At the recent Chinaplas 2013 show, US companies displayed their technology prowess and updates to products, with materials suppliers tying up with local Chinese manufacturers to showcase technology at a localised level.
ExxonMobil ties up with local machine maker
Materials firm ExxonMobil Chemical showcased how its Exceed and Enable metallocene polyethylene (mPE) resins and Vistamaxx propylene-based elastomer (PBE) can be used to provide opportunities for downgauging. The firm has had various success stories in China and for this reason is seeing a 15% growth for its mPE business, compared to the general PE market, according to Thomas Deman, ExxonMobil Chemical’s Global Marketing Manager of PE.
One such demonstration shown at Chinese machine maker Xinle Huabao Plastic Machinery’s booth was a five-layer cast line running a “tough cast power” pre-stretch machine wrap packaging film using Exceed and Enable mPEs and Vistamaxx PBE.
“By adding the elastomers into the mPE formulation, the processor is able to downgauge by up to 40% to 15-20 microns (instead of the usual 20-25 microns); plus the film is able to be pre-stretched by up to 250% (hence the term used tough cast power),” said Deman.
Furthermore, Deman says the elastomers add value to the film. “Vistamaxx PBE provides the cling requirement at a much lower dosage of 4% when used with LLDPE, compared with up to 50% for ULDPE.” A typical fivelayer cast power pre-stretch film structure includes the 96-100% LLDPE (in the outer layers), 100% mPE resins (in the inner layers), with 4% Vistamaxx PBE.
“Besides allowing for a more sustainable production, it is also more energy efficient; results in significant cost savings plus the film produced is not only thinner but tougher and with improved optical properties,” reiterated Haridass Kalidas, Asia Pacific PE Market Development Manager.

Ashok Sapaliga, Asia Pacific Market Development Manager for Vistamaxx in Film says the company has a two-way approach to the market. “We set solutions for customers and want to go beyond the product. Our goal is to help customers high performance sustainable end products.”
Meanwhile, machine maker Xinle is also reaping the benefits of the elastomers, said General Manager Guoliang Ma. “Through the cooperation with ExxonMobil Chemical, we have increased the output of the machine from 450 to 650 kg/hour,” said Ma, adding that the Hebei-headquartered firm sells not only the machine but the entire stretch film solution to customers. “Xinle as a machine supplier has the formulation for the power stretch film, so that we are able to resolve film quality issues and improve processability."
Xinle had a turnover of RMB120 million last year and expects a 20% increase this year, mainly due to ExxonMobil Chemical’s solutions, said Ma. Xinle exports half its output to countries like the US, Brazil, Mexico, Turkey, Iraq, Russia, Malaysia and South Korea.
PolyOne basks in investment limelight
Specialised polymer material provider PolyOne achieved a number of milestones in China last year, including the expansion of an existing R&D centre in Shanghai, and is evaluating future expansions, said Mark Crist, Vice-President of Asia. “We are committed to China. In fact, the Asia Pacific headquarters is based in China, and contrary to what critics may say, this is the right location since most of our customers have facilities in China, too.”
Over a period of three years, the US$2.9 billion firm has acquired a manufacturer of glass and carbon fibre reinforced polymers and advanced composite products Glasforms, Spartech (custom sheet and rollstock and packaging business) and Colormatrix. “PolyOne has been taking the cash it makes and investing it in acquisitions. We will continue on this path,” said Crist. The investments, which tie in with PolyOne’s transition from cyclical commodity markets into speciality applications, have been paying off. In the first quarter of 2013, its revenue rose 7.5% to US$801.1 million from the year-earlier quarter, attributed to its speciality businesses that delivered a 34.4% increase.
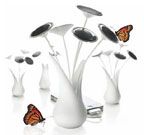
“Spartech (now known as Design Structures and Solutions) is very much like what PolyOne was in 2005; while Glasforms will use PolyOne’s global footprint to expand.” Crist also commented that “integration is a challenge when products are similar but since Colomatrix offers liquid colour solutions and PolyOne colour masterbatch, both are in different spaces.”
Meanwhile, regarding the acquisition of Spartech, which is a sheet thermoformer and would mean that PolyOne will be competing with its customers, Crist said, “Conventional wisdom will say there is a conflict but actually we have found little overlaps and more synergies globally."
At Chinaplas, it showcased a global collaboration with Netherlands-based Xindao and its Chinese design studio XD Design to increase the content of renewable resources within the new XD Design Sunshine Solar Charger. The moulded casing components are made from PolyOne’s reSound biopolymer, which Xindao estimates will reduce the CO2 footprint for this product by as much as 35%. The 30% ABS and PC bio-derived polymer is not universally applied, Crist agreed, due to the higher price. “We are only targeting the high-end markets,” he added.
PolyOne also unveiled its new InVisiO colour and design services, which are tailored to help brand managers and designers evaluate colour and design alternatives to accelerate the product development process, strengthen brand equity and build marketplace excitement.
DuPont places emphasis on R&D in China
DuPont Performance Polymers plans to expand its Shanghai R&D centre later this year, further enhancing its application-development capabilities with the addition of 200 staff (to total 500) and doubling the space. Woong Chung, Global Technical Services Manager, said 50% of new materials that are offered globally are developed by the local Chinese team. “The centre was set up two years ago for automotive part testing, but now we will expand our focus to new materials, new designs and prototyping.”
In terms of design capabilities, Woong says DuPont has 20 CAD/CAE designers in the region, claiming that it is the only firm providing this full scope of design support. “We strongly believe in design solutions to add real value to customers and we look forward to continuing our collaborative relationship with the automotive, industrial and consumer segments in China.”
In the automotive sector, the focus is on lightweighting, efficiency in automotive components for lower CO2 emissions and fuel economy, with downsizing of engines and focus on hybrid and electric cars as well as total system costs. New advance products for automotive applications include the Zytel Long Chain Polyamides (LCPAs).
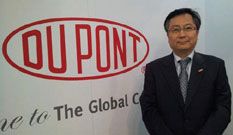
A number of Chinese automotive makers have adopted the Zytel nylon resin and Vamac ethylene acrylic elastomer in the air-intake manifold, cylinder head cover and air ducts, allowing up to 40% decrease in component weight, compared with the metal counterparts.
“We also custom make and localise the materials to suit Chinese demands and specific customer requests since Chinese OEMs want different types of materials,” said Woong, adding that the automotive sector is demanding but DuPont is able to cater to the needs with its predictive engineering and tool shop availability at the technical centre.
At Chinaplas, the firm also introduced a renewably sourced Zytel RS HTN grade that can be used for thinner, lighter handheld device housings while Zytel NHFR halogen-free fire retardant material offers a cleaner, more effective solution for this industry.
(PRA)