Also, download this story from the electronic issue here
India-based plastic woven fabric machinery maker Lohia Corp Ltd, the flagship company of the Lohia Group, has delivered accumulated plastic processing capacity of 2.5 million tonnes, with an installation base of 1,000 extrusion lines and 40,000 circular looms in over 75 countries to date.
2013 was a milestone year for Lohia Corp as it changed its name from Lohia Starlinger Limited, as a consequence of Austria-based Starlinger & Co. GmbH having divested its shareholding in the company. Exhibiting at the K2013 show in Germany, it thus, displayed a new logo. “The new logo and colours represent the renewed energy, passion for excellence and the italicised characters give the sense of forward motion and rooted dynamism,” explained P.C. Joshi, Director of Sales & Marketing.
Its journey in this business started off in 1981, when it was incorporated for the production of circular looms. It later expanded its range by including tape extrusion lines in 1984, with technology support from another leading European supplier.
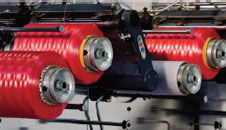
Today, as a global supplier of machinery, Lohia operates a manufacturing facility in Kanpur, and has local sales offices in the US, Brazil, UAE, Indonesia and Thailand, supported by sales agents in all the major global markets.
“We also have a fully resourced, in-house R&D facility in Kanpur, manned by qualified and experienced professionals. This enables us to deliver significant developments and innovations in tape extrusion, tape winding, circular weaving, conversion and spinning machinery for PP multifilament yarn. This is used for producing value added flexible packaging like woven sacks/bags, FIBC’s, tarpaulins, geotextiles, agro-textiles, ropes and twines for diverse applications,” explains Joshi.
Wide product range
Its extensive product range includes Lorex and duotec models of tape extrusion lines with melt capacity ranging from 260-900 kg/hour with 75-150 mm screw diameter and film widths of 600-2,000 mm with operating line speed up to 600 m/minute, depending upon the product requirement.
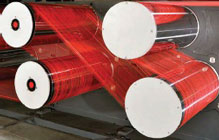
According to Joshi, the technology in the duotec series uses a unique double stretch process where the tapes undergo a pre-stretch before the final stretch.
“This process can be used to improve a mix of factors such as working speed, efficiency, increased process stability and tape properties.”
In its range of tape winders, Lohia offers a variety for high speed winding of flat and fibrillated tape.
“Our range of tape winder includes precision and step precision winders to suit a large variety of tape specification to produce perfect bobbins to deliver high efficiency during weaving and excellent fabric quality,” adds Joshi.
The latest generation autoroto winders are now considered a benchmark in the industry, claims Joshi. The autoroto winders with a speed up to 600 m/minute enable the automatic transfer of the tape from a full package to an empty tube, and are capable of producing equal length bobbins resulting in higher weaving efficiency and reduction in wastage and labour cost.
The circular looms from Lohia are designed for high performance weaving of heavy to light tubular/flat fabric from PP/HDPE tapes.
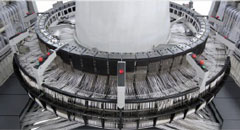
Said Joshi, “We offer these machines, from four to ten shuttle versions, to weave fabrics up to a width of 2.5 m (double-lay-flat) for covering the full range of the requirements. Special models for leno and ventilated fabrics are also available.”
He went on further to explain the latest nova series circular looms, adding that these produce “excellent weaving quality with higher working speed using electronic control system and tape tension control devices to produce nearly zero defect fabric.”
Converting machinery range
In the extrusion coating range, Lohia offers the coatec 1600/90 with 330 kg/hour melt capacity and line speed of 150 m/minute, suitable for flat fabric of 660-1,600 mm width and tubular fabric of 300- 750 mm width. It can coat both sides of tubular fabric in a single operation. The machine can be supplied with an optional equipment to laminate BOPP film. It produces coated fabric with what Lohia says is “precise film thickness and excellent adhesion”.
The range also includes the bcs 850/45 for producing bottom folded and sewn woven bags with speeds of up to 45 bags/minute.
Meanwhile, the valvomatic conversion line produces side-stitched valve bags for packaging of cement and pulverous/granular materials.
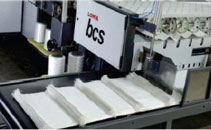
“We also offer special conversion machines for FIBC (jumbo bags) like fabric/belt cutting, baffle panel/profile/hole cutting, bag cleaning and hydraulic bale presses,” explains Joshi.
In this range, the company offers six-colour rollto- roll flexographic printing press soloprint for fine quality printing on tubular PP/HDPE woven fabric with speeds up to 150 m/minute. The machine is a joint effort of Lohia and Pelican Rotoflex Pvt. Ltd and is equipped with new generation electronics.
Other machinery include the Lofil range of spindraw- wind lines that are said to be compact and flexible machines for producing fully drawn high tenacity PP multifilament yarns. The machine has an extrusion capacity of 20/40 and 80 kg/hour and can produce a wide range of deniers from 600- 4,800 with winding speeds up to 1,500 m/minute. These yarns have applications in sewing thread for bag stitching, webbings and slings, braids and ropes as well as geotextiles.
Growing to meet customers’ demands
With its business growing by an average of 10% a year, Joshi credits the company’s success to improvements in its production systems that have helped its sales efforts.
“We have reduced the lead time by 15%, to allow for a better response time, even with customised machinery. In terms of technology, we are working on introducing more automation and increasing the speeds of our machines, with less wastage.”
As for the company’s focus, he explained, “Our exports constitute 25%-30% and we are positive about the future.”
At the upcoming Plastindia show, being held in Gandhinagar, Gujarat, from 5-10 February, Lohia at Hall 5/Booth M6, will showcase its latest nova series of weaving and converting machines.
For weaving, it will demonstrate the nova 6 and nova 8 and next generation valvomatic 35 models. The latter produces valved bags from tubular fabric for applications like the cement industry. Looms can produce small to wide width ranges for simple bags to FIBC bags; tarpaulins to geotextiles.
(PRA)