Catalysts add the “it” factor in material
Also, download this story from the electronic issue here
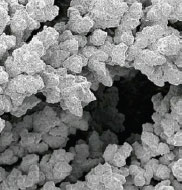
Ordinary, almost non-usable materials can be transformed into valuable materials with the help of essential elements called catalysts, reports Angelica Buan.
Catalysts are an axial component in many industrial processes helping to transform a raw material into functional products. While there is nothing magical about these substances, yet, they speed up chemical reactions without being consumed themselves, and enable material advances and diversity in applications of these materials.
According to research institute Ceresana’s global catalysts market outlook, catalysts are used in a wide range of applications from packaging and cosmetics, to agricultural fertilisers and oil refining. As stated, more than 80% of products in the chemical industry are made using catalytic processes.
Meanwhile, bioplastics are becoming a big application for catalysts, expected to drive an average annual growth rate of nearly 20% per year through 2021.
Because of their role in the manufacturing, catalysts remain a strong revenue earner in the chemicals sector. Ceresana, in its market reports, says that the global demand for catalysts will grow nearly 5% per year to US$20.6 billion in 2018 and reaching US$22 billion until 2021, with fast growth being earmarked in the Asia Pacific, Africa and Middle East regions.
Innovating with silver
One example of a catalyst widely used in the industry is silver. According to Washington-based non-profit association, The Silver Institute, silver is a vital catalyst in the production of two major industrial chemicals, ethylene oxide and formaldehyde, which are important ingredients in plastics, owing to silver’s unique chemical properties. Moreover, silver remains unaffected by the reaction, thus it is almost completely recovered after use.
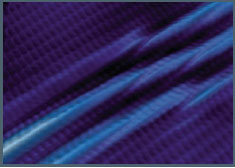
Silver is also the selected catalyst for creating borophene, a 2D sheet of boron, which the research team from the US Department of Energy's (DOE) Argonne National Laboratory, Northwestern University, and Stony Brook University have been developing.
Borophene, which is formed as electricallyconductive sheets of boron atoms, possesses metallic properties and is atomically thin, thus, scientists see its huge potential to rival graphene, a carbon-based substitute to silicon that is widely used in computer chips and electronics. Borophene can be utilised for a range of applications from electronics to photovoltaics.
The 2D material can be created inside an ultra-high vacuum chamber via a non-toxic technique called electron-beam evaporation. This technique vaporises a source material and then condenses a thin film on silver substrate.
Although borophene is still in the developing stage, and challenges in making it stable from chemical reactions when exposed to air are prompting for further research, scientists sees the material as a solution for making better electronic products in the future.
Clean-up act with earth oxide and silver salts
Scientists from Bengaluru’s Indian Institute of Science (IISc) have developed a reusable nano-composite catalyst using an inexpensive rare earth oxide called Ceria, a soft, silvery, ductile metal that easily oxidises in air and resembles the metal iron in its mechanical properties.
In its study, the IISc group found that ceria nanoflakes could be combined with silver bromide and silver phosphate to create the nanocomposite catalyst. All it takes for the catalyst to work is to be suspended in water and in sunlight, the researchers said.
The new material, when exposed to visible light, facilitates the formation of hydrogen peroxide, a strong oxidising agent, in water. The material uses the process of photocatalysis – the acceleration of a chemical reaction that takes place in light, in the presence of a catalyst. The hydrogen peroxide results in the breakdown of dyes and bacteria that commonly contaminate water ways.
A non-glycerol biodiesel
One major breakthrough using palladium as catalyst could address the glut of crude glycerol, a by-product of biodiesel production, which otherwise can be a challenge to tackle. Impurities, such as fatty acids, alcohol and salt, in crude glycerol make the substance of insignificant economic value. It also can be expensive to purify crude glycerol for use in food, pharmaceutical, or cosmetics applications.
Researchers from Illinois-based Northwestern University have developed a technique to generate biodiesel without the glycerol.
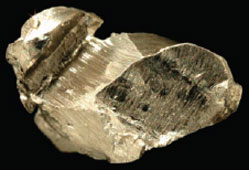
The process calls for a complementary action metal triflate and palladium catalysts. One catalyst breaks the carbon/oxygen bond, whilst the other catalyst hydrogenates the unsaturated product. That catalytic system aids to selectively break down triglyceride esters into organic compound carboxylic acids. The carboxylic acids can be converted to biodiesel, as well as propane and valuable C3-oxygenates, the scientists said, adding that while the technology is still in the development phase, it represents a positive potential for future biodiesel production.
Producing grease-to-green fuel
In a related development, a group of scientists from the National University of Singapore (NUS), Department of Chemical and Biomolecular Engineering, has hatched several environmentfriendly techniques to make biodiesel entirely from waste grease more cheaply and efficiently.
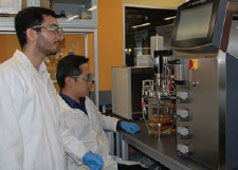
Waste grease is a combination of used grease, vegetable oils and animal fats that are usually discharged by homes and food and beverage outlets. The wastes that are accumulated in grease traps of buildings’ sewer systems are collected for disposal by contractors licensed by the NUS.
The research aims to simplify the process of waste grease-to-biodiesel in a single step. Traditionally, the high free fatty acid content in waste grease makes it unsuitable for biodiesel production due to technical issues and current catalysts and requires more than one step to process the waste grease.
The NUS team led by Associate Professor Li Zhi developed a one-step approach with specially engineered high-performance catalysts. Besides achieving impressive biodiesel conversion yields under optimal conditions, they can be easily separated from the biodiesel mixture at the end of the transformation process for multiple re-use with little deterioration in performance, Zhi said.
