No holds barred on technology
The K2013 show, held from 16-23 October in Düsseldorf, Germany, may have had slightly lower visitors but machinery makers were enthusiastic about the response to the latest technology on display.
Extrusion/Converting
- India-based converting machinery maker Lohia Corp showed off a new logo having changed its name from Lohia Starlinger, as a consequence of Austria based Starlinger having divested its shareholding in the company. Its product line-up included a new modified extrusion coating machine for coating of flat/ tubular fabric with PP/LDPE, with a working width of 1,600 mm and speed up to 150 m/minute. This machine is supported by the circular looms for weaving tubular or flat fabric from PP/HDPE tapes and a conversion machine for bags, with an output of up to 45 bags/minute. Another highlight is the Autoroto tape winder, for winding flat/fibrillated tapes of different widths with speeds of up to 600 m/minute. It has been upgraded to enable automatic transfer of tapes from a full package to an empty tube. Having already delivered 15,000 of these winders, the firm is now working on a new generation winder, featuring more “smarter” electronics. The firm said it received over 350 active enquiries from prospects from almost 75 countries.
- Indian extrusion machinery maker Rajoo Engineers claimed it was the only company running a nylon barrier resin line at the show, producing around 3 tonnes/day “with a consistent output every day of the show”. The firm said it was an opportune time to showcase the technology since the Indian line offers a competitive price vis-à-vis the “high prices of European machines, coupled with the appreciation of the Euro with respect to domestic currencies.” At the K2010, the Rajkot-based firm tied up with German blown film machine maker Hosokawa Alpine to market hybrid lines. This collaboration has paid off with the machine displayed sold to Nylopack of South Africa. Rajoo also entered into a collaboration with Germanybased Maschinenbau Heilsbronn to provide spare parts and services for Rajoo machines bought in Europe. Meanwhile, Rajoo said it had an increase in visitors by over 30%, compared to the previous show.
- At an in-house expo it had at its Lengerich facility, German extrusion machine maker Windmöller & Hölscher (W&H) showcased the Aquarex blown film line with water quench cooling, Filmex cast film line with the new Filmatic PS stretch winders and it also had on display at the show the Optimex three-layer blown film line, but the highlight was surely the five-layer blown film line Varex II. Using the proven Varex technology as a foundation, it has improved upon the concept to feature a new die and air ring and modularity. It can be tailored to a user's specific requirements and also allows for retrofitting with optional modules to accommodate future requirements. All the components are also integrated in a central control system for ease of operation and monitoring from an ergonomically designed and intuitive operating unit. Highlights include the Maxicone P die specially optimised for polyolefins, flow-optimised barrier screws, patented melt distribution system, Optifil P gauge profile control system, new bubble collapsing unit in the film haul-off, new Filmatic S II winder and the new Arctis air ring, which is an upgrade of the Opticool air ring presented in 2009. The Varex II is available with working widths of up to 3,600 mm and for up to 11-layer films. It is designed for outputs up to 1,500 kg/hour. Extruder sizes include 50, 60, 70, 90, 105, 120 and 135.30 D. Die diameters range from 120- 900 mm. At the K, it was shown running a five-layer, 2,200 mm, 40-micron collation shrink film based on ExxonMobil Chemical’s Exceed and Enable mPE resins.
- Germany-based Hosokawa Alpine showed a five-layer blown film line with its patented 400 mm-diameter X die head for 11-layer films and a special triple lip high output V-ring. The firm says the die head is capable of a high level of versatility and competitive advantage, with the highest savings realised by replacing laminated structures with co-extruded structures, adding that there are a wide range of applications for 11-layer films in the food packaging segment. Capable of an output of up to 1,000 kg/hour, the line was running a different structure each day of the show. The extruders were equipped with Smartboxes and driven by water-cooled asynchronous servo motors. The line is controlled via ExVis 2.0 with a One-Touch system. Other novelties were the space saving Double Winder ATW and patented TRIO (trim reduction and orientation) machine direction orientation (MDO) system.
