Busting toxic chemicals in food-contact packaging
Also, download this story from the electronic issue here
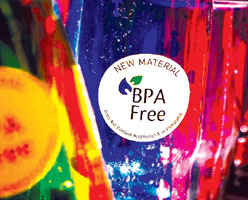
Just when we thought that our neatly packaged food and drinks were safe from contaminants, it has now been made aware to us that the chemicals used in the making of packaging materials could also be a conduit to health risks, says Angelica Buan in this article. Meanwhile, two researchers in New Zealand have developed a sensor that could detect notorious phthalates.
Chemicals have earned the notoriety of being, in many instances, toxic. It may be true for substances that require care and precision in handling. However, chemicals are useful components in materials that we practically use in our daily lives. This is more so in plastics packaging, where chemicals are part of the manufacturing process.
The worst enemy of packaged food and drinks is contamination by not only organisms causing food spoilage, but also chemicals inherently used for producing packaging materials and to enhance functionality of materials. These can also potentially contaminate the products on contact, studies say.
Health risks under the wraps
Chemicals in materials used for packaging are found to influence the health of consumers in varying degrees. A study, published in the journal Food Additives and Contaminants, discovered that around 175 legally-used chemicals found in food packaging are linked to cancer, fertility, genital malformations and birth defects. The surprising news is that these chemical-containing food packaging complies with the criteria of Substances of Very High Concern (SVHC), set by the EU's Registration, Evaluation, Authorisation and Restriction of Chemicals (REACH) body.
Chemical contamination in packaging can occur if it is in direct contact with food. There are instances also that chemical migration occurs for secondary and tertiary packaging, as well as during the production process.
Early this year, the US Food and Drug Administration (FDA) scratched off three greaseresistant perflourinated chemicals used in food packaging materials.
The Environmental Working Group (EWG), reacted to this stating that the ban undercuts a sound solution to the problem, adding “that there are yet a number of similar FDA-authorised chemicals used in packaging materials.”
Other meaningful actions, such as removing Bisphenol A (BPA), another industrial chemical used in the production of food-contact packaging that is linked to a host of health risks such as hormone disruption and cancer, has not alleviated safety concerns according to some reports. The latter point out that BPA substitutes such as Bisphenol F (BPF) and Bisphenol S (BPS) present different risks, one of which is the potential effect to brain development in infants, as cited in a research by the University of Calgary in 2015.
As well, there are certain chemicals in packaging that can migrate into the packaged product. Yet, the debate weighs on how much of the chemicals that can be detected.
A recently conducted second phase of the Australian Total Diet Study by the Food Standards Australia New Zealand (FSANZ) spotted low levels of chemicals in food and beverage items that had leached from plastic packaging.
FSANZ tested samples for about 30 chemicals that included BPA, epoxidised soy bean oil (ESBO), perfluorinated compounds and phthalates, as well as printing inks, for migration into food from packaging.
The tests showed" no detections of phthalates, perfluorinated compounds, semicarbazide, acrylonitrile or vinyl chloride in food samples". What this means, said FSANZ, is that the amount of the chemicals migrating into the product may pose no safety concerns.
Recalls of products
Nevertheless, potential migration of chemicals has resulted in several food products being recalled. French bottled water manufacturer Perrier pulled out its water products from the US market in 2009 after a small sample of the water bottles tested positive for benzene, which is a crude oil component and is believed to be carcinogenic.
Likewise, cereal maker Kellogg recalled 28 million boxes of cereals in 2010 after reports of an off-putting odour from the product and packaging that ranged from waxy to metallic, which the company said could be due to the presence of hydrocarbons, including methyl naphthalene in the wax and film used in the packaging.
Even packaged pet foods did not pass the scrutiny for chemicals. A batch of cat treats in plastic stand-up pouches produced by Blue Buffalo in the US was pulled off the shelves when FDA detected the presence of Propylene Glycol (PG), a chemical used for direct and indirect food applications.
While not categorised as carcinogenic, PG could potentially increase the acidity level in the body of animals. Cats that ingest high dosages of PG may display frequent urination and thirst, amongst other reactions.
Precursor for innovation to detect DEHP
One of the most headlined incidences of chemical contamination is the Taiwan food and beverage scandal in 2011, which involved the use of industrial plasticiser DEHP in dangerous amounts in a range of Taiwan-made products. Some 965 products were found contaminated with the plasticiser, of which 206 were exported to 22 countries.
The incident that took place unleashed the perils of adding chemicals not only in food products but also in food-contact packaging.
Moreover, it is also a backstory for a promising innovation that detects traces of DEHP.
New Zealand’s Massey University’s Dr Subhas Chandra Mukhopadhyay, Professor of Sensing Technology, School of Engineering and Advanced Technology, and Dr Asif Iqbal Zia have developed a sensor that can detect phthalates.
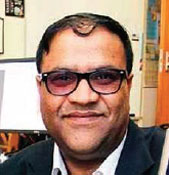
“Illegitimate addition of DEHP as a clouding agent in beverages has been a controversial issue in Taiwan in 2011; and for which, the country faced huge economic loss, when it had to recall all the exported beverages for testing as required by the buyers. The testing lasted for months due to the non-availability of a reliable rapid testing system, in addition to the enormous costs of the testing,” Dr Zia said in the email interview with PRA.
