Thermoforming: Consumer appeal powers packaging
Also, download this story from the electronic issue here
What is in or out in packaging designs depends on consumer behaviour. Rising urbanisation and changing lifestyles are creating a platform of opportunities for packaging that promise convenience, sustainability and freshness, says Angelica Buan in this report.
Consumer trends are shaping the future of packaging industry. These trends not only boost food packaging demand but also household tendency and support the growth of the global plastic packaging market, which is expected to reach US$1.1 billion by 2022, according to Stratistics Market Research Consulting (SMRC).
Aiding this growth are technological innovations of packaging, increasing consumer awareness and favourable government policies, the US-headquartered research firm states, further adding that expansion of the food & beverage market, which is the largest application of plastic packaging, is expected to fuel market growth.
Food-on-the-run packaging
Lifestyles that are getting busier and rising urbanisation are catalysts for growing demand in packaged ready-toeat meals, small or single serves and food-on-the-go.
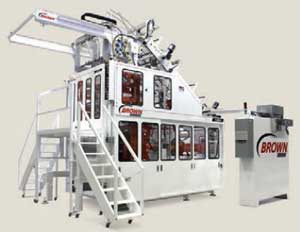
US-based thermoforming machine manufacturer Brown Machine is tapping on the opportunity for ready-to-eat meals with the latest offering in its Quad thermoforming series and its Elite line of trimmers. The improved equipment from the Quad series features increased thickness and height of the upper and lower forming heads, increased thickness of the platens and redesigned drive arms, resulting in 260 tonne-maximum station strength.
Italian firm Amut Comi has introduced the VPK C84 series: off-line or in-line configuration, with three and four stations. It is suitable for handling different materials, such as PET, PP, PS, PLA and PVC, and for producing trays, lids, berry boxes, clamshells, nursery trays and plates. The production speed is up to 35 cycles/ minute and the mould has an area of 840 x 650 mm. The four-column forming station has a clamping force of 24,000 kg (a top mould servo plugs assist is included) and can be extended until 60,000 kg for in-mould cutting. The series is equipped with a servodriven up-stacker (upon request) and an individual heating element control for top and bottom ovens with open zone configuration. The oven can be 1,950 mm or 3,250 mm in length. It is also equipped with a new software with a full diagnostic and easy learning/handling operator interface.
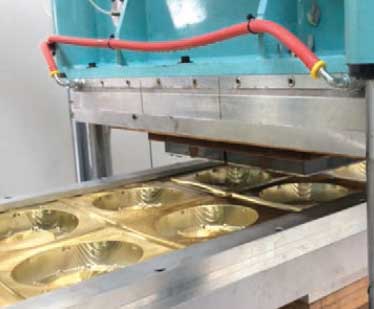
Meanwhile, revamping its packaging design into something that offers product visibility to cater to customers who want to see what the packaging contains, US-headquartered Campbell Soup Company packaged its microwaveable single serve soup in a translucent bowl thermoformed by Silgan Plastic Food Containers. The soup bowls also feature an over cap, clear PETGmodified label and flexible film-metal ring end, also from Silgan.

The ready-to-drink market is UK’s RPC Group’s target, with its introduction of the thermoformed cup for Indian cafe chain Café Coffee Day's Frappe Chill. The on-the-go cup, manufactured in multi-layer PP, with an EVOH layer that prevents oxygen ingress, keeps the quality of the coffee as it maximises ambient shelf life. The cup is retortable and the product is hot-filled and then retorted for 30 minutes at 118°C, RPC explained. The travel-friendly design offers convenience and ease of use for the consumer, including an integrated telescopic straw in the lid that can be expanded and contracted as required.
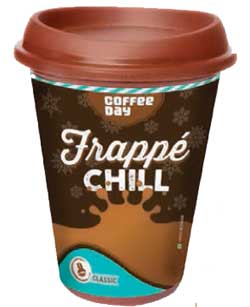
Fresh is in: call for barrier packaging
The need for balanced diets is revving up the demand for fresh products containing the least possible preservatives; and which call for packaging with excellent barrier properties.
Market research group Technavio forecasts that the global fresh food packaging market will grow moderately at a CAGR of around 4% by 2020. Augmented consumption of ready-to-eat food products will lead to the demand for packaging solutions that can extend the shelf life of the products enclosed. This has resulted in the advent of modified atmosphere packaging (MAP). Since this technology helps to maintain an optimum oxygen level, its augmented usage during the projected period will result in market growth, Technavio said.
The fresh food packaging market is segmented by type to include flexible and rigid plastic packaging, and paper and paperboard. The flexible plastic packaging segment is projected to account for more than 40% of the total market share by 2020. Since this packaging type is used to pack fresh food items, an increase in the demand for fresh food products will lead to its growth during the projected period, according to Technavio.
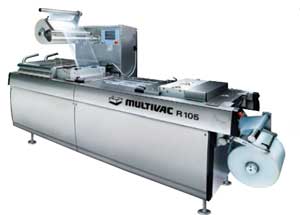
Offering packaging solutions suitable for fresh produce, US-headquartered Multivac has innovated the FreshSafe packaging concept based on the thermoformed vacuum packaging machine R105, which is a preconfigured, plug and play machine with several pre-programmed formats.
The concept packaging has perforations, created by the machine’s integrated perforator, enabling therefore an exchange of atmosphere and creating equilibrium (EMAP).
Meanwhile, UK fresh food packaging manufacturer Linpac and Italy-headquartered Infia, a fresh fruit and vegetable packaging manufacturer, developed the Freshware range, which taps into the growing demand for chilled prepared and convenience food. It comprises hinged and lid sealed containers and tubs for prepared fruits and salads.