- At an open house, Austrian firm Battenfeld-Cincinnati showed an extrusion line for producing PP sheet with thicknesses ranging from 200-2,500 microns that was equipped with a high-speed BC-75-40 DV T4 extruder and the new Multi-Touch roll stack. Since the market launch ten years ago, the firm says it has already installed more than 170 high-speed extruders worldwide, with the compact 75 mm-machines able to reach outputs of up to 1,500 kg/hour for PP and up to 2,000 kg/hour for PS. A highlight was the Multi-Touch roll stack incorporated in the line, which operates with only two large chill rolls instead of the conventional stack of three rolls, but with the addition of five post-cooling rolls. This allows for even cooling and calibration of the sheet on both sides.
- Though German firm Reifenhäuser’s booth only had four virtual models on display, reserving the eight actual lines for an open house in its Troisdorf facility, it waxed lyrical about its Evolution extruder line that features an Energizer screw “to avoid useless energy input, reduce energy consumption and lower melt temperature by as much as 20°C without compromising melt quality or output.” Also debuting was the Mirex MT polishing-stack with a patented control mechanism for thermoforming sheet; Evolution Ultra Flat for flattening of blown film and Evolution Ultra Cool cooling ring.
- For the first time, Germany-based Brückner Group’s subsidiaries, including Brückner Maschinenbau, Brückner Servtec, Kiefel Technologies and PackSys Global, exhibited on a joint booth at the show. It also said the number of visitors “exceeded all expectations." Recent investments include the expansion of the Kiefel technology centre, production locations for PackSys Global and a new R&D centre for Brückner Maschinenbau, which offers a wide range of test facilities for components. Meanwhile, PackSys acquired Swiss company MADAG Printing Systems, a supplier of hotstamping machines, early this year, allowing for synergies in technology and customer potential.
- Manufacturer of corrugated pipe extrusion lines Unicor presented the UC 330 Corrugator with its newly developed air cooling system. It will be used primarily in the American drainage pipe market. During pipe production, the moulds can be kept at a constant temperature between 20°C and 80°C in a continuous cooling process. Outputs of up to 1,100 kg/hour (PP/PE) or 1,300 kg/hour (PVC) can be achieved and the maximum production speed is about 40 m/minute. Another new product, the SWESY 700 die head complements the "Disc Die Heads” already available from Unicor. It allows for wall thickness distribution in the diameter range from 95 mm id up to 700 mm od and also provides higher productivity, with quick changes between sizes. Meanwhile, since 2013, Canadian downstream equipment company Adescor has been a part of Unicor. It also presented its product portfolio at the K. Unicor has also been a part of the GAW Group of Graz, Austria, since 2012.
- German firms Leistritz Extrusionstechnik and materials handling firm AZO tied up to build an extrusion plant for the production of highly filled compounds with up to 85% calcium carbonate. Since the Leistritz ZSE MAXX extruders have a specific volume/torque ratio, this plant is able to realise maximum outputs and an energy efficient production. Leistritz and AZO were supported by GALA, Maag Pump Systems, Reverte Mineralprodukte, Ultrapolymers and BYK-Chemie. With slight adjustments, it can run various applications with, for example, talcum, titanium dioxide or barium sulphate. In the field of flame retardants, materials such as aluminium hydroxide or magnesium hydroxide can be processed. Due to the cost-efficient nature of the compounds, they have experienced a real boom lately, especially in the automotive and packaging industries or for white goods. The firms agree that production is very challenging for compounders, with the transport of the material from the big bag stations/silos to the extruder playing a crucial role. “This has to be done with minimum dust granting enough settling time and minimum air content, in the material.” Thus, Leistritz choose to work with AZO in the field of material handling.
- A particular focus in this process was the stable feeding of the dosing units, which is done by means of pneumatic suction conveyors. The collective feeding system is designed in an energy efficient way and thus, works with optimum conveying speed. If necessary, the polymer can be combined from various feeding points. Each component is sucked in according to its formula, accurately weighed and homogenously mixed by the AZO Mixomat. Colours and additives are also fed into the process directly above the extruder. Since the dosing unit is pivotable, material can be fed into the extruder from two positions.
