Also, download this story from the electronic issue here
Global plastics manufacturing has expanded, specifically in terms of advancement in technologies to increase production efficiency and capacities, in line with the competitive nature of the sectors being served. As well, the incremental enduser applications for plastics are also fuelling growth for the manufacturing sector. It is against this backdrop that global plastics and rubber extrusion and converting systems machinery specialist Davis-Standard is reinforcing its commitment in the Asian region.
Global advantage brand
Innovative solutions that are efficient and sustainable are a common denominator for plastics processors and manufacturers to vie in the global market. In the same way, solutions providers that have a proven track record for high-quality equipment and services tend to stay ahead of the league.
Headquartered in Pawcatuck, Connecticut, US, Davis-Standard says it provides the highly required features for equipment, such as cost efficiency and durability, with a high return on investment.
Davis-Standard has extended its frontiers across the various markets around the globe through its “The Global Advantage” brand. Ditto to the company’s goals, it is able to supply technologically-advanced extrusion solutions to plastics processing industries around the world.
Catering to various markets with different consumer needs remains to be the cardinal element in The Global Advantage formula, which the company sums up as “quality service on global scale”
Having established a presence in several key markets in the US, Europe and Asia Pacific with sales and aftermarket offices, the company says global customers are assured of fast response by service technicians, as well as access to quality equipment upgrades.
According to Davis-Standard, whether processors need to add new capabilities or upgrade existing equipment, the company has spare parts, including current drives and controls, extruder refurbishing, extrusion feedscrew services, and extruder gearbox retrofits as well as modernisation packages to support cost-effective results with a fast turnaround. This is the company’s way of staying close to its customer base to serve thoroughly and promptly.
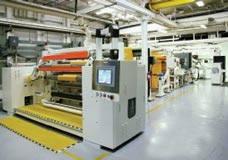
China – the be all market
China is an important market for Davis- Standard: the company has a facility located in the country, serving as the centrifuge for the other Asian markets. Set up in 2012, the Suzhou facility covers an area of 4,300 sq m.
It certainly is in an advantageous position in China, a country which, according to a report by Transparency Market Research (TMR), is expected to be the largest market for film machinery in the coming years.
Moreover, China is in proximity to other emerging economies in the Asian region. The TMR forecast points to Taiwan and India as anticipated markets to propel demand for film machinery, owing to an increasing demand from the packaging industry in view of the increase in the middle class population and industrialisation.
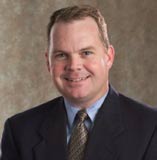
Come 20-23 May, Davis- Standard will once again exhibit at Chinaplas, dubbed as Asia’s largest plastics and rubber trade fair, to be held in Guangzhou. The extrusion specialist will showcase its dsX product line, specifically the new dsX s-tretch line for cast film.
PRA interviewed Jim Murphy, Vice-President of Global Sales and Marketing at Davis-Standard, to find out more about the company’s plans.
PRA :
How did Davis-Standard fare in 2014 in terms of market growth and sales?
Jim :
Our main area of focus for 2014 was the extrusion systems, where we saw a significant growth of nearly 80% followed by cast lines, 15%, and extrusion coating, 10%.
PRA :
Being globally present has become a main course of action for major players in the plastics industry. Davis-Standard fulfills this through its Global Advantage mantra. How does Davis- Standard undertake this compared to its competitors?
Jim :
There are three main reasons why our Global Advantage stands apart from the competition:
a)
We offer the industry’s most diverse offering of trusted equipment brands.
We are the company we are today because we offer a range of converting and extrusion systems. We have capabilities to customise solutions and also produce standard equipment to serve our customers.
b)
We have established brand recognition and sell products in every continent.
The key to our continued success has centered on building regional capabilities that allow us to think globally, but act locally. The continued expansion of our capabilities in China is an example of how we’re working to establish regional capabilities in the areas of service, installation and aftermarket support. We intend to continue to make progress in this area to separate us from others in the industry.
c)
We are a leader in technology and new product development.
Our R&D capabilities are among the best in the world. Examples of recent technologies impacting the marketplace include our high-speed aseptic packaging line; a new high-speed, high-output extruder; and our scrapless horizontal winder.
As a global leader in supplying equipment to the food and beverage packaging industries, we’re helping customers reduce waste and become more productive. We’ve also set ourselves apart from second tier suppliers due to customer access to fullscale laboratory facilities. We continue to invest in our laboratories with new equipment and staff.
PRA :
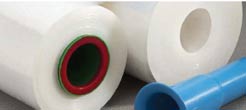
What will Davis-Standard display at Chinaplas 2015? What are the benefits of this machinery?
Jim :
We plan to promote our dsX product line, specifically our new dsX s-tretch line for cast film. This line is the first in-line pre-stretch cast film line of its kind, featuring integrated pre-stretch capabilities as an alternative to traditional prestretching methods, thus enabling processors to produce stronger, thinner film with greater efficiency. The system is available in three, five and seven-layer cast film options, which utilise the company’s proprietary and patented technologies.
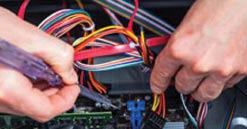
Advantages include a comprehensive, flexible and pre-configured design, and a smaller footprint at 2 m wide to simplify installation start-up. This line is capable of processing ultra thin films at speeds up to 1,000 m/minute. From a cost and environmental standpoint, benefits include consistently high quality pre-stretch film produced with greater efficiency and reduced waste via coreless winding.
PRA:
What does the dsX series of machinery comprise?
Jim:
The new dsX technology is representative of the many new innovations to be introduced as part of Davis-Standard’s Global Advantage initiative, helping customers gain a competitive edge by optimising their ability to respond to the everchanging needs of their markets.
