Staying with bags through thick and thin
Also, download this story from the electronic issue here
In terms of sustaining transitions in materials advancements, weathering the toughest regulations, and yielding to safety standards, we can say that plastic bags have “been there, done that”.
Meanwhile, the European Bioplastics (EUBP), the association representing the bioplastics industry in Europe, welcomes the approval of the French implementation decree on single-use plastic bags, which was published by the French Ministry of Ecology, Sustainable Development and Energy recently. In August last year, France introduced a ban on single-use plastic bags as part of the new law . An implementation decree setting out the requirements and conditions in greater detail has now been approved and will come into effect on 1 July 2016. The decree applies to single-use carrier bags below a thickness of 50 microns, which will have to meet the requirements of the French standard for home composting and feature a biobased content of at least 30%. The minimum biobased content will increase progressively to 40% in 2018, 50% in 2020, and 60% in 2025. Appropriate bioplastics materials have been readily available on the market for quite some time, and manufacturers are eagerly waiting in the wings, says the association. It also adds that the decree will help to revive economic activity for French plastics converters, as 90% of fruit and vegetable bags are currently being imported.
Reduction of consumption of disposable bags has been practiced in many countries mainly for reason of environmental protection. Nevertheless, countries differ in tackling this problem, depending on their respective amount of per capita consumption, the number of reuses, as well as the quality of the different waste managements and disposal and recycling systems. As an example, Europe has an amendment of the packaging directive (94/62/EG) that commits EU member states to precise actions.
Using bioplastics for bags is considered as a remedy as far as bag bans and taxes levied on polyethylene (PE) bags are concerned. Plastics made of renewable raw materials, including potato starch, soybean oil and citrus oil, have gained recognition as a viable alternative to fuelbased plastics. Nonetheless, composting and degradability issues are still being deliberated on, and thus, bioplastic bags are not considered as a be-all solution despite the advantages they are claimed to provide.
But nothing can bring the good ol’ plastic bag down, being the most common carry-all for shopping for more than four decades now since it was first introduced at retail in mid-1970s. Its versatility enables it to be adaptable for a variety of needs.
Thin is in
Ultrathin-wall plastic bags, carrier bags with enhanced carrying handle, valve bags, FIBC, standup pouches, disposable sachets: the list of different types of bags grows bigger and bigger. The new study of the market research institute Ceresana expects that the worldwide demand for bags and sacks made of PE, of other plastics, of woven plastic strips, as well as of paper, altogether will grow until 2022 to about nearly 38 million tonnes.
PE, especially LLDPE, is the most-commonly used material here. However, individual materials may account for highly different market shares in various applications.
Thin wall packaging’s rising popularity has created significant opportunities for growth and developments in the rigid plastics market. In a new report from industry consultants, AMI Consulting, states that with the consumption of 3.1 million tonnes of polymers in 2015, thin wall packaging is a large and relatively stable market in Europe.
Nonetheless, the search for higher margins and market positioning is causing the industry to focus on improvements in material and process engineering. The past few years have been particularly productive for the industry and advances in process technology synergistic with polymer science have enabled changes that have facilitated the emergence of new applications.
Alongside these aforesaid changes have been the changes in the supply chain. The industry actively consolidated and the leaders attempted to redefine and restructure their businesses to maximise technical competence and to create a stronger negotiation platform, says AMI. This has driven the disposal of non-strategic business units and targeted investments. There has been significant site rationalisation, exchange, production relocation and acquisition amongst the leaders.
In 2015, the top ten converters of thin wall packaging in EU28+3 accounted for 43% of the market. Outside the leader base, the supply in Europe remains relatively fragmented and more consolidation is expected.
Retailers remain ever stronger customers of thin wall packaging, driving improved quality standards of value products. Brand owners employ a range of packaging solutions to capture discrete marketing opportunities, using multiple formats. This enables brand owners to monitor and compare costs, alter the packaging mix and spread risk. Over the next five years those suppliers with a focused business strategy are expected to continue to strengthen their market position.
Need for strong bags
While thin films are showing strong market foothold, thick films are not being left behind. There are a number of industries that cannot do away with plastic bags.
Moreover, the heavy duty and the so-called industry sacks have demand in the construction sector, in China and Brazil, according to a report by Ceresana.
Specifically in Asia, more than in Europe, heavy duty plastic bags are used for cement packaging. Paper bags, however, are more preferred in animal feed or construction materials sectors, while PE films are also gaining further market shares.
Stand-up pouches making their mark
Plastic tops in the food packaging trend, compared to metal cans or glass jars. Ready-made meals, a hallmark for rising urbanisation in many economies are benefiting from stand-up pouches (SUPs) that come with value-added features, such as being microwave-ready and biodegradable.
According to a report from MarketsandMarkets, SUPs attract wider usage because of the adaptability for varied applications, and hence, they have the potential to reach a market value of US$33.4 billion by 2020. SUPs also consume less storage capacity and have the ability to stand up on shelves, thus adding to the product's visibility.
This packaging solution is designed with excellent barrier properties and available with attached accessories like resealable properties, nozzles and zip locks, which are useful for end-users.
They are widely used in an array of applications, with the food and beverage sector being the main one as they are made of highly sterilised materials. This enables the products inside the pouches to remain fresh without getting contaminated for a longer period.
Other sectors include the healthcare, personal & homecare, nonfood and others such as fertilisers, paints, and coatings.
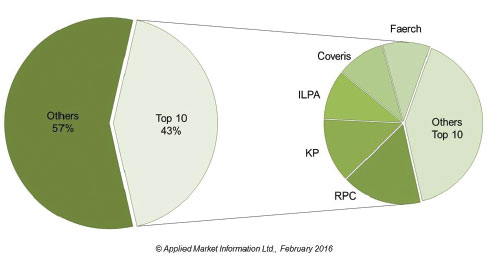
(PRA)
Copyright (c) 2016 www.plasticsandrubberasia.com. All rights reserved.