Also, download this story from the electronic issue here
The numerous potential applications for industrial hemp match the nearly utopian dream of the composites industry that is on the look out for stronger yet cheaper materials, with a lower carbon footprint, says Angelica Buan in this report.
Potential, but outlawed
The cannabis plant, commonly known as marijuana, is a strictly regulated plant that is classified as a narcotic and one that has been receiving attention lately due to its potential to cure cancer. Aside from its medicinal properties, the weed, also known as Cannabis Sativa L, possesses ideal properties for a wide variety of industrial applications.
While marijuana is of the Cannabis Indica variety, the hemp used as industrial composite material is Cannabis Sativa, a non-psychoactive variety.
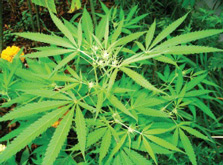
Nevertheless, industrial hemp has suffered the blow of being akin to its psychoactive substance-containing twin, marijuana. The cultivation of what would have been a nostrum material to drive market value for major industries has been politically curbed. For instance, the 1937 Marijuana Tax Act implemented in the US almost maimed the potential of industrial hemp, believed to be useful for nearly 50,000 variety of products ranging from building composites and cellophane to automotive parts. But recent developments have pushed several states in the US to legalise industrial hemp farming and research.
Countries like China, the UK and Canada (the latter has legalised industrial hemp production since 1992) continue to grow industrial hemp, while elsewhere, cultivating all varieties of cannabis is outlawed.
The origin of hemp can be traced back to Central/South Asia and its cultivation for fibre goes back to ancient China. Hemp is defined as containing less than 0.3% of the intoxicating substance Tetrahydrocannabinoids (THCs), compared to marijuana’s THC range of 10% to 30%.
Hemp farming is sustainable, as growing hemp requires no chemicals, pesticides or herbicides. In fact, hemp adds on and conditions the soil where it grows, while as a cash crop, hemp is grown in rotation with other crops.
Getting high on hemp
Industrial hemp as a material for the plastics industry has been known since the early 20th century, when hempderived cellulose was promoted as an affordable and renewable raw material.
Of all natural fibres, hemp merits as being the strongest and most durable. Hence, hemp-reinforced plastics are found to be up to ten times stronger than petroleumbased plastics, as well as 100% biodegradable.
Today, it is seeing its use in a variety of industries. In 2014, Canadian company Hempearth commissioned a Florida-based aircraft manufacturer to build the world’s first hemp fibre-based plane. Currently crowdfunding for an initial working capital of US$500,000, the company has designed a four-seater, two-engine aircraft with a cruising speed a little over 340 km/hour. It also has a wingspan of 12 m that will be constructed from at least 75% hemp, including the wings, seats, pillows, and outer shell.
The colour of the plane will be that of natural hemp fibre and the plan is for it to run completely on hemp biofuel, derived from the seed of the weed.
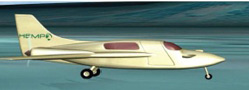
Using hemp as a biofuel could improve carbon efficiency, too, citing research done by Professor Richard Parnas at the University of Connecticut. He found that hemp converts to biodiesel at a 97% efficiency rate and can burn at lower temperatures than any other biodiesel available on the market.
According to Hempearth, it has tested the strength and durability of woven hemp material and says it is comparable to fibreglass, which is traditionally the material used in aircraft. As well, hemp is carbon neutral whereas fibreglass releases styrene into the environment. Hempearth plans to fly the hemp plane in Kitty Hawk, North Carolina, in 2016.
Rolling out fibre cars
Hemp is also making inroads into the car design segment and biodegradable cars are no longer a pipe dream. The concept has been around since Henry Ford’s biocomposite-made prototype car was built in 1941. The Ford prototype exhibited strength akin to steel, yet was 450 kg lighter than steel.
In 2010, Canada-based car maker Motive Industries unveiled the world’s first production-ready electric car (EV) with a body partly made of hemp. The three-door, four-seater hatchback Kestrel EV features a top speed of 90 km/hour and a range of 100 miles before it needs to be recharged. The resin-infused hemp body of the car is impact-resistant and exhibits strength comparable to fibreglass boats, but is lighter.
In fact, the Kestrel weighs less at 1,133 kg, with the battery, compared to similar-sized Ford Fusion weighing 1,690 kg. This means the Kestrel is 30% more fuel efficient, with the hemp composite helping lower the weight of the car panel by about 10%.
Following suit is German car maker BMW that released in 2013 i ts EV model . I t features hemp composites and a weight of 1,224 kg. The EV is powered by a 22-kWh lithium-ion battery, which is essential for the car to also weigh less (aside from ensuring fuel efficiency), as the battery accounts for about 20% of the car’s total mass.
The latest addition to the roster of hemp-based vehicles is the sports car produced by US car maker Renew. The Florida-based company manufactures the Ultra-Low Carbon Footprint (ULCF) sports car using hemp.
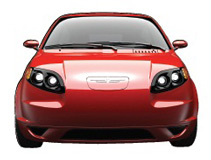
Aiming to create 100% carbon-neutral and nonpolluting cars, Renew’s gas-powered EVs feature 10% lower carbon footprint than average cars of this type, the company said, adding that once cellulosic hemp ethanol becomes available, the Renew EV model will be 50-85% greener.
Sniffing out opportunities
The changing climate has spurred research activities, specifically in the US, making the probability of hemp markets opening up becoming high.
Recently, a research project conducted at Bradley University, US, combined hemp fibre, sawdust and cotton with a recyclable solvent to replace PP resin. Luke Haverhals, Assistant Professor at Bradley is working with Brent Tiserat, a researcher at the USDA, to also find natural-based building materials.
Other new applications for hemp include skateboards pioneered by US-based apparel and skateboards maker Lotus Boards, which is producing what it says is the world’s first hemp-based 3D printed skateboard. The moulded grip-patterned skateboard is composed of 30% hemp, weighs 0.8 kg, and has energy savings between 22-45%, while carbon emission is reduced by 70%, compared to similar processes, according to Lotus Boards.
Powering batteries
Hemp fibres are found to be not only as strong as steel and more impact-resistant than fibreglass, but also better than graphene in terms of energy storage.
This property, thus, makes hemp a suitable material for high performance energy storage devices. Moreover, hemp fibre is found to be more conductive than copper and more flexible than rubber.
It also makes sheets with a high surface area, ideal for supercapacitors, a type of high-discharge battery. According to a study presented at the American Chemical Society (ACS) meeting held last year in San Francisco, part of the procedure involves processing cannabis via hydrothermal synthesis into carbon nanosheets for the supercapacitors. Using hemp for this purpose is cheaper than graphene, according to Dr David Mitlin of Clarkson University, New York. He also adds that the hemp’s electrochemical performance is at par, if not better, than graphene.
The part of the hemp used for the study was actually the leftover bast fibre, the inner bark, which typically ends up in landfills. The recycled waste fibre is, thus, made into energy storage devices that can be useful for EVs (for regenerative braking) and power tools, to name a few.
Meanwhile, start up Canadian company Alta Supercaps plans to scale up production of the hempbased supercapacitors for the oil and gas industry.
Hence, the legalisation of industrial hemp farming and more R&D are seeing various opportunities for this previously outlawed fibre.
(PRA)