Boat made from recyclable thermoplastic composite
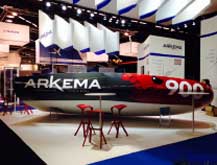
Companies are pushing their sustainable efforts: first the chair (http://www.plasticsandrubberasia.com/mar2016/materials2.html) and now comes a boat….made entirely from a recyclable thermoplastic composite.
France-headquartered chemicals firm Arkema teamed up with Lalou Multi to unveil a Mini 6.50 Arkema 3 “Innovation” prototype sailboat at the composites show, JEC World 2016, in Paris recently. The hull and the bridge of this 6.5 m boat are made from Arkema’s Elium resin, infused with carbon fibre.
Daniel Lebouvier, Technical Coordinator of the project at Arkema: “This is a liquid thermoplastic acrylic resin. It is processed in the same way as the resins traditionally used in boat building, and features all their mechanical properties, but is recyclable unlike those resins. This means that end‐of‐life parts made from this resin can be ground and reused to manufacture new parts. This is an answer to the major issue of the treatment of end‐of‐life composites (a topic that is dear to the heart of skipper Lalou Roucayrol). Arkema is the first company to be marketing a resin of this type, and the mini 6.50 Arkema 3 “Innovation” will be the first boat built with this type of resin to be sailing the oceans.”
The collaboration between Arkema and Lalou Multi is also called “open innovation”.
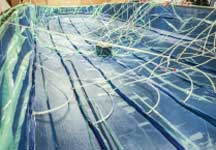
Fabienne Roucayrol, Project Manager at Lalou Multi: “As part of discussions on the 2014 – 2018 partnership with Arkema, Lalou Multi put forward the construction of a new boat, the objective being that this Mini 6.50 should be a showcase for Arkema products as well as our know‐how in their processing, in particular with this new innovative resin. Following R&D work over eighteen months and countless processing tests, we hit upon the right recipe in December 2015. The hull and the bridge of this new boat are made entirely from the Elium recyclable composite resin! This major innovation complements the many innovations introduced in the boat itself by architect Romaric Neyhousser.”
Elium is the first liquid thermoplastic resin to be used to manufacture composite parts. It is processed using straightforward methods identical to those used for thermoset resins, and features mechanical properties that are similar to epoxy resins. Its thermoplastic nature makes the Elium resin post‐formable and recyclable. It is 30 to 50% lighter than steel and just as tough, lends itself to complex designs and shapes and can be combined with fibreglass or carbon fibre.
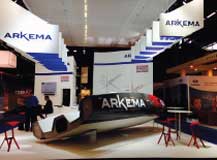
The construction of the boat was planned like a genuine research project. This new resin, fresh out of Arkema’s laboratories, had never been used in this type of manufacture. Lebouvier says that Elium applications were aiming at composites with fibreglass using the RTM (Resin Transfer Moulding) techniques. “In the case of the prototype, the infusion and carbon fibre technique was used. This was a more challenging situation in which we had no experience, in particular to manufacture large components. So we had to find the right conditions and fine-tune the product. We were able to do this, despite the tight timetable, thanks to very close collaboration between the Lalou Multi team, Romaric Neyhousser, and Arkema’s research teams.”
The story between the enterprise Lalou Multi and Arkema began in 2012, at the time of the construction of the Multi 50 trimaran of skipper Lalou Roucayrol. Driven by weight reduction and reliability objectives, Lalou had no hesitation in innovating in ocean racing by calling upon Arkema’s products to build his trimaran. In fact, the cockpit glazing and the helmsman’s protective bubbles are fitted with Altuglas ShieldUp sheeting, which helps significantly reduce overall weight while affording optical properties. And unlike other boats, the entire trimaran is assembled with glue joints, which deliver an optimum flexibility – sturdiness – weight ratio.
For this new Lalou Multi boat, the objective of the architect, the skipper and Arkema was to include as many technologies from the Group as possible from the design stage.
- Bostik’s adhesives were used for the structural assembly of the boat. In particular, the bulkheads and the bridge were glued to the hull with methacrylate and MS Polymers adhesives, and the foamed structures were assembled using a polyurethane adhesive.
- The cockpit windows and the hood were made from Altuglas ShieldUp, a material that is transparent like glass but lighter and able to withstand extreme conditions.
The Mini 6.50 Arkema 3 “Innovation” is expected to set sail in late April 2016.
(PRA)Copyright (c) 2016 www.plasticsandrubberasia.com. All rights reserved.