Referring to the Rapid Phthalate Sensor, the 2.5 by 2.5 mm device is made using MEMS technology that involves photoresist coating, ultraviolet light exposed interdigital pattern transfer, plasma etching, gold deposition by DC magnetron sputtering by Argon gas plasma and lift-off.
The sensor is fabricated on a single crystal 4-inch rigid silicon substrate (525 microns thick) over native silicon dioxide with patterned gold electrodes. A gold layer of 500 nm is sputtered on top of the 20 nm chromium seed layer to provide defect-free adhesion of thin film electrodes on the silicon substrate. Gold is the most preferred electrode material for sensing applications due to its excellent physiochemical stability, bio-affinity, low electrical resistivity and minimal oxidation, according to the engineers.
How this sensor catches those inconspicuous phthalates in contaminated beverage, as a sample, is via a selective coating developed based on the molecular imprinting technique.
“The sensor is coated with a selective polymer coating that captures the phthalate molecules by creating hydrogen bonds with them and binds them on the sensing surface,” Zia explained.
Molecular imprinted polymers (MIP) are specially designed polymer materials owning valuable target molecules recognition sites, privileged by unique advantages like high selectivity, physiochemical stability, robustness, longer shelf life, reusability and specific recognition of analytical and structurallyrelated compounds.
“This molecular recognition selectivity has proven to be an attractive predominant advantage over biological receptors and antibodies for a more number of target molecule capturing sites,” he adds.
A special polymer was developed that owned molecular imprints of phthalate molecule or in other words, the polymer contains phthalate molecule recognition sites on the polymer surface.
MIP for phthalates is synthesised by suspension polymerisation using methacrylamide as a functional monomer attaching itself to phthalate molecule via hydrogen bonds. N,N-methlene-bis-acrylamide is used as crosslinker for polymerisation reaction and ammonium persulphate, as an initiator for synthesis of the polymer.
Additionally, the sensor can also detect other structurally related compounds used in the plastic industry as additives.
“We have also done some work on DINP. The sensitive and selective molecularly imprinted polymer coating could be tailored with respect to the target molecule,” said Zia.
Protection from the industry to consumers and the environment
While the sensors are not novel technologies, the Rapid Phthalate Sensor, which operates on the Electrochemical Impedance Spectroscopy technique, provides benefits encompassing the industry, consumer and the environment.
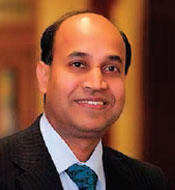
Zia commented: “Almost all contemporary analytical techniques used to detect phthalates are highly sensitive due to the requirement of measurement of trace levels of phthalates present in food and beverage samples. However, these are time consuming, expensive, complicated, produce laboratory waste, need the expertise of highly trained professionals, in addition to submission of samples to laboratories worth millions of dollars.”
Therefore, he says that it is necessary to have a rapid assay, which may detect the quantity of phthalates present in food and beverages that may be ingested, this being considered as a primary means of human phthalate exposure amidst the extensive use of plastics in daily lives.
He goes on to say, “The requirement of instant screening of a batch of products manufactured at an industrial set-up still requires a simple test device that only requires minimal training and does not involve bulky and expensive support electronics. The objective of our research was to develop a lowcost real time testing system that could readily be installed in an industrial set-up.”
At the time of press, Mukhopadhyay said that lab prototypes have already been developed and tested but commercialisation of the technology still requires further R&D as well as funding to come up with a more robust version of the developed technology. “While there are already a few companies interested in this technology, most of them prefer a system that can be commercialised without any further research,” he added.
Yet to be patented, the senor technology aims to simplify defence from chemicals that have become crucial components in our changing lifestyle.
When asked how the sensor could be used in the industrial level, Zia replied, “The sensor could be integrated with the quality control of food and beverage products industries that use PET bottles and plastics packaging. On the other hand, this technology could be developed as a commercial hand-held device that could be used by a regular consumer to ensure that the phthalate content of the plastic packageddrink is lower in concentration than the Minimal Risk Level (MRL) limit of 8.0 μg/L as set by WHO and ATSDR (Agency for Toxic Substances & Disease Registry) of the US.”
The sensor could also become a helpful precursor for the plastics industry to tap safer alternatives to phthalates, Zia and Mukhopadhyay opined. “This technology could guide the plastic industry to find health-safe replacements for phthalates in order to save the human generations from the carcinogenic and teratogenic effects of these synthetic compounds.”
Furthermore, the engineers said that the benefit of this ongoing technology development extends to protecting the environment.
“Both consumers and the environment can be protected by way of providing awareness about the health hazards involved in the use of phthalates in plastic products. These efforts could help stop further penetration of ubiquitous phthalates into our ecosystem,” the researchers noted.
(PRA)Copyright (c) 2016 www.plasticsandrubberasia.com. All rights reserved.