Davis-Standard: Catering to the needs of Asia
Also, download this story from the electronic issue here
Global plastics and rubber extrusion and converting systems machinery specialist Davis-Standard is riding high on the back of a year that has started off well, said newly appointed President/CEO Jim Murphy, speaking at the Chinaplas show in Guangzhou recently. Furthermore, the company is adding on more resources at its technical facility in Suzhou to cater to the demands.
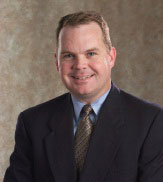
On a roll with new projects
Headquartered in Pawcatuck, Connecticut, US, Davis- Standard is seeing interest in new projects, according to Murphy, who has been with Davis-Standard for more than 25 years and was leading the Sales and Marketing efforts, prior to his promotion.
“We are expecting a 10% growth increase in orders this year. We already have a backlog of orders from our worldwide sales,” he commented, adding that the growth is expected from all regions.
“North American markets are improving, Europe has turned the corner and we expect orders to pick up, while opportunities are growing in Asia, in countries like India, Indonesia, Thailand, Malaysia and South Korea.”
Catering to the needs of regional customers
The company has manufacturing and technical facilities in the US as well as subsidiaries with facilities in China, Germany and the UK.
In China, Davis-Standard has a laboratory facility in Suzhou, which is building up its capabilities every year, said Murphy. “The Suzhou facility has been a game-changer for Davis-Standard due to regional manufacturing capabilities and the ability to serve every major converting and extrusion coating market in Asia.”
In April, it had an open house and welcomed nearly 60 industry leaders from different companies throughout China. “This event was the first of many to be planned at this location,” said Murphy, adding that the company plans on having regular open houses to share new technology and processes with customers.
“This is all part of Davis-Standard’s commitment to offering The Global Advantage to customers in the region.”
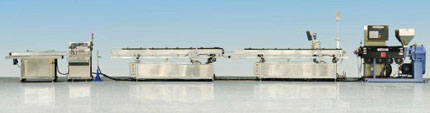
Presentations were made on feedscrew and extruder design, microbore tube processing, extrusion of FEP resins, ultrasonic technology, parts and aftermarket services, PEBAX extrusion for medical tubing, and a live demonstration on the laboratory’s FPVC and Micro Bore tubing lines.
Davis-Standard representatives from the US and China as well as representatives from Arkema, DuPont and Zumbach were involved in the presentation.
To allow for customer trials, the Suzhou laboratory is equipped with a high-speed FPVC extrusion system and multi-purpose microbore tubing line to support the continued growth of China’s medical industry.
The FPVC line is capable of line speeds from 5 to 100 m/minute for processing 2 mm to 8mm OD tubing with accuracy of +/- 50u. Line components include a 63 mm extruder, 8 m water cooling, precision internal air supply, OD gauge and combination puller-cutter.
The multipurpose Micro Bore tubing line is designed for single or dual layer tubing, and single lumen tubing with or without a stripe. It is equipped with two extruders, OD/ID wall thickness measuring and controlling system, close loop control via vacuum sizing tank and puller, and a high level central control system. Both lines are available for customer trials and R&D applications.
Future product lines in China
Murphy says that most equipment in China is imported for high technology manufacturing but Davis-Standard is able to cater to the needs locally. “We are able to offer the solutions locally, and meet the requirements in terms of speed, uptime and quality.”
As such, the main products being manufactured in Suzhou and sold throughout the region include extruders up to 90 mm, feedscrews, PLC control systems as well as high speed FPVC systems for medical tubing.
Furthermore, Murphy says the Davis-Standard’s extrusion lines are distinguished in terms of quality production, and the company has the technology and machine designs to deliver that. “The melt processing, wide lines, web handling at high speeds and control technology all tie in to offer a quality product.”
Additionally, the Suzhou facility can assemble and refurbish gear boxes and control panels, and there are plans to add fabrication and assembly of downstream equipment to service the China and Asia markets, said Murphy.
“We have added people and process support for future developments.” The company will also be keeping a close watch on food packaging solutions, since the trend is for flexible packaging. “The middle classes are driving growth in the distribution of food.”
He also shared that the company plans to start the production of a low-voltage wire insulation extruder line in Suzhou. “We are planning to start this up by the end of the year.”
This should bode well for the company since China’s building and construction market has great potential due to economic development and further urbanisation, according to the China Real Estate Research Committee.
Even against the slower GDP growth in the country, it is expected that over the next ten years, China’s urbanisation will reach 65-70% and the urban resident population will increase by another 300 million. This will, thus, require for the need of 800 million sq m of residential housing in order to accommodate the urban population.
Hence, Murphy says the company is working on other developments and “will keep adding on capabilities, products and support in Suzhou.”
New cell for elastomer applications
Meanwhile, tying up with German rubber extrusion solutions provider Uth, Davis-Standard has recently introduced a new technical cell for elastomer applications at its laboratory at its headquarters in Pawcatuck.
The cell features DavisStandard’s signature DSREV multipurpose elastomer extruder and a Uth gear pump to support processes ranging from hose, automotive seals, and architectural gaskets to in-line straining and pressure stabilisation applications.
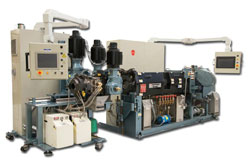
The firm says it has already conducted several trials since completing the installation earlier this year.
“Feedback from customers has been extremely positive. We offer various options for customer trials to address existing processing challenges, as well as future projects. This includes improving output rates, reducing extrudate temperatures, isolation of pressure for effective vacuum venting, and fine mesh straining of various materials,” according to Murphy.
The DSREV extruder in the technical centre is Davis-Standard’s flagship design. It is a preconfigured machine with feedscrew and head zone direct injection temperature control units, a compact base, and simplified cooling and wiring systems.
Other advantages include touch-screen controls, process data acquisition, and easily accessible machine components.
When coupled with the Uth gear pump, processors are able to isolate high pressure and achieve pressure stabilisation. The gear pump is equipped with a Uth two-roll feeder (TRF) for cold feeding or to be used as a stand-alone device for fine mesh straining.
Other gear pump advantages include improved filtration, reduced material retention time and small footprint to easily integrate into existing lines.
(PRA)Copyright (c) 2015 www.plasticsandrubberasia.com. All rights reserved.