A biocatalyst method uses whole-cell Escherichia coli (E. coli) bacteria. It produced a 97% biodiesel conversion yield in 72 hours. Another method involves specially formulated magnetic nano-sized solid acid particles, which when combined with methanol efficiently catalyse waste grease, yielding up to 98% biodiesel in 24 hours.
Meanwhile, the third method is a recyclable magnetic nano-biocatalyst created using an enzyme derived from a fungus. The latter catalyses the waste grease containing methanol into biodiesel, giving a 99% biodiesel yield in 12 hours.
The scientists determined that among the three methods, the biocatalyst method shows the most potential, since the biocatalyst can be produced in large amounts at low costs.
Enabling sawdust-based fuel
In yet another way that catalysts are being used is how to repurpose sawdust for producing fuel. One technique devised by researchers at the Brusselsbased KU Leuven’s Centre for Surface Chemistry and Catalysis resulted into valuable chemicals for fuel and plastics.
With a unique process via its patent-pending biorefining technique and a chemical reactor, the researchers are able to convert the lignin in sawdust into aromatic chemicals and plant substance cellulose into hydrocarbon chains (but dropping the oxygen bonded to them) that can be used either as an additive in gasoline or as a component in plastics.
A catalyst aids to speed up the chemical reaction in the wood that is added to a reactor, to depolymerise the lignin material – a key substance for the gasoline – into the required chemicals. Likewise, solvent is added to extract the lignin out of the solid material; water or some biobased alcohols are also used in the process.
The researchers explained that with the right temperature and pressure, it takes about half a day to convert the cellulose in the wood shavings into saturated hydrocarbon chains, adding that the method allows them to make a petrochemical product using biomass, and thus, bridging the worlds of bioeconomics and petro chemistry.
Safer alternative for PET bottles
Antimony, a brittle, moderately hard metal with poor heat and electricity conduction ability, has been widely used in producing polyester-based products such as PET bottles.
For industrial use, antimony catalysts cause formation of insoluble particles and the grey discolouration in polyester.
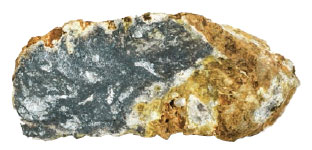
In the environment, antimony exposure can cause health risks. According to the US Environment Protection Agency (EPA), short-term exposure to the powder substance by inhalation in humans can cause skin, eye and respiratory problems. Hence, product manufacturers are looking for safer alternatives to this catalyst.
UK-based chemical technology company Catalytic Technologies says an antimony catalyst is not very active; using it requires around 250-300 ppm in the polymer, thus, likened to sand, antimony particles block filters and fouls production plants. This denotes more shutdown time. Additionally, antimony remains within the polymer after production and processing, and can leach to PET bottles.
Thus, the firm offers an antimony catalyst alternative in the form of a more active titanium-based catalyst.
Transforming environmentally-friendly ethanol
Creating a greener industrial chemical is a breakthrough role of catalysts. In a recent development, researchers from the Institute for Integrated Catalysis, Pacific Northwest National Laboratory and the Voiland School of Chemical Engineering and Bioengineering, Washington State University, with a grant from the US Department of Energy, have developed a mixed-oxides (zinc and zirconium) catalyst that can change biobased ethanol to isobutene or isobutylene used in bioplastics and biofuels.
Isobutene, a colourless gas, which is widely used in manufacturing a variety of products from plastic bottles to rubber tyres, is produced from crude oil. The researchers believe that the new catalyst can significantly help wean the industry from relying on fossil fuel-based chemical. It also enables for lower production costs and faster production times with a one-step production process since it requires the presence of water, thus, allowing producers to use diluted and cheaper bio-ethanol rather than having to purify it first.
Bad air into sustainable plastics
US biotechnology company Newlight Technologies, known for its carbon-negative AirCarbon innovation, has successfully harnessed the benefits from methanebased carbon emissions (60% carbon and hydrogen) combined with air (40% oxygen) and a high-yield biocatalyst. The result is a high performance long chain thermoplastic polymer that is cost competitive with fossil fuel-based polymers, and is suitable for use in extrusion, blown film, cast film, thermoforming, fibre spinning, and injection moulding applications.
AirCarbon is a PHAbased thermoplastic made from greenhouse gas that is used and is being developed for use in a wide range of products, including films, caps and closures, furniture, electronics accessories, bottles and other applications.
Newlight’s AirCarbon PHA deal with Texasheadquartered marketer and distributor of chemicals, Vinmar International, signals the launch of the PHA-based polymer to world-scale volumes.
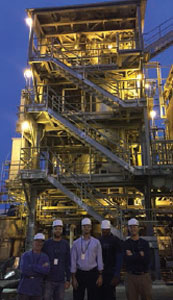
Enzymes for sugary chemicals
Hydrocarbon chemicals present in ice cream and other household items can be produced with a carboxylic acid reductase biocatalyst discovered by a team of Manchester University (MU) scientists. The enzyme enables the conversion of fatty acids into fuels and chemical commodities. This breakthrough could lead to the long-term replacement of fossil-fuel obtained chemicals, they said.
Through synthetic biology, an area of biological research and technology that combines science and engineering, the MU scientists who worked alongside Finland’s University of Turku scientists for this study, were able to commandeer naturally existing fatty acids for the production of ready-to-use fuel and household chemicals.
The breakthrough allows researchers to further explore how to create renewable energy from sustainable sources, and the advance could lead to more innovative ways of sourcing fuel from natural resources.
(PRA)Copyright (c) 2016 www.plasticsandrubberasia.com. All rights reserved.