- The firm also says that optimum distribution of the material streams is vital as well as material moisture that can complicate the process. Therefore, the processing unit and the screw geometry have to be designed according to the task. Thus, Leistritz used a ZSE 75 MAXX twin-screw extruder with a processing length of 48 L/D. Polymer, additives and calcium carbonate (provided by Ultrapolymers, Reverte and BYK) are fed into the process via the main feed opening and two side feeders. Leistritz implemented the downstream equipment with Maag (gear pump screen changer) and GALA (underwater pelletiser). Finally, the pellets are gently conveyed to the filling station by means of a suction conveyor.
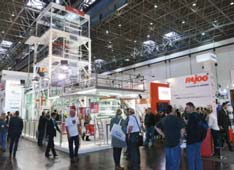
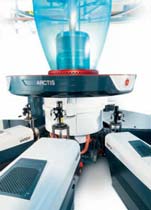
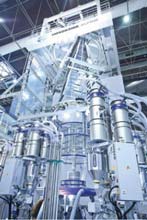
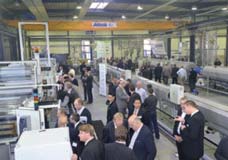
Recycling Equipment
- Austrian recycling machinery supplier Erema Engineering Recycling has launched the Intarema, which features the Counter Current feed technology allowing for a higher flow of material in a shorter time and because of its tangential configuration the process is said to be virtually pressure-free with preheated material. The flexibility extends to the system being able to process a range of difficult materials including those with high levels of moisture and contaminants, such as washed agricultural films, washed post consumer film flakes (PE-LD, PE-LLD, PE-HD), films with solid content such as paper, wood or metals and also thick-walled regrind materials from waste automotive and electronic goods, PS cups and PE lids. The system is paired with the "Smart Start" concept, allowing many central process steps to run automatically. Another innovation is the ecoSAVE technology (equipped as standard) that enables users to benefit from 10% less energy consumption. The firm says that including the direct drive of the extruder screw, up to 3% higher efficiency is possible. The system is available for capacities ranging from 50 to 3,000 kg/hour. It is offered in three series, with the T series featuring a short single-screw extruder without degassing for materials like non-printed edge trim, cutting waste, rolls and loose leftover film and regrind materials.
- The TE series features double degassing for the processing of slightly printed production or industrial waste plus fibres and technical plastics. The TVEplus, meanwhile, is designed for the recycling of heavily printed films or very moist materials. This is made possible through ultrafine filtration, thorough melt homogenisation and degassing in a single step.
- Austrian recycling systems provider Next Generation Recyclingmaschinen (NGR) and Leistritz Extrusionstechnik are partnering to market new recycling compounding technology. The new lines, known as A:COMP, S:COMP, X:COMP and F:COMP, will expand NGR’s product portfolio for post-industrial and post-consumer markets and will enable its customers to process virtually any form of plastic waste, such as films, fibres and thick-walled components, using NGR’s filtration technology. The melt will then be refined using twin-screw extruders from Leistritz. Additives, fillers and reinforcing materials are added to shape the property profile of the material. The results are custom-tailored materials for virtually any requested application area. The lines can also produce cost-optimised pellets. Rounding up is a user-friendly central control system that makes it easy to change equipment parameters, and a recipe management system that improves traceability. NGR's global sales network in the US, Malaysia and Taiwan will manage the marketing activities for the new lines.
- Meanwhile, NGR will also set up a Chinese customer centre beginning of 2014.The new facility in Taicang, Shanghai, will include two NGR systems for customer trialling. With a 25% share of the world's recycled plastics, the Chinese market is termed as an ideal location for further expansion, the company says. It also opened a US customer care centre in 2010.
- Due to global interest and after a period of testing, NGR says it will be using liquid state polycondensation (LSP) as a new process for PET recycling, to improve and control the properties of rPET. The process uses a higher rate of reaction in the melt phase to save energy and time. And while current methods of PET processing involve either slightly lowering the intrinsic viscosity (iV) values or using solid state condensation (SSP method) to increase the iV, LSP enables a short-term increase of iV values and thus leads to a higher decontamination performance. The firm has already started a pilot plant with capacity of up to 400 kg/hour of PET fibres and PET bottle flakes. It expects field testing to begin next year, with commercialisation in 2015. LSP supports the processing of PET from industrial waste, including fibres, bottles, preforms and films, as well as washed PET postconsumers flakes. NGR also expects it to be used for food grade applications once it has completed the regulatory approvals.
