on the temperature of the air inside the mould and the production cycle is monitored by a PLC in which all the parameters have been preset. Electrical heating makes a heating and cooling unit superfluous, reducing the overall weight of the mould, lowering energy consumption without imposing temperature limits to the process while increasing heating efficiency.
The company, based in Nembro, near Bergamo, describes it as an all-in-one compact machine with an attractive ROI due to benefits such as a shorter cycle, raw material savings and reduced energy consumption.
(PRA)