CFRP components with shorter cycle times using wet moulding
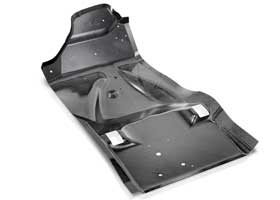
German machinery maker KraussMaffei has innovated a solution for manufacturing fibre-reinforced plastic components based on both thermoset and thermoplastic matrix systems known as wet moulding, which it says is a cost-effective alternative to the HP-RTM (high-pressure RTM) process.
Development focuses primarily on creating processes and systems that can be used to manufacture lightweight components in large series production, for which there is great demand in vehicle construction. The company is to exhibit this at the JEC World show in Paris, France.
Wet moulding or wet pressing, in comparison to classic RTM processes (resin transfer moulding) like HP-RTM (high-pressure RTM) and C-RTM (compression RTM), is characterised by a simpler process chain in which the preform process is omitted completely. For this reason, wet moulding is a cost-effective alternative for manufacturing new lightweight components in vehicle manufacturing.
During the wet moulding process, a mixing head applies the resin (usually epoxy resin) onto the flat-lying semi-finished fibre product in continuous strips. The fibre product is then passed on to the mould, where it is compression moulded. This process has two decisive advantages. It saves valuable cycle time, because the resin can be applied to one component at the same time that the other is curing in the mould. The system can also be more reactive. Charging is no longer necessary in the heated mould, in which a reaction cannot yet occur. These two factors save time, leading to shorter cycle times. It is also possible to use recycled fibre material. This makes wet moulding an excellent option for industrial processing of recycled fibres in the RTM process.
The lines feature a high degree of automation, ensuring short cycle times and high numbers of pieces. At JEC World in Paris, KraussMaffei is presenting current application examples from the mass production of the new 7 series BMW and the i8 electric car.
(PRA)Copyright (c) 2016 www.plasticsandrubberasia.com. All rights reserved.