German firm Bomat, which specialises in exhaust heat exchangers and a specialist for industrial waste heating solutions , produced the first of its kind flue and exhaust gas heat exchanger made with Celenese’s Fortron polyphenylene sulfide (PPS) components.
At the K2013 show in Dusseldorf in October last year, specialty materials firm Celanese showcased Bomat’s heat exchanger, which is made unique with the high-temperature resistant Fortron PPS that is used in both the complex water-carrying housing components (water distributor) and the side panels, while the heat exchange tubes are ceramic. This ingenious material combination enabled Bomat to produce a first-of-kind heat exchanger without any metal in the exhaust gas section.
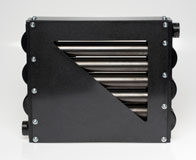
Eliminating the high-alloy steels and aluminum from the exhaust gas section prevents the acidic flue gas condensate from dissolving any metal ions, especially heavy metal ions such as nickel and chromium. In every heating system, the flue gas condensate is discharged via the conventional waste water system, but this new technology prevents aluminum or heavy metal ions from entering the water cycle and damaging the environment. This means operators of heating systems and cogeneration heat and power plants (CHP) can obtain significantly more energy from their fuel and save natural resources, as well as reduce the environmental impact by decreasing the release of heavy metals.
Celanese was involved in the development of the new Bomat Profitherm heat exchanger from the beginning. Early involvement, which helped Bomat avoid unnecessary development loops and meet its ambitious timeline, focused on component design, supplemented by structure simulation and extensive calculation of mold filling, fiber alignment and weldline positions. In addition, extensive material and application knowledge, and technical support were an absolute pre-requisite.
As the material of choice for the innovative Bomat Profitherm heat exchanger, Fortron PPS provides:
Excellent resistance to the acidic flue gas condensates that arise in oil and gas burners and CHP
- Very good resistance to heating oil and fuel gases
- Outstanding heat distortion temperature
- High strength and stiffness
- Improves production of parts to the precision specified
- Coefficient of linear thermal expansion similar to that of steel that, in combination with metal add-on pieces, results in lower thermal stress and forces acting on the components
- Enables ready-to-use parts: Die-cut without any further reworking
- More favorable overall energy balance than with customary metal cast parts; no mechanical reworking or corrosion protection required
- Considerably lower component weights that simplify storage, transport and assembly
(PRA)