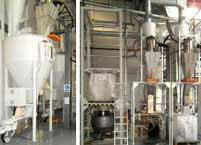
Benecke Changshun Auto Trim, a joint venture between Germany’s Benecke-Kaliko, a part of the ContiTech Group, and China’s Jiangsu Changshun Group has officially started operation its new production line for interior films made of thermoplastic elastomer based on olefin (TPO) into operation.
This new production capacity is expected to meet the demand growth in the Chinese automotive industry for high-quality TPO films. Available as compact films and foam sheets, the Benecke films have various applications that include instrument panels, door paneling and centre consoles. For the new TPO production line, Benecke Changshun Auto Trim has practically built its own new factory, complete with production hall, numerous ancillary rooms and a warehouse at a cost of around EUR7 million according to company insiders.
From silo to film extruder, Bensheim-headquartered ProTec Polymer Processing designed and implemented all of the material supply equipment for the Benecke Changshun Auto Trim film production line. Apart from supplying virgin materials, this system also creates value by returning regrind from the continuous edge trimming that is inevitably created during production and the balls that occur when the process starts up after a change of material back into the process. Since the TPO interior films are up to 50 % lighter than the conventional PVC films, the TPO regrind exhibits significantly impaired flow characteristics. As a result, the regrind conveyor had to be equipped with special process controls and plant technology that was adapted to the unique flow characteristics.
The film extruder, a twin-screw extruder, is run underfed. Throughput is regulated by the SOMOS Gramix S9 gravimetric dosing and mixing system fitted above the material feeder.
It can handle up to nine components (primary and secondary components in different ratios depending on the recipe). Two of these can be regrind components, which are separated for light and dark regrind types. The extruder is operated with a throughput of up to 800 kg/h; the regrind proportion in this case can be up to 50 %.
The SOMOS Gramix S9 gravimetric dosing and mixing system is suitable for supplying extruders operating in overfeeding or underfeeding mode, continuous production processes used in coextrusion or blow moulding applications with a longitudinally homogeneous material mixture and at throughputs of up to 2,400 kg/h.
The dosing system features convenient operation via touch-screen display and offers diverse display and evaluation functions. Current process states in the dosing system can be intuitively detected while any outages and faults are indicated in clear text. The Gramix controller also automatically detects the dosing screws used in the individual dosing stations.
(PRA)