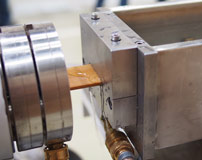
Rising market growth, above all in the US and in Asia by more than 5%, cost-efficient machinery concepts with high line speeds and output rates, and new applications are stimulating the global wood plastics composites (WPC) industry, which had slowed down slightly. This was the conclusion during the 10th Wood Plastic Composites Conference which, was organised by Applied Market Information (AMI), UK, and held in Vienna, near the main sponsor, battenfeld-cincinnati.
What is true for plastics processing in general is equally true for WPC processing: with up to 80%, the material costs take up the largest share in the overall production costs. With the aim of reducing these costs, a trend towards more co-extrusion applications is currently emerging in the industry; simultaneously, the demand is rising for low-cost fillers such as rice husks, mineral fillers or recycled fibres. At the same time, there is an increase in the demand for cost-efficient machinery concepts to reduce the overall costs, especially for the main product line of decking profiles, for concepts which offer high production and also ensure high-end product quality.
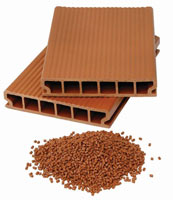
Here, hollow instead of solid profiles cater to the wish for material savings. The use of recycled materials to reduce material costs is as much an issue in the industry as is the use of biologically based and/or biodegradable materials.
Extrusion machinery maker battenfeld-cincinnati also focused its equipment demonstrations on these trend topics and showed, in cooperation with Beologic NV (Belgium), a complete line producing a hollow WPC profile consisting of PVC filled with 50% rice husks, and a second line, on which a WPC profile based on a biopolyester resin was made. The first line, equipped with a fiberEX 93-34 D parallel twin screw extruder tailor-made for WPC processing, reached an output of 380 kg/hour – a performance absolutely on a par with PVC profile production. The smaller line, equipped with an alpha 45 single screw extruder, reached an output of 40 kg/hour.
Sonja Kahr, the company’s WPC product manager, comments: “Today, we offer suitable solutions for all applications in the WPC industry and, above all, solutions tailored to fit every individual application. In our product portfolio, we have single screw extruders or conical twin screw extruders to produce small technical profiles, while for high outputs we offer parallel machine models which, with their 34D processing length, provide every possible option for direct addition of colorants, degassing and flexibility in plasticising. Both machine concepts can be optimally combined for co-extrusion applications.”
On both lines demonstrated at the AMI conference, materials from Beologic NV were processed, a company specialising in WPC compounds. PVC-rice compounds not only constitute a low-cost alternative to wood-plastic compounds, but rice husks have the vital advantage that they contain no lignin, and consequently the colour of the finished products fades much more slowly.
New applications for WPC were also displayed by the two companies Rehau and Plastic.WOOD directly beside the extrusion lines shown in production in battenfeld-cincinnati’s technical lab. While the German profile manufacturer Rehau presented a WPC sunshade system made of WPC in an aluminium frame, the Italian company Plastic.WOOD showed various injection-moulded products, such as tableware and chairs, made of WPC.
(PRA)