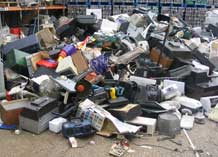
The large-scale incineration or dumping of plastic films in landfills could soon be a thing of the past as new technologies seek to convert plastics into fuels and other useful products. Economic factors and fundamental difficulties with handling and sorting at recycling facilities has resulted in plastic film recycling still being in the early stages of development, especially in comparison to recycling processes for dense rigid plastics such as PET used widely in the drinks industry.
In the UK, current data suggests 1.7 million tonnes of consumer plastic packaging – 1.1 million rigid, 0.6 million film – were consumed last year. Only 440,000 tonnes was collected for recycling. It is estimated that over 1.2 million tonnes of plastic, used in consumer packaging alone, is not being recycled.
As a result, policy around the world has looked at alternative solutions to reduce the impact of plastic films, especially plastic bags, on the environment. Controversial policies have included the banning of single-use plastic bags and imposing charges on consumers.
However, Axion Consulting – a UK-based waste processing consultancy specialising in plastics recycling – believes it is now technically feasible and economically viable to begin the large scale collection of low grade plastic films for conversion into fuels and other recycled products.
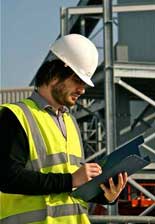
Speaking at the 12th European Gasification Conference – organised by the Institution of Chemical Engineers (IChemE) in the Netherlands – Sam Haig, IChemE member and senior engineer at Axion Consulting, said: “Plastic films are lightweight and 2D in shape and can easily get mixed into other recycling streams, such as paper, causing contamination. They also have a tendency to get trapped in recycling machinery requiring regular maintenance. As a result, plastic films have been excluded from most public household waste collection schemes around the world.”
He added, “However, a new generation of machinery uses a flow of air to help detect and remove around 95% of films from co-mingled kerbside waste collections. The process is likely to be more economical and efficient than current machine-based and hand-picking operations. Importantly, the recycled films can be used for products including refuse sacks and signage for retailers.”
Haig continued: “Our analysis also suggests that it is now economically viable to convert low grade plastics into fuel. We studied five chemical engineering processes and concluded that three: fast pyrolysis; depolymerisation; and gasification with biological treatment provided significant financial returns over a ten year period.
“The more efficient sorting of films at recycling facilities and the conversion to fuels are clearly better solutions than disposal in landfills or by incineration. However, avoiding irresponsible disposal in the first place and increasing our efforts to re-use plastic films and bags should be the priority for everyone.”
Sam Haig was speaking at the 12th European Gasification Conference in Rotterdam, the Netherlands, 10–13 March 2014.
When asked if plastics that are difficult to recycle be phased out, he said, “Plastics are part of our everyday lives and each type has been developed specifically for its unique properties. It would be challenging to phase out these difficult to recycle plastics. The solution is to provide the right infrastructure for collection, sorting and recycling.”
As for the way households recycle plastics in the future, he added that there is a lot of discussion about the ‘best’ way to collect and recycle all household materials, including plastics. “There are also questions about which plastics we should be using. However, the major change to recycling in the future needs to be a drive towards the next generation of technologies which will allow the recycling and re-use of more of our materials, including plastic films. Consumers also have a responsibility re-use and dispose of plastics responsibly.”
Most consumer products made from films have short lives and include plastic shopping bags and wrapping for food such as bread, fruit and vegetables. Generally, these are made of Low Density Polyethylene (LDPE) or High Density Polyethylene (HDPE).
Consumer products made from rigid plastics can be categorised into short-life and long-life.
The most common short-life applications are in product packaging and include bottles used for soft drinks – Polyethylene Terephthalate (PET); milk – HDPE; cleaning products – Polypropylene (PP) and HDPE; food trays – PP; and pots – PP.
Long-life plastic items are generally parts of products in and of themselves: TVs, fridges, car parts, etc. There is a huge range of different types of plastic used in order to cater for particular niche requirements, but the main ones are PP and Polystyrene (PS).
Some plastics are governed by legislation dictating recycling targets e.g. End-of-Life Vehicle Directive, and Waste Electrical and Electronic Equipment Regulations). Plastic packaging is not subject to this type of legislation.
Why are some plastics currently not recycled?
Rigid plastics are much denser and more rigid than films. They are much easier to transport and handle in recycling facilities. Plastic films have a tendency to pick up and retain moisture and contamination much more than rigid plastics. This also makes them more difficult to identify during sorting. Many plastic films are constructed as multi-layer sheets of several different types of plastic, which means they are not as easy to re-extrude to a suitable product.
Commercial and public relations (PR) factors also influence recycling. Drinks manufacturers have rolled out PR initiatives to enable ‘closed loop’ recycling of their own bottles. The commercial values of recycled ‘clear’ PET and ‘natural’ HDPE streams are much higher than PP, PS and PVC (or coloured PET/HDPE).
What are the challenges when recycling plastics?
All plastics have to be sorted to keep levels of contamination low. The challenge lies in separating the different plastic types and the end markets for the recycled products. Clear PET bottles are used almost exclusively for drinks, as are natural HDPE bottles. This means it is possible to sort on both polymer type and colour to produce a food grade plastic that can be re-manufactured into a bottle.
PP, which along with LDPE, HDPE and PET make up the vast majority of consumer plastic packaging, is not as easily sorted. In the UK, many authorities do not collect them as part of their kerbside collections. Material Recovery Facilities (MRFs) are not typically set-up to produce a purified PP stream.
In addition, PP is used for fatty foods and cosmetics requiring the packaging to be thoroughly washed before it can be re-extruded. Recycled PP cannot be reused in food-grade packaging applications as non-food-grade PP makes up a large proportion of the PP waste and cannot yet be effectively sorted from food-grade PP. The recycled plastic can only be used as non-food-grade polymer attracting a lower value than food-grade. The economics of recycling PP are not as favourable as PET and HDPE.
Recycled plastics and fuel
Depending on the technology used, low grade waste plastics can be converted into diesel or gasoline-like products, or into Synthesis Gas (Syngas). The product can undergo further processing into a variety of products including ethanol.
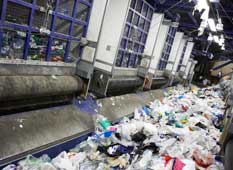
Syngas can be used in an on-site Combined Heat and Power (CHP) engine, or the diesel, gasoline and ethanol products can be blended with road fuels to power vehicles.
Current technologies advertise a conversion ratio of 1,000 kg waste plastic = 1,000 L fuel oil; a syngas to ethanol plant could theoretically have a conversion ratio of 1,000 kg waste plastic = 750 L ethanol.
About IChemE
IChemE (Institution of Chemical Engineers) is the hub for chemical, biochemical and process engineering professionals worldwide. With a growing global membership of over 38,000, the Institution is at the heart of the process community, promoting competence and a commitment to best practice, advancing the discipline for the benefit of society, encouraging young people in science and engineering and supporting the professional development of its members.