Biobased materials embrace improvements
Also, download this story from the electronic issue here
The still young and fast growing bioplastics market, with an estimated growth of 20% a year, is continuously being updated to cater to new innovations and further the sustainability issues.
Old hand PLA gets into the swing of things
Swedish firm Perstorp has introduced renewable Capa for Bioplastics, the world’s first of its kind concept which builds on the Capa lactide technology. The renewable concept enables freedom to design polymers that are flexible or hard, transparent or crystalline, tough or rigid and with a targeted melting point and polarity. Market indications show that these products are likely to deliver what many customers are looking for in terms of biobased content and performance. Renewable Capa has been evaluated both in terms of compostability and biobased content and is also certified as biobased by the independent Belgian certification body Vinçotte.
Perstorp says it will continue to focus its efforts on three fast-growing bioplastic segments – paper coatings, bags and films, and packaging. Capa for Bioplastics is a biopolymer enhancer that is said to offer stability and compatibility, improved mechanical properties, flexibility at low temperatures, and biodegradability. This effort is supported by Perstorp’s industrial production and pilot facilities in Warrington, UK and its Swedish innovation centre in Perstorp, for bioplastic formulations.
Currently, the lactic acid used to produce PLA has been based on first-generation feedstocks like cane sugar, sugar beet, corn and cassava, are grown following principles of sustainable agriculture, yet the debate still continues on whether these do not compete with food production.
Corbion Purac claims it is the first in the world to have successfully made PLA bioplastic resin from second generation feedstocks that are not suitable for human consumption, and include plant-based materials like bagasse, corn stover, wheat straw and wood chips.
In order to fully commercialise and bring PLA based on second generation feedstocks to the market in commercial quantities, Corbion invites all interested brandowners and converters to join a consortium in order to accelerate the market introduction of second generation feedstock bioplastics.
Biosuccinic acid developments
Following the commissioning and opening of BioAmber’s joint venture plant with Mitsui Chemicals in Sarnia, Canada, it has made the first shipments of its biobased succinic acid. The US$141.5 million plant has a capacity of 30,000 tonnes/year of succinic acid, making it the largest of its kind in the world. It is expected to increase production volumes progressively to reach full capacity in 2017.
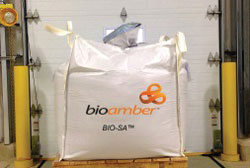
Succinic acid is produced via a fermentation process that makes use of a proprietary yeast, BioAmber licensed exclusively from Cargill. Although originally developed to produce lactic acid, the yeast was found to be able to ferment at a low pH and, contrary to other organisms that were experimented with, able to tolerate high concentrations of succinic acid. BioAmber and Cargill collaborated closely on the development of this yeast technology. BioAmber says the biosuccinic acid produced is of higher quality than previously produced at the demonstration plant located in France.
Minneapolis-based BioAmber has also entered into a technology license with Johnson Matthey Davy Technologies (JM Davy) that will enable the construction of a 100,000-tonne/year plant that uses biosuccinic acid as the feedstock to produce 70,000 tonnes of BDO and 30,000 tonnes of tetrahydrofuran (THF). It has also secured the rights to license the JMD technology for two additional BDO/THF plants.
By licensing JM Davy's proven BDO/THF technology, BioAmber says it accelerates the process, saving time and money for setting up the plant, which it plans to commission in 2018. BioAmber has already signed a 15 year take-or-pay agreement with Vinmar International for 100% of the output from the plant's 100,000 tonne-year BDO and THF capacity. BDO and THF are used to make engineering plastics, polyurethanes, biodegradable polyesters, spandex and other speciality chemicals.
Meanwhile, Covestro, formerly Bayer MaterialScience, and Reverdia are to jointly develop thermoplastic polyurethanes (TPUs) based on Reverdia’s Biosuccinium succinic. The Desmopan TPUs are targeted for use in a variety of applications, including the footwear and consumer electronics industries. Biosuccinium, produced at commercial scale since 2012 using Reverdia’s patented low-pH yeast technology, allows Covestro to capitalise on years of research.
The company plans to expand its biobased TPU production in Taiwan to industrial scale. Biobased Desmopan products are already available in various hardness grades, including 85 Shore A, 95A and 60D. Simulations by Reverdia suggest a roughly 65% reduction in the carbon impact compared with products produced with petrochemicals.
