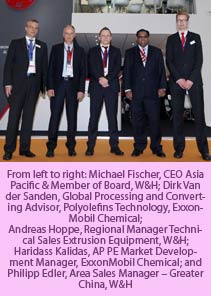
Global chemicals firm ExxonMobil Chemical and German extrusion machine maker Windmöller & Hölscher (W&H) say the five-layer technology for dedicated polyolefin (POD) blown films has taken off in a big way. Speaking at Chinaplas, officials from both companies said the technology is “breaking through global markets, with a huge turnaround expected in the next two to three years.”
The technology was first introduced at K2010 in Germany and shown at K2013 by W&H. At Chinaplas, it promoted its latest Varex II line based on ExxonMobil Chemical’s Exceed and Enable metallocene polyethylene (mPE) resins for collation shrink film for carbonated beverage bottles. The line is paired with a polyolefin-dedicated 400-mm Maxicone die; new high performance Arctis HP air ring and new Filmatic S II winder.
Dirk Van der Sanden, Global Processing and Converting Advisor, Polyolefins Technology, ExxonMobil Chemical, said that compared to conventional three-layer PE films, converters can benefit from higher productivity and greater flexibility to produce a broader range of film solutions from a single line.
According to Dirk, the additional two layers in the five-layer film structure allow for optical, mechanical and improved toughness/stiffness properties. “To achieve similar flexibility with a three-layer technology would possibly require two lines that could be more expensive to buy and to operate,” he added, explaining that when assuming a further downgauging of around 10 to 20% the ROI on the incremental investment of a five-layer over a three-layer line would typically be three years.
Meanwhile, Haridass Kalidas, AP PE Market Development Manager, ExxonMobil Chemical, said that the leap from three-layer to a five-layer film technology would allow a processor to stay ahead of the competition and afford extra capabilities.
This was reinforced by Michael Fischer, W&H’s CEO Asia Pacific, “The main leaders in the packaging industry have successfully transcended to three layers and are now discussing the POD five-layer line. This is because it offers higher output and it allows up to 30% downgauging. Furthermore, the move from three-layer formulations to five-layer structures significantly increases the options available for product development.”
He also said the five-layer POD technology would be ideal for the high volume Chinese market adding, “a processor only needs to focus on one machine and one product.”
Fischer also said W&H had sold its first Varex II line in China.
Extending advantages from formulation
Besides the optical properties, high output and downgauging, formulations can be designed to provide balanced in-use performance and a high holding force.
“Basically, it is how to put the benefits into practice; and to structure the layers so that the right material is in the right layer for a beneficial end strategy,” said Dirk.
Both the W&H and ExxonMobil Chemical officials say that the companies work together jointly to make the POD technology a success. “While W&H provides the hardware, ExxonMobil supplies the software: coupling state-of-the-art blown film equipment technology with the newest resin developments and film formulations.”
As to why the five-layer POD technology is successful globally, the ExxonMobil Chemical executives say that there is a “big pull from the downstream market as major brand owners are more concerned on using less material.”
Hence, the formulation propagated by W&H for a typical 40-micron, five-layer film structure for high clarity collation shrink film would contain a layer distribution of 10 / 17.5 / 45 / 17.5 / 10 - ABCBA
A 70% Exceed mPE 2018KB; 30% ExxonMobil LDPE 151HR
B 100% Enable mPE 35-05HH
C 15% Exceed mPE 2018KB; 45% ExxonMobil LDPE 165BW1; 40% ExxonMobil HDPE HTA108
B 100% Enable mPE 35-05HH
A 70% Exceed mPE 2018KB; 30% ExxonMobil LDPE 151HR
Hand/machine stretch wrap
The two partners have also cooperated on other technologies such as the power pre-stretch (PPS) film using Exceed and Enable mPE resins and Vistamaxx PBE (propylene-based elastomer) on W&H’s cast line for power pre-stretch films. Benefits include downgauging through an improved structure and the use of Vistamaxx to improve physical properties of the film, say the ExxonMobil Chemical officials.
According to Dirk, “There are two clear market segments for palletising applications: hand and machine stretch wrap. Currently, 70% of the Asian consumption is hand wrap film. The high tenacity film is produced in a single step as an alternative to the two-step pre-stretched handwrap film. Additionally, this film can be used on conventional machine wrap equipment.”
As for the high-end power pre-stretch machine wrap, the use of Exceed and Enable mPE resins and Vistamaxx PBE, results in a solution that delivers thin, tough cast stretch films with improved optical properties. Also possible are a high pre-stretch ratio and high speed wrapping performance, which can lead to low unit costs.
The ExxonMobil Chemical executives also said that the benefit of the technology is that a processor could serve both the machine and hand wrap markets on one line.
Meanwhile, looking to the future, applying its exclusive NanoLayer feedblock and die technology, US-based Cloeren Incorporated has also collaborated with ExxonMobil Chemical and W&H on the latest cast stretch film technology, which is able to deliver up to 33 layers and a thickness down to 8 microns. Conventional cast stretch films typically have five or seven layers.
One of the applications for NanoLayer cast stretch films is securing heavy load pallets. The films can deliver high wrapping speeds and excellent load retention, which can lead to more reliable shipping without load damage for products such as bottled water, soft drinks and other beverages.
(PRA)