Also, download this story from the electronic issue here
With the ongoing move from a fossil fuel-based economy to a more sustainable biobased one, manufacturers are looking for alternative solutions. And since China is a big market for biomaterials, given its population and the growth of biodegradable shopping bags and mulch film, Chinese firms are cashing in with the production of biodegradable PABT and PPC.
Biosuccinic acid goes into PBS and pigments
At Chinaplas 2014, Reverdia, a joint venture between Netherlands firms DSM and starch and starch-derivatives company Roquette Frères, was demonstrating a 100% biobased succinic acid. Using a proprietary biotechnology process, feedstock is converted to Biosuccinium, via low pH yeast process, developed by Reverdia. It enables the production of biobased PBS (polybutylene succinate) that can be used as a single polymer or in compounds for both durable and biodegradable applications.
Other applications include polyols for polyurethanes, coating and composite resins and phthalate-free plasticisers. End products include footwear, packaging, paints and many more. The company claims improved abrasion resistance in microcellular polyurethanes and better chemical resistance in TPU-based systems.
In 2012, Reverdia started producing Biosuccinium in Cassano Spinola, Italy, with a capacity of about 10,000 tonnes/year, and for which, the company becomes known as the world's first dedicated large-scale plant. Reverdia says it is preparing for a next phase with further expansion of its production.
Meanwhile, Swiss speciality chemicals producer Clariant says it is the first pigment producer to offer high performance pigments that are based on biosuccinic acid. It is incorporating renewable raw materials into its Quinacridone pigments produced at its Frankfurt-Hoechst facility in Germany. The biosuccinic acid is supplied by Myriant.
The pigments are targeted at the automotive, architectural and plastics industries as well as colourants used in printing applications tailored to individual needs.
Successful pilot plants for PHA and biobased DDDA
Privately held biopolymer maker Meredian and speciality food ingredients and solutions provider Tate & Lyle have started up pilot production of Meredian’s PHA (polyhydroxyalkanoate) formulation process, which converts biomass fermentation products to PHA. Tate & Lyle contributed its fermentation technology to the pilot trial; it supplies fermentation products like acidulants.
Meridian recently received food contact approval for its PHA from the US FDA, for use in packaging and storage containers. The pilot project also achieved production rates that make commercial production viable, thus opening the door for mass production of completely biodegradable plastics.
US-based industrial biotechnology company Verdezyne recently produced more than 1 tonne of biobased DDDA (dodecanedioic) acid using its proprietary yeast platform and downstream process. The Michigan Biotechnology Institute (MBI) and the Michigan State University (MSU) Bioeconomy Institute (BEI) worked with Verdezyne to run the process at the 4,000-l scale. The biobased DDDA is a raw material used to produce nylon 6.12 and resins.
The privately held company is currently evaluating several potential sites for producing plant oil-based DDDA in Malaysia. The facility will serve up to 30% of the US$200 million a year global market requirement for DDDA, which has been growing at an annual rate of 5.4%.
Malaysian conglomerate Sime Darby along with existing investors BP Alternative Energy Ventures, DSM Venturing, OVP Venture Partners and Monitor Ventures, have taken up a an investment of US$48 million in Verdezyne. With a 30% stake, Sime Darby is the single-largest shareholder in Verdezyne.
Chinese cash in with PABT and PPC
Chinese biodegradable/compostable polymer maker Jinhui Zhaolong High Technology has set up a 20,000- tonne/year line for PABT in Shanxi province, having completed its pre-trialling last year. The US$35 million facility expects to sell 70% of its output to Europe. The firm, a subsidiary of Shanxi Jinhui Energy Group, is also tying up with a South Korean materials supplier, it said at the Chinaplas show in Shanghai.
The US FDA-approved Ecoworld PABT is a terpolymer that is said to be completely biodegradable. It can be decomposed into carbon dioxide and water in 180 days by microorganisms under compostable conditions. It is made of 1.4 butanediol, adipic acid (feedstock for PA) and terephthalic acid using a onestep polymerisation technology. It allows for film properties, ageing resistance as well as 120% tear resistance and 130% impact strength, compared to PE, owing to its benzene ring, says Jinhui. With its properties, it is targeted at agriculture mulch film, rubbish bags, compostable bags and cling wrap, to name a few. The shelf life of PABT is 12 months, even after being processed to film products, says Jinhui.
But Jinhui’s PABT cannot be used on its own. It has to be compounded with other biodegradable materials such as PLA or starch.
Jinhui is also collaborating with another Chinese producer Tian Guan to use its PPC (PP carbonate) degradable composite in compounding Ecoworld PABT.
Tian Guan says it formulated PPC to counter the high price of barrier materials like EVOH. The new PPC formula comprises 40-50% carbon dioxide and the monomer is PP, polymerised to obtain the PPC. It is said to cost 60% less than EVOH, while still maintaining oxygen resistance at the same level and it is biodegradable, says Tian Guan.
Tian Guan received an award from the Chinese government in 2009. It has 50 local and three US patents on the biodegradable material.
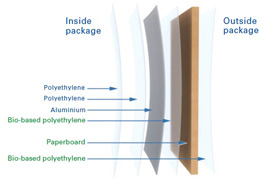
Packaging sector growing for biomaterials
Packaging solutions provider Tetra Pak says that all of the packaging it produces in Brazil is now using biobased low-density polyethylene (LDPE), which is produced by Brazilian materials maker Braskem. Combined with paperboard, the use of sugar canebased LDPE increases the content of materials from renewable sources to as much as 82% in a Tetra Brik Aseptic 1,000 ml Base packaging. Tetra Pak says it is also aiming to develop a 100% renewable packaging.
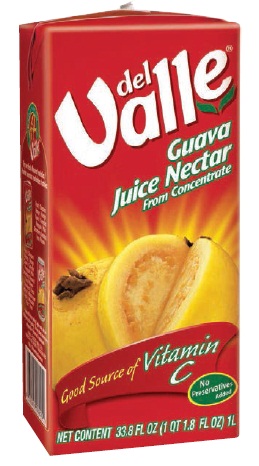
In February, Coca-Cola Brazil became the first company to use the new packaging for its Del Valle juice beverages, previously sold in regular cartons. Following that success, the pilot is now being extended to include all 150 customers that source from Tetra Pak Brazil – a total of more than 13 billion packs/year. No modification of the machine is needed for customers to switch to the new packaging materials. Tetra Pak has initially prioritised the Brazilian market but intends to expand the offer to more markets in future.
Meanwhile in Germany, BASF says it replaces up to 100% of the fossil resources used at the beginning of the integrated production process with certified biomass for its Ultramid polyamide. The share of renewable raw materials in the sales product is then indicated in the respective quantity. A third-party certification confirms to customers that BASF has used the required quantities of renewable raw materials which the customer has ordered in the value chain.
The resulting Ultramid, which is produced according to the so called mass balance approach, is identical in terms of formulation and quality but associated with lower green house gas emissions and saving of fossil resources. Also, existing plants and technologies along the value chain can continue to be used without changes.
BASF operates Ultramid polymerisation plants in Ludwigshafen, Germany; Antwerp, Belgium; Freeport, Texas and São Paulo, Brazil. Another plant is under construction in Shanghai, China.
(PRA)