Also, download this story from the electronic issue here
US firm DuPont Packaging and Industrial Polymers highlighted how its collaboration with market players can open up multiple possibilities for increasing the functionality and attractiveness of plastic packaging, while at the same time reducing footprint and wastage of food, at the Aprilheld Chinaplas show in Shanghai.
DuPont Packaging and Industrial Polymers focused on a range of new materials for thinner, multi-layer films for lidding applications and thermoformed trays, special adhesive resins for the TripleBubble technology, renewably sourced tie-resins and polymer modifiers, as well as compatibilisers for use in the recycling of mixed plastic waste.
Roger Kant, Regional Marketing Director, Asia Pacific, explained that there are two ways of reducing the use of materials in packaging: by downgauging and by improving packaging functionality that in turn can reduce food waste at source.
“An important new technology is the ultra-thin reorientation structure, which is just entering the market place,” he said, adding that DuPont is collaborating with equipment suppliers to develop this technology with special adhesives.
"It's an embryonic technology," added the Australia-based executive. “But it will become important for the packaging technology over the next few years. In fact, the first line is being installed in China, even as we speak,” said Kant.
Collaborations with machine makers
As such, DuPont and blown film machine maker Reifenhäuser Kiefel Extrusion, based in Worms, Germany, have collaborated to bring a new APET-based Appeel sealant resin. It is used for the production of PA-based lidding films, which seal directly to trays of 100% APET, obviating the need for APET/LDPE tray laminates.
Another novelty is a special grade of Surlyn packaging that allows the production of thermoformable barrier films that can be made 20% thinner than conventional seven-layer PA/PE films, allowing for lower costs, improved optical properties, higher puncture/abrasion resistance and improved sealing properties.
In both of the above examples, DuPont contributes its know-how in packaging plastics, while Reifenhäuser optimises its Evolution barrier blown film technology.
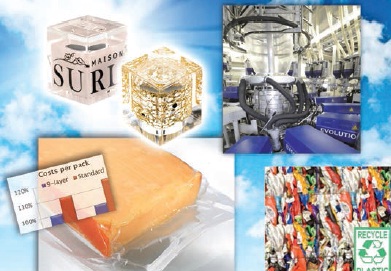
DuPont and another German machine maker Kuhne have also cooperated to extend the latter’s TripleBubble process for the production of biaxially stretched films. With up to 11 layers of functional plastics, Surlyn packaging resins and DuPont’s Bynel adhesive resins, these films are available in thicknesses of 20-110 microns. Benefits are adjustable shrinkage of up to 60%, high barrier properties, high gloss and, despite the comparatively low thickness, high tear strength and puncture resistance. Raw material savings of up to 50% are possible.
Stretching the sustainability curve
A new development is DuPont’s Entira EP compatibilisers that lower the barriers for the material recycling of packaging. The company says that small additions of 4% to the regrind of inherently incompatible packaging polymers make for a more economical and efficient re-compounding process. Consequently, the tensile strength, elongation at break and, in particular, the impact strength of the recyclate is increased to a level that meets the demands for highperformance applications. Grades optimised for specific applications are currently at the development stage.
Meanwhile, in bioplastics, DuPont is working with Brazilian biopolymer maker Braskem to develop renewably sourced tie-resins and polymer modifiers to extend its existing range of Bynel and Fusabond resins.
“Recycling multi-layer films is challenging, especially at the post-consumer stage, but with the addition of the biobased Fusabond, these films can be recycled,” said Kant.
Thus, DuPont will use Braskem’s sugarcanesourced PE to produce drop-in alternatives that are fully recyclable in PE waste streams.
The US firm says its aim is to help multi-layer packaging manufacturers that have started to use Braskem’s green PE to increase the renewable material content in their overall structures.
Target applications for biobased Fusabond include applications like wood/plastic composites, starch/ PE compounds and glass-fibre/PE compounds where use of a renewably sourced modifier significantly increases the renewable material percentage in the structures.
China’s meat packaging next
Kant also said that the company is looking at China’s growing market for meat packaging.
“We are collaborating with major retailers to understand the needs of consumers, in terms of food safety. Packaging to meet these needs is the future and we want to work alongside retailers in China," he said.
Philippe Hanck, the division's Shanghai-based Managing Director for Asia Pacific, said, “Science driven innovations continue to be a strong basis for DuPont’s answers to global market demands. However, we strongly believe that sustainable success needs more than the efforts of a single company.”
He added, “There is a need to work through collaboration through the value chain; not only with direct customers but with machine suppliers and converters.”
Hanck says that solutions for the major challenges of today’s world require global collaborations. “This is particularly true for the development of safe packaging solutions,” he concluded.
(PRA)