Davis-Standard installs PLLA tubing line in China
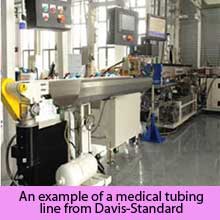
As the market for polymeric and antineoplastic devices for internal drug delivery continues to grow, so does manufacturing of micro-bore tubing made from PLLA (Poly-L-Lactide). US extrusion machinery maker Davis-Standard has sold a PLLA tubing line to a medical start-up in Tianjin, China. The line, installed last year, is said to have exceeded customer expectations by successfully producing products ranging from 1.7 mm to 2 mm OD with a tolerance of +/-20 microns.
“PLLA is a bio-absorbable resin ideal for applications that require a polymer to reside in the body for a controlled length of time before safely degrading and being absorbed internally,” explained Glenn Beasley, Senior Sales Engineer for Davis-Standard. “Very few companies process this material due to the high resin cost and difficulty in achieving a quality end result.”
Beasley continued, “To ensure immediate success, the customer relied on us to address their requirement of tight OD/ID tolerances and a smooth, gel-free tube surface when processing PLLA. The high cost of this material requires a fast start-up and no room for error during processing to keep costs reasonable.”
The line is capable of processing tubing from PLA and PLLA as well as a variety of other thermoplastic resins at rates up to 50 m/minute. Davis-Standard supplied the entire line, including a flood cooling tank. Beasley noted this type of cooling has traditionally been problematic for PLLA. However, recent developments in formulations permit water cooling for a limited residence time without compromising the tube surface.
The medical tubing sector continues to be a strong market for Davis-Standard in China. The company has a subsidiary in Suzhou with a lab line capable of demonstrating PLLA technology among other processes. Depending on application, Davis-Standard’s turn-key medical tubing systems can support extruder outputs up to 315 kg/hour) and line speeds up to 240 mpm. The material range includes PLA, PEEK, FPVC, polyurethane, nylon, PEBAX and FEP. Extruder options are available depending on process and application and engineered for a fast delivery and competitive pricing. Advantages include line control with data acquisition, precision vacuum sizing, closed loop ID/OD control, ultrasonic gauging, puller/cutter systems and more.
(PRA)Copyright (c) 2016 www.plasticsandrubberasia.com. All rights reserved.