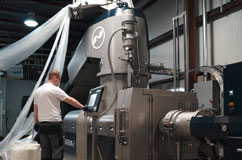
Erema North America, a subsidiary of Austria-based Erema Engineering Recycling says that due to high demand – especially in post consumer recycling – it will continue to expand in the US. Further to this,
To date, customers of Erema North America (ENA) have had a trial centre already covering some 1,000 sq m of floor space and three recycling systems for trials at their disposal at the company's North America base in Ipswich, Massachusetts. Now, the company plans to expand it to 2,400 sq m and install a new system. This means that in future the North American market will have four demonstration systems stationed in Ipswich for customer trials. The new system will be an INTAREMA 1108 TVEplus with Laserfilter, which will be joining the three existing plants: an INTAREMA 1108 T and INTAREMA 1108 TVEplus – each with Erema melt filter SW RTF, plus an INTAREMA 605 K. The expansion of the trial centre will get underway in March 2015 and its completion is scheduled for late summer 2015.
Mike Horrocks, ENA CEO, is proud to explain: "Our North America base represents a major Erema investment showing a strong commitment to North American customers. The facility is a valuable link to Erema's global headquarters in Austria, allowing customers easy access to EREMA equipment, technical support and vast reservoir of knowledge derived from decades of plastics recycling throughout the world."
Interest in the recycling of post consumer plastic waste is currently growing at a rapid pace in the US. The complex material mixtures, high degree of moisture and heavy contamination of the input materials call for reliable recycling systems. And this Erema says come in the form of its INTAREMA TVEplus system here which, thanks to the patented configuration of melt filtration with subsequent homogenisation upstream of extruder degassing, plus the efficient Laserfilter, enables high-quality end products.
The recently enhanced Laserfilter is particularly suitable for the processing of materials with a high degree of contaminants such as wood, paper, aluminium or copper and fulfils requirements which conventional melt filters cannot meet. With the new scraper geometry of the Laserfilter, customers now have additional efficiency benefits such as longer screen service life and reduced labour requirements thanks to long screen change intervals.
At the upcoming show in the US, NPE 2015, Erema will be exhibiting an INTAREMA 1108 TVEplus with Laserfilter at Booth no. W5673 on West Hall Level 2 at the International Plastics Showcase from 23-27 March 2015 in Orlando, Florida. Additionally, the enhanced, fully automatic edge trim system INTAREMA 605 K for the in-house recycling sector – which is likewise of significance for the US market – will also be demonstrated live.
The new, fully automatic processing system designed especially for the recycling of PE edge trim is the successor model of the previous KAG system which now features all the innovative technologies of the INTAREMA plant generation for further boosts to efficiency.
Erema says in-house recycling solutions for flexible plastic packaging are its core competency with some 2,000 of the over 4,000 systems it has sold around the world operate in this application field.
One of the key benefits of the enhanced INTAREMA K new system is the direct feeding of the endless edge trim via piping and cyclone which takes place automatically and offers maximum flexibility through possible combinations of cyclone, roller intake or conveyor belt, too. As a result, pre-cutting of the edge trim is not necessary. The fully automatic throughput adjustment to the actual amount of edge trim also ensures minimum labour requirements. This efficiency boost results in high-quality, clean pellets, up to 100% of which can be returned to the production process. INTAREMA K systems can thus be integrated not only in production lines but also installed externally as an offline system.
Furthermore, all the systems feature the new Counter Current core technology for improved material intake and higher output capacity, the Smart Start system for extremely easy operation and a top degree of automation plus enhanced ecoSAVE technology for even lower energy costs.
(PRA)