Also, download this story from the electronic issue here
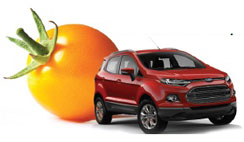
Left-over food? Fruit scraps? Discarded shells and seeds? Don’t throw them into the compost pit just yet. These food wastes can actually be used to make plastics.
The recycling of food waste and scraps has been limited to organic fertilisers, garden mulch or biogas when they had nowhere to go to but the landfills. In a study commissioned by the Food and Agriculture Organisation (FAO) of the United Nations (UN), it was cited that about 30%, or 1.3 billion tonnes, of food across all levels of the supply chain worldwide is wasted, amounting to an estimated US$1 trillion.
With the current technology advances in creating new materials, fruits, vegetables and other sources like prawn shells have been found to be ideal as organic materials for plastics. Although based from nutritional food sources, the resulting bioplastics are not edible. So the next time a meal is served, think about how food can provide environmentally friendly solutions to lessening the use of fuel-based plastics.
- Switzerland-headquartered Tetra Pak has recently launched the first of its kind carton packaging made of plant-based LDPE films and Forest Stewardship Council certified paperboard, as well as biobased HDPE caps, both derived from sugar cane. The Tetra Rex packaging is developed in partnership with Brazilian biopolymers producer Braskem; and will be commercially available in early 2015.
- Tomatoes are more than just ketchup for Michigan headquartered car maker Ford Motor and Philadelphia based food processing company Heinz. Ford’s team at the Plastics Research Division is exploring the potential of transforming Heinz’s tonnes of tomato by-product, called tomato pomace, into reinforced PP that is more eco- friendly and lighter compared to a talc-reinforced material . Ford has used soybean oil and wheat straw to produce cushioned parts and plastic frames of cars, and its biobased portfolio also includes parts from hemp cellulose fibre, recycled cotton, coconut, kenaf, tree pulp fibre, and rice hull.
- Using a major fatty acid obtained from coconut oil, scientists from the University of the Philippines Natural Science Research Institute (UP-NSRI) and the UP Institute of Chemistry have developed a biodegradable plastic and clay.
- Researchers at the Aalto University in Helsinki, Finland, created a starch-based transparent bioplastic that is biodegradable and possesses high mechanical strength and thermal resistance. The process adopted by the team is different from the usual film processing of starch being treated with heat and water through gelatisation, which makes plastic material degrade faster and become brittle. This has been overcome by using a star-shaped molecule called AEEP (aminoethoxy ethanol substituted phosphazene), the lengths of which act as mobile hydrogen bonding plasticiser molecules while being connected to a central core. It, thus, effectively prevents migration and leeching of the starch molecules from the resulting plastic, said the researchers.
- Scientists from the Institute of Technology (IIT) in Genova, Italy, are proving that parsley is more than just an edible herb. The team sampled parsley as well as other food wastes including rice hulls, cocoa pod and spinach to turn them into plastics using the same process as creating cellophane. According to the IIT scientists, they observed how cellophane is processed, which includes passing cellulose, the matter that makes up plant cell walls, through acid and alkali baths. And when cellulose derived from cotton and hemp is dissolved in trifluoroacetic acid, a common chemical, it can turn into a material that is mouldable into plastic, without doing any additional processing. As an additional benefit, the team said that the resulting bioplastic exhibits the inherent properties of the herbs and vegetables used. In the case of parsley, it is its antioxidant properties.
- Cashew-derived plastics were developed by Japan headquartered NEC Corporation in 2010. The biomassbased plastic is produced by bonding non-edible cellulose with oil-like cardanol, extracted from cashew nut shells. The resulting bioplastic, featuring a high plant composition ratio of more than 70%, is durable, heat and water resistant, non-crystalline and can be easily moulded. It is also said to be twice as strong as polylactic acid resin (PLA). This year, NEC developed a new production technology, known as the two-stage heterogeneous synthesis process, that can synthesise the bioplastics, while consuming just one-tenth the energy that was previously required. NEC says that it will be using this technology to start mass production of cellulose-based bioplastics by 2016. It is targeting its material at the electronics sector.
- For the past two years, researchers at Harvard University's Institute for Biologically Inspired Engineering have been developing a fully degradable bioplastic known as shrilk, which is a combination of silk protein and a substance called chitosan that is found in crustacean shells and insect parts. The downside is that shrilk is a complex material that needs to be fabricated in specialised environments, and chitosan is not waterproof like petroleum-based plastics, so a coating of beeswax is required to create a water barrier. Also, some modifications will be required to use the current technologies of injection moulding and casting to mass manufacture shrilk-based products. Applications range from toys, mobile phones to packaging and diapers. The upside is that not only is shrilk fully degradable, but it also releases plant nutrients into the soil. It also poses no threat to trees, unlike wood cellulose.
- Two fibre-rich fruits have been utilised by a group of researchers from Brazil to create plastics that are ideal for automotive applications. Plastics that are reinforced by fibres, which can come from pineapples and bananas, are believed to be three to four times stronger, 30% lighter, and completely renewable, than conventional plastics. Some of these so-called nano-cellulose fibres are likened in stiffness to DuPont’s proprietary nylon material, Kevlar, used in armour and bulletproof vests. To prepare the nano-fibres, leaves and stems of pineapples or other plants are put into a device similar to a pressure cooker. After adding in chemicals, the mixture is heated over several cycles until a pulverised material is produced. It takes 0.4 kg of nano-cellulose to make 45 kg of the bioplastic, the scientists explained. The team from Sao Paulo State University said that nanocellulose reinforced plastics also show greater resistance to damage from heat, gasoline, water, and oxygen. In the near future, the plastic may also be used in medical applications, for hip joints and artificial ligaments.
- A story that is not new but deserves a mention is US-based Cornell University’s polymer processed from oil from orange peels using a catalyst to speed up the reaction. Limonene is a carbon-based compound produced in more than 300 plant species. In oranges it makes up about 95% of the oil in the peel. It is also responsible for the citrus smell in the oil. The Cornell team used a derivative of this oil called limonene oxide and carbon dioxide as the building blocks for the polymer. A catalyst is also used to allow the limonene oxide to react with the carbon dioxide and formulate the polymer called polylimonene carbonate, which has many characters similar to polystyrene.