- Austrian firm Starlinger, which says it concluded sales worth EUR30 million during the exhibition, was promoting the new recoSTAR universal C-VAC recycling line, suitable for materials that tend to create gases in the recycling process such as postconsumer household waste and agricultural film or highly printed film. The module was sold on-site to a Portuguese plastics recycling company. In addition to the sale of the exhibited deCON decontamination dryer for rPET material, Starlinger Viscotec also won an order for the new viscoSHEET PET sheet line that produces sheet out of up to 100% rPET with what it says are guaranteed iV levels.
- The C-VAC degassing module is said to enhance process engineering, especially filtration, degassing and compounding. By using two extruders, two degassing ports and additional reverse venting, degassing performance is achieved. Due to the two separate extruder drives, the extruder speeds can be adjusted independently from each other according to material requirements, resulting in lower shear and consequently better degassing efficiency. Meanwhile, recycling and compounding (eg., glass fibre) is possible in one step as the compounding takes place during the recycling process after the melt filter. An advantage for glass fibre compounding is by using single screw extrusion, the breaking of the glass fibre is reduced to a minimum during the compounding process, which helps to increase the strength of the parts produced.
- Sweden-based Rapid Granulator showcased its new Raptor Series, which complements its existing GranuMATIC series. With its parent company IPEG’s recent acquisition of shredder manufacturer Republic Machine, the series incorporates Republic's PowerWedge rotor. It is said to be particularly suitable for the shredding of films, monofilaments and airbag materials. The equipment also features an "open hearted design", which allows the whole shredder to be opened up in what the firm says is less than 70 seconds using an integrated hydraulic system, allowing direct access to the core components for simpler maintenance. The firm will initially offer five modular models early next year.
- Pallmann introduced the HydroFiner for separating adhesive labels from large amounts of post-consumer laminated plastic packaging by using the hydromechanical action. In developing countries, the labels are often removed by vigorously brushing them off manually. Pallmann has taken this approach and improved it with its HydroFiner, where the waste is intensively rubbed between two surfaces, together with a small amount of water. “The material rubs mostly against itself, rather than the metal surfaces of the machine, the labels and the glue are separated and removed, and the packaging is reduced to flakes,” it says. The process, for which Pallmann has applied for a patent, is based on two discs, a rotor and a stator, with material being fed to the centre via an augur, and then moving to the outside through pairs of intermeshing teeth. The HydroFiner is capable of outputs of up to 1,800 kg/hour of packaging waste. The German firm says it sold two machines at the K.
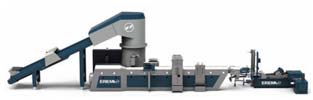
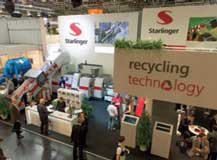
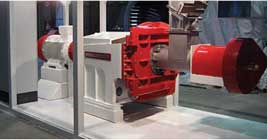
Auxiliary Equipment
- Italian auxiliary equipment maker Moretto presented what it says is the biggest standard gravimetric dosing unit in the world, specially developed for rPET bottle flakes dosing with output of up to 5,500 kg. The patented DGM Gravix gravimetric dosing series ensures precision, even in the presence of high vibrations, says the firm. An innovative feature is the weighing algorithm with the Vibration Immunity System (VIS). The reaction time is also said to be ten times faster than common dosing units in the market today. The double effect mixer ensures a homogeneous mixture and the digital technology allows for precision and speed in the weighing cycle. Double eyelid, free weighing hopper and Rotopulse with digital technology round up the Gravix. The Super Easy Touch View is a coloured interface with easy to use programming and intuitive for the machine and the process management. It caters to outputs from 30-12,000 kg/hour with dosages up to 12 materials and allows more than a 1,000 hopper combinations. This large hopper capability makes the Gravix versatile and available for different capabilities such as medical, powder, flakes, high temperatures, anti-wear and antistatic. The hoppers can be removed with no tools, allowing for easy inspection. The system software is based on the Linux platform.