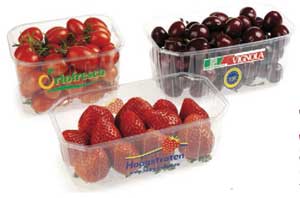
Infia also has new designs for fruit punnets, which include a side ventilation air flow system. It says it is the first packaging producer in the world to be able to apply a printing solution directly on to a punnet. This exclusive technology enables pack personalisation and promotion of customers' brands and logos. Unlike other technologies, such as heat transfer, labels or sleeves, it does not add additional plastic materials to trays resulting in improved cost savings and environmental impact.
RPC produces MAP trays, sealing film and tray lidding machines, enabling packing a range of seafood products from fish fillets to shellfish. The thermoformed HDPE trays come in a range of sizes and boast of features such as pyramids, which when used in combination with plastic layer pads prevent discolouration of the fish from residual water and liquid.
Advocates of sustainable packaging
Today’s consumers want to be active participants in the environmental drive, thus, preference for sustainable, biodegradable and recyclable packaging is becoming popular.
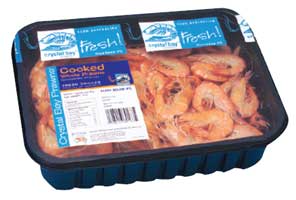
Besides consumer demand, government legislation and technology advances will drive sustainable packaging to a US$244 billion market by 2018, with Asia as the largest market owing to its 32% share of the overall market, Smithers Pira said in a report on sustainable packaging.
It said that the most common sustainable packaging trends include downsizing and lightweighting of packaging; increased recycling and waste recovery; increased use of recycled content; increased use of renewably sourced materials; and improvements in packaging and logistical efficiency.
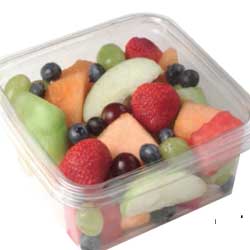
US thermoforming packaging company Fabri-Kal launched its new Alur On-The-Go Boxes, which are made from PET and 50% Post Consumer Resin (PCR). The 32-oz, 6-in single cell containers come with an outer-fit lid to enable heat-sealing of the food container. Boasting no flavour or odour transfer, the lids ensure freshness of food, says the company. The crystal-clear packaging will allow OEMs to display and sell a variety of meal and snack combinations, according to the Michigan-headquartered company, that also says the stackable boxes offer the option of customisable embossing.
Meanwhile, Fabri-Kal has expanded its sustainable packaging programme via a US$50 million facility in Idaho. The company intends to utilise locally produced agricultural fibre for its Greenware packaging line, which includes the on-the-go boxes.
Linpac has also unveiled a new addition to its Rfresh Evolve rigid vacuum skin packaging range, manufactured with a variety of label panel designs. The pre-formed trays are manufactured from up to 95% post consumer PET recyclate.
Mass producing cups
Swiss machine maker WM Thermoforming Machines in-line production machine Intec FT 900/3 is able to produce two-colour disposable cups made of multi-layer PP. It consists of an automatic dosing and feeding unit for raw material in granules, including the management and recycling system for the scrap material. It is also equipped with the latest generation of WM’s Next extruders, which thanks to the new screw design, guarantees higher productivity, less power consumption and, at the same time, increases process stability and homogeneity.
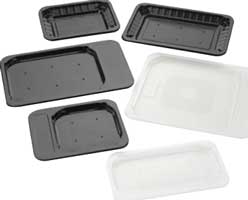
The WM extrusion line consists of a main extruder with a screw diameter of 75 mm where the regrinded material is mixed with PP-based material and filled with 70% of talc. The two co-extruders with a diameter of 45 mm are used for the outer coloured layer. The total extrusion capacity of the group is 1,500 kg/hour. The flat die head of the extrusion unit feeds a vertical laminating calender with three rolls creating a sheet width of 930 mm and a thickness ranging from 0.2 to 2 mm.
The extruded sheet is then sent in line to the transporting system of the thermoforming machine, which uses a tilting lower forming platen and a servo-assisted plugging unit. The forming tool will consist of a 54 cavity mould and can accommodate moulds with a maximum size of 880 x 520 mm, with clamping force of 75,000 DaN. The tilting system of the movable lower platen is developed based on an innovative double Desmodromic system of cams and levers operated by a servomotor.
After simultaneous forming and in-mould trimming, the cups are removed from the bottom half-mould through a tilting plate rotating at 75 degrees, which is driven by aspirated spindles. The cups are then transported and unloaded automatically into various rows on the conveyor belt feeding consecutively WM’s in-house developed rimming unit consisting of three rotating screws. This unit folds the upper edge of the cups prior to sending the piles to the counting, packing and boxing units.
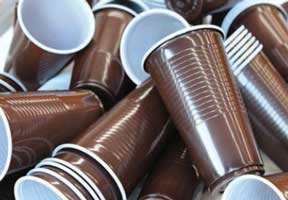
The waste of the residual perforated PP is sent in-line to a soundproofed grinding mill reducing the scrap into flakes in order to be blown into a dosing/ mixing unit located above the extrusion unit. This creates a closed loop from the raw material to the finished product with the direct in-line recycling of wasted material.
The Intec 900/3 can produce up to 120,000 pieces/hour of 200 cc cups, minimising energy consumption using only one operator, according to WM.
(PRA)Copyright (c) 2016 www.plasticsandrubberasia.com. All rights reserved.