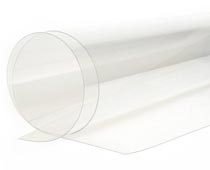
With smart materials being one of the fastest growing areas of materials technology, Sabic and Cima NanoTech, a Singapore and US-based company, have jointly developed a transparent conductive polycarbonate film that has the potential to revolutionise the materials used in consumer electronics, household goods, automotive, architecture and healthcare.
The new material, designed to provide “next generation” functionality, has the potential to further enhance performance, enable new innovative applications and open doors for new product designs, Ernesto Occhiello, Sabic Executive Vice President, Technology and Innovation, explained. This could translate into faster response touch screens for consumer electronics, transparent “no-line” anti-fogging capabilities for automotive windows, better EMI shielding effectiveness for electronics, and transparent WiFi/Bluetooth antennas for mobile devices like smartphones, tablets, laptops and all-in-one computers.
Sabic engaged in a joint collaboration with Cima NanoTech in the latter half of 2013 to develop the promising new material, which will be available for customer trials later this year. /p>
The collaboration, leveraging both Cima NanoTech’s proprietary SANTE nanoparticle technology and Sabic’s Lexan film, a polycarbonate material, has resulted in the development of a new series of transparent conductive materials that are lightweight with transparency, conductivity and high flexibility.
SANTE technology, a patented self-assembling nanoparticle technology platform, stands alone in providing high transparency with ultra-low electrical resistance, which is said to be ten times better than the incumbent indium tin oxide (ITO).
Said Jon Brodd, CEO of Cima NanoTech, “In addition to its ability to meet optical grade specifications for display and touch applications, SANTE nanoparticle technology is also more cost effective as coating is performed via a wet coating, roll-to-roll process versus sheet-to-sheet.” The conductive SANTE network is also mechanically robust, thus allowing it to withstand flexing, stretching, torsion and tension for flexible applications. The substrate can also be thermoformed into various curved and 3D form factors.
(PRA)