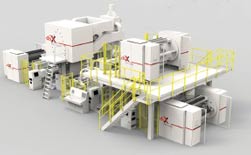
Introduced worldwide in 2013, the dsX series also includes the dsX flex-pack, dsX flex-film and dsX med-tube lines. The latter is a versatile solution for medical tubing allowing for materials processing ranging from polypropylene (PP) to fluorinated ethylene polypropylene (FEP) with a unique co-extruder arrangement and simple feedscrew changes. It offers a smaller footprint for clean rooms, a language-specific control system and fast delivery. Systems are available for single lumen, multi-lumen, IV catheter, corrugated drainage, integrated bump tubing and multi-layer tubing.
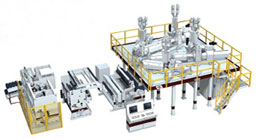
The dsX flex-pack extrusion coating line is a pre-configured system, available in two layouts, which support cost-sensitive flexible packaging applications. It was developed specifically for converters and printers looking to increase their flexible packaging business. The system ensures end-product quality, application versatility, greater uptime, and reduced productivity costs. Since it is designed as a high-value, pre-engineered system, it can be delivered in as fast as six months, while providing distinct advantages in the price-sensitive global flexible packaging market.
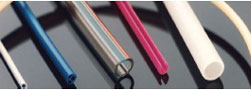
It caters to a variety of emerging application opportunities including: salted snack and noodle bags, toothpaste tubes, sachet packs personal care products, condiment packs and stand-up pouches.
The dsX flex-film is the latest in the line of the dsX technology. This pre-engineered blown film line is designed to serve the core of the blown film industry for applications in printing and laminating, flexible packaging, collation shrink and bag making, hood shrink and surface printing. Available in 1,900 mm and 2,500 mm sizes, processors can take advantage of Davis- Standard's high performance technology at an affordable price. This includes industry-leading air rings (UpJet), die and feedscrew designs for film uniformity, high output rates and long-lasting equipment performance. Options for different widths, die sizes and accommodations for multiple applications are available.
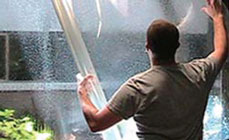
As for the UpJet air ring, it is geared toward commodity markets such as stretch film, can liners and industrial films. It can be used on existing and new blown film lines in manual or auto-profile mode. When used with Davis-Standard's automatic profile control and Centrex or Vertex dies, output increases have been as much as 40%. It is available in sizes ranging from 180 to 1,016 mm in manual or motorised elevation control and passive or automatic thickness profile control configurations.
PRA:
Following up on the dsX series of machines, how have these fared in the Asian market sector?
Jim:
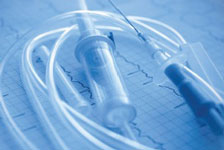
Our dsX machines have been very well received in Asia and throughout the world because they address price, performance and delivery. We’ve especially seen demand in Asia for the dsX med-tube and dsX flex-pack lines due to high demands in medical tubing and flexible packaging applications.
We have sold dsX s-tretch and dsX flex-pack lines as well, the first of their kind in Asia. And we estimate the demand for the dsX series to continue to grow.
PRA:
What types of machinery is the Suzhou facility producing? Are these sold to the Chinese market only or have there been orders fulfilled by Suzhou for other Asian countries? Are there any new services offered by the facility?
Jim:
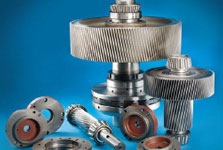
Suzhou has been a game-changer for us in Asia because it gives us regional manufacturing capabilities. Suzhou serves every major converting and extrusion coating market in the region.
The main products being manufactured in Suzhou and sold in China and throughout the ASEAN region include our feedscrews and control systems, Super Blue® extruder as well as the high speed FPVC systems for medical tubing.
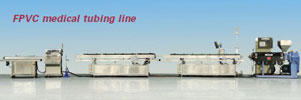
In addition to this, Suzhou can assemble and refurbish gear boxes and control panels. And in the future, we are looking at fabrication and assembly of downstream equipment to service the China and Asia markets.
PRA:
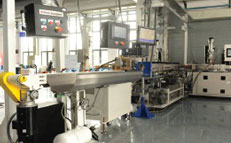
What sectors does Davis-Standard expect will generate demand for equipment/solutions?
Jim:
We definitely see an increased demand for upgrades of existing lines especially downstream equipment and control systems.
PRA:
Are there any updates on Davis-Standard’s green market solutions?
Jim:
All of our equipment is geared toward energy efficiency, reduced scrap and better processing. We expect this to be a continued effort for all our future equipment launches.
For instance, our dsX series of equipment is engineered to ensure:
- Energy efficiency
- Smaller footprint
- Less waste
PRA:
How will Davis-Standard’s participation in Chinaplas 2015 push further the Global Advantage brand?
Jim:
Chinaplas is Asia’s largest plastics and rubber trade exhibition and the second most influential exhibition in the world. Any time you have an opportunity to reach over 120,000 visitors, you need to take advantage! We look forward to seeing existing and potential customers at our booth, # 2.2E31.
To round-up, Davis-Standard systems encompass over ten product lines to support manufacturing applications and customers within every major industry. This includes the agriculture, automotive, construction, healthcare, energy, electronics, food and beverage packaging, and retail industries, among others.
With more than 950 employees worldwide and a network of independent sales agents and suppliers in nearly every country, we also have three manufacturing and technical facilities in the US, as well as subsidiaries with facilities in China, Germany and the UK.
(PRA)