Modifiers to up the PVC/epoxy resins ante
US firm Metabolix has developed a new class of renewable multifunctional modifiers for PVC. This series of biobased PHA (polyhydroxyalkanoate) copolymers offer toughening, plasticisation, and improved processing. Other benefits are the good UV stability and transparency, do not promote biodegradation, and are fungi resistant.
Because of their unique miscibility with PVC, the PHA modifiers do not migrate, extract, or volatilise.
Metabolix’s current range of Mirel PHA copolymers are produced by bio-fermentation of sugars in which the water-insoluble inert polymer accumulates inside specially engineered microorganisms. The polymer is then extracted and purified and can be compounded and processed using conventional plastics converting equipment.
Metabolix says it is working closely with customers to commercialise its PHA biopolymers in PVC applications such as building materials, flooring, decking and railing systems, wire and cable, tubing, roofing and films, as well as in a variety of parts using recycled or reprocessed PVC.
Solvay’s Epicerol recently won the JEC Asia 2015 Innovation Award. Solvay is the owner of the Epicerol technology and trade mark, and Advanced Biochemical (Thailand), the producer of Epicerol, a 100% biobased epichlorohydrin (ECH).
A chemical intermediate, it is mainly used in the production of epoxy resins, a key material for a wide range of industries namely composites, coatings and electronics. It has been in use since 2012 and a recent partnership with customers saw Epicerol-based epoxy resins being used in the composite matrix of the Belgian Solar Car, The Punch One, allowing for 45% bio-content in the resin.
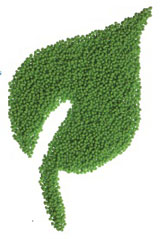
TPEs/engineering plastics enter the foray
Hexpol TPE group (which brings together the Elasto and Müller Kunststoffe businesses) has launched Dryflex Green, a family of TPE compounds based on renewable resources such as plant and vegetable crops. The range includes several series with amounts of renewable content to over 70% (ASTM D 6866 ) with hardnesses from 50 to 80 Shore A.
The TPE compounds display mechanical and physical properties comparable to TPE from fossil - based raw materials. They offer flexibility and tensile properties with a soft-touch feel. They can be processed using traditional polymer technologies such as injection moulding and extrusion. Dryflex green TPE compounds give adhesion to biobased polymers, such as PE, for 2K and multicomponent applications. The compounds are also fully recyclable and can be easily coloured.

Spain-based Elix Polymers has introduced a natural fibre-reinforced ABS for injection moulding applications and specific extrusion processes, targeted at the automotive and furniture markets. Benefits include high stiffness, heat resistance, low moulding shrinkage ratios, low emissions and weight reduction when compared to glass fibre-reinforced ABS, says Elix. It adds that the ABS-NF has a density of 1.12 compared to 1.15 for ABS-GF. The material has been also tested for 3D printing technology with impressive results, both in terms of processability and aesthetics.
The development of the material was undertaken under the auspices of the EEA and Norway Grants, representing the contribution of Iceland, Liechtenstein and Norway. This was the first time that a European ABS producer was given a European Grant for a project to investigate new sustainable ABS materials and composites.
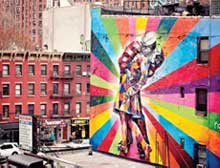
US-based PolyOne’s resound natural fibre-reinforced composites are now being targeted at the consumer sector, hence the firm has added on new colours and extrusion option offerings for non-automotive customers. New reSound NF colour options include beige, copper, terra cotta, green, blue and black hues, developed in collaboration with PolyOne’s InVisiOSM Color Inspirations 2016 colour collections.
In addition, reSound NF is now available in formulations that have been tested and proven for profile extrusion, expanding its use to potential extrusion applications in building and construction, sports and leisure, and furniture manufacturing.
Introduced this year in March, the materials offer mechanical property improvements of more than 20% for tensile and flexural properties, 10°C to 20°C higher heat deflection temperature, and an increase of more than 50% in impact strength. Independent testing has shown that reSound NF formulations offer equivalent performance to short glass fibre-reinforced alternatives, at a 5-10% lower density.
(PRA)Copyright (c) 2015 www.plasticsandrubberasia.com. All rights reserved.