- Emphasising that quality control for nonwovens and films has become crucial, ISRA Vision debuted a plug & inspect surface inspection solution, which it says simplifies integration with production lines by allowing customers to handle installation on their own and to start up the system quickly. The system uses a high speed camera and switchable LED lighting that allow detection and identification of defects from different views and angles within a single camera bank. The LED illumination has been patented by the German firm. It is operational on any PC or laptop, allowing for system integration on almost any machine, web run, and system. Due to its compact construction, it can also be used in existing environments where space is limited. With this system, ISRA says manufacturers of nonwovens and film have easy access to 100% surface inspection.
- With the feature of web-enabled controls, US firm Conair has made it possible for remote control of its auxiliary equipment from literally anywhere. This means wherever someone can access the internet, whether it is via a computer, laptop, tablet or smart phone, they can now connect remotely with the webenabled controls available on Conair’s dryers, blenders and material handling systems and monitor conditions, change settings, respond to alarms, troubleshoot or download process data. In fact, Conair says that interfacing with the controls is as if “you were standing in front of the equipment on the shop floor.” Another advantage of the Internet-based system is that Conair can have access to processors’ auxiliary equipment without having to access the corporate network. The web-connectivity features are standard on Carousel Plus dryers, DM3 drying monitor, TrueBlend gravimetric blenders, TrueWeigh gravimetric extrusion controls and gravimetric blenders and FLX and ELS central vacuum conveying systems.
- Swiss gear pump maker Maag Pump Systems unveiled its sixth generation gear pump boasting up to 50% higher performance. It has redesigned the gears, shafts, bearings and seals, to allow an improved volumetric efficiency. This makes it possible to operate at reduced rpm, shear rates and temperatures, reducing energy consumption by up to 10%. The advantage of the enhanced pump geometry will be welcomed by manufacturers of easily degradable products, in particular during degassing stages where minimum fill levels translate into reduced residence time. Processors will, thus, be able to minimise the levels of volatiles in their products. Furthermore, product quality is improved and due to the enhanced pressure capabilities, finer filter meshes can now be used further down the line. Maag also offers alternative housing designs for its polymer extraction pumps, with matching interfaces to older pump generations. The portfolio comprises multiple sizes with output of up to 100 tonnes/hour. Sizes 250 and above were launched at the K, while others will be introduced next year.
- US pelletiser maker Reduction Engineering Scheer is increasing its presence in Asia by having doubled the size of its Chinese facility in Shanghai and setting up a sales and service centre in Taiwan to support customers in Southeast Asia. In Taiwan, the 600 sq m facility will focus on re-sharpening of rotor knives using CNC grinding machines. Meanwhile, Scheer China doubled its production space in July to 1,000 sq m in response to strong growth. The facility has three CNC machines for re-sharpening of rotor knives. In Europe, the firm has expanded its manufacturing footprint by approximately 30%, relocating from its former operation in Stuttgart, Germany, to a new facility in Korntal. “The expansion was prompted by strong growth for pelletising systems throughout the world, particularly in Asia,” said the firm. The new facility houses a large-capacity laboratory that includes demonstration machines to run full production trials for customers.
- US testing equipment firm Instron has introduced the manual wedge grips that meet the stringent alignment requirements of NADCAP AC7122-1 (for non-metal materials) and AC7101 (for metals), commonly used in the aerospace industry. Whilst the 2716-028 wedge grips are designed for a nominal force of 100 kN, the 2716- 030 wedge grips can take maximum loads of 250 kN. This makes them an ideal choice for demanding tensile tests with a large variety of materials such as metals, high strength fibre reinforced polymers and other rigid materials. Their enclosed design resists dirt and debris. Symmetric closing of the grips is achieved via an easyto- use ratchet handle, whilst as the test proceeds, the wedge action allows the gripping force to increase in proportion to the applied load. Pull rods allow the grips to be used inside a compatible temperature chamber, providing a wide temperature range from –80°C to 250°C without changing parts or lubricants. Accessories include “piggy back” adaptors and fixtures for different test types that can be attached with the grips left on the system.
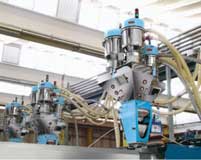
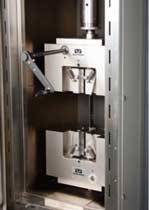