Davis-Standard’s new dsX flex-film line for blown films
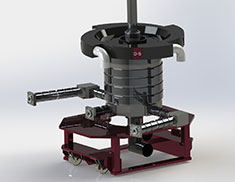
US extrusion machinery maker Davis-Standard has introduced its new dsX flex-film line for blown film applications. Offered with multiple extruder packages to support the blown film industry’s core market, this line is said to exemplify Davis-Standard’s trademark quality and performance at an affordable price. Using Davis-Standard engineering and components, the dsX flex-film supports equipment flexibility, options for greater processing efficiency, a fast delivery and responsive localised service. Target applications include films for laminating and converting, bag making shrink film, hood shrink film, collation film, multi-unit packaging films, roll stock and surface print films.
“With the dsX flex-film, Davis-Standard addresses the price, output, gauge uniformity and delivery requirements of a demanding blown film marketplace,” said Tom Kennedy, Vice President of Davis-Standard Blown Film. “We believe this value-added system strengthens the marketplace by offering a high-level option to processors who seek a cost-competitive US manufactured system.”
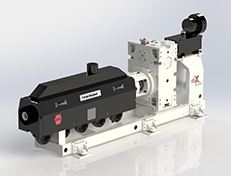
Available in 1,900 mm, 2,200 mm, and 2,500 mm sizes, the dsX flex-film is equipped with Davis-Standard extruders, feedscrews, gearboxes, air rings and dies. Dies are manufactured at the company’s Pawcatuck facility in the US for applications from one to nine layers. Most of the lines feature Davis-Standard’s compact Vertex die. This die supports high IBC cooling air exchange rates and output rates, while supporting streamlined polymer flow, low residence time, fast flushing and excellent thickness control.
Options for modifying equipment are based on application, film thickness and other processing factors. The UpJet air ring is an option for increased output capacity. Surface winders can be upgraded to include centre assist, gap winding, and reversible winding direction on a single winder with integrated nip, or back-to-back, or face-to-face winders with a secondary nip. Screw designs can be upgraded from X100 liner and Colmonoy 56 screw facings to more wear resistant X800 barrel liners and Colmonoy 83 screw flight facings.
The line supports speeds up to 180 m/minute and film thicknesses ranging from 20 to 180 microns. Advantages include die designs and what the company says is among the fastest formulation changes in the industry, options for multiple end-use applications, proven control systems and screw designs, flatter films with nip flattening enhancements, and US-centred support and service for a faster response and shorter lead times. This line can be delivered and installed in as little as six months from order to acceptance.
(PRA)Copyright (c) 2015 www.plasticsandrubberasia.com. All rights reserved.