Coal-to-plastics technology in China to take off
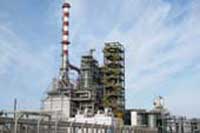
US firm Honeywell’s UOP business unit has broken ground on a new manufacturing capacity outside Shanghai to produce materials used to convert methanol from coal into feedstocks for making plastics, a significant milestone to enable China to meet the growing demand for plastics.
When it enters production in 2017, the catalyst production line in Zhangjiagang City in Jiangsu Province will produce catalysts used in Honeywell UOP's Advanced Methanol-to-Olefins (MTO) process technology.
Honeywell UOP developed the MTO process to convert methanol, which can readily be produced from coal or natural gas, into the olefins ethylene and propylene that are the primary chemicals used to manufacture plastics. The heart of the MTO process is a proprietary catalyst that facilitates the conversion of methanol into olefins.
"MTO is an innovative, proven technology that enables countries such as China that are rich in coal, but which have had to import petroleum, to make plastics," said Rajeev Gautam, President/CEO of Honeywell's Performance Materials and Technologies business group. "Honeywell UOP has licensed eight MTO units in China in just the last three years, and this new facility will allow us for the first time to fully manufacture MTO catalysts in China for our Chinese customers."
In 2011, Wison Clean Energy Company became the first company to license the Honeywell UOP MTO process, which entered commercial production in 2013. Since that time, seven other companies concluded MTO licensing agreements with Honeywell UOP. The most recent of these was Luxi Chemical Group last December.
While global demand for ethylene and propylene is growing by 4 to 5% per year, China is expected to invest more than US$100 billion in coal-to-chemicals technology by 2020. This would reduce China's dependence on imported oil for the manufacture of plastic resins, films and fibres that are used to make millions of different products.
"The Zhangjiagang facility makes it possible for Chinese manufacturers to meet the growing demand for petrochemicals with Honeywell UOP technology," said Rebecca Liebert, President/CEO of Honeywell UOP. "In addition, the operations use local raw materials, supporting economic development in Jiangsu Province, and incorporate zero-discharge wastewater treatment."
Honeywell's facility in Zhangjiagang opened in 2015. It produces other types of catalysts that are used in Honeywell UOP's Oleflex process, which converts propane into propylene, and in continuous catalyst regeneration (CCR) Platforming, which is used to produce high-octane gasoline. Over the past five years, Honeywell UOP has licensed its Oleflex technology to 30 producers globally, including 23 in China.
The Zhangjiagang facility is located in a modern industrial park about 85 miles northwest of Shanghai. In addition to Oleflex and MTO catalysts, the site produces adsorbent materials used in refining and petrochemical production and natural gas processing. Honeywell also is planning production of materials for other fast-growing technologies at the site.
Honeywell UOP has an 80-year history in China, beginning in 1937 when it built one of China's first refineries in Yumen. It was one of the first American companies invited back to China during the 1970s, to help modernise the Chinese petroleum industry. More recently, Honeywell UOP hydroprocessing and Platforming technology has helped China develop cleaner-burning transportation fuels to combat air pollution.
(PRA)Copyright (c) 2016 www.plasticsandrubberasia.com. All rights reserved.