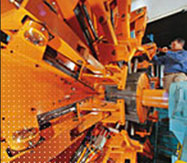
North Carolina-based Wilmington Machinery, a leader in high capacity Rotary Extrusion Blow Moulding Machines introduces its all new In-Line Multi-Clamp Intermittent Reciprocating Blow Moulding Machine, which is built for medium volume production of industrial, agricultural and other forms of rigid packaging. Manufacturers of automotive, toys or other industrial applications will also benefit from Wilmington Machinery’s new technology.
The machines produce medium/heavy wall parts at rates of up to 600 pieces an hour. Models are available for both monolayer and coex (multi-layer) mouldings. The Wilmington in-line machines are single parison for precise and repeatable mouldings. Cycle times meet or exceed those obtained by other technologies such as shuttles, long strokes, conventional reciprocating and others. The combination of single parison and parison programming creates especially high quality parts.
For more than four decades, Wilmington Machinery has consistently proven itself as a premiere builder of high-capacity extrusion blow moulding and structural foam injection machinery. The company also builds custom machinery under proprietary arrangements.
It supplies foam sheet extrusion, co-extrusion, industrial blow moulding, thermoforming, injection moulding and hybrid processes to its customer base comprised of large and small processors seeking expertise in plastics machinery design and build.
Wilmington Machinery operates a modern 65,000 sqft plant equipped with lifting capacity up to 40 tonnes and direct interstate and port access. Wilmington Machinery offers services including 3-D modelling and animation, along with expert mechanical, electrical and electronic design of controls and hydraulics.
(PRA)