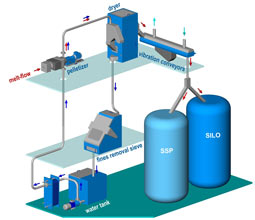
An integrated system that uses the thermal energy of the molten polymer in PET pelletising for subsequent crystallisation eliminates problems caused by the agglomeration of amorphous material and substantially reduces energy costs for compounding or recycling, according to Germany-based Nordson BKG.
The CrystallCut patented process avoids the need to cool PET after pelletising and then reheat it for crystallisation. As an integrated network that incorporates underwater pelletising, drying, and crystallising, it is designed for precise control of material temperatures throughout the process, preventing production and quality problems caused by insufficient crystallisation and excess levels of amorphous material. The energy efficiency of the CrystallCut system can save more than EUR 3,000,000 in annual energy costs for a typical PET resin plant and nearly EUR 200,000 for an extrusion line recycling PET bottle flakes, according to examples cited by Nordson BKG based on actual commercial installations.
In the CrystallCut system, the hot PET granulate produced by the face cutter of the underwater pelletiser is transported rapidly to the pellet dryer in hot water (up to 95 °C) through closed conveying pipes, where pellet cooling and solidifying takes place. This conveying medium and the short distance between die head and dryer are keys to conserving the heat from melt processing. The pellets are at a temperature in the 150 to 160 °C range when they exit the dryer onto a vibrating conveyor. This keeps the pellets in constant motion, generates a uniform distribution of thermal energy, and prevents pellets from sticking together. At the completion of the process, the pellets have a temperature of approximately 180 °C, have achieved up to 40% crystallinity, and may be transferred directly to solid state polycondensation (SSP).
In addition to saving energy costs and preventing amorphous PET clumping, the CrystallCut system yields an almost dust-free product and increases bulk density by 8% in comparison with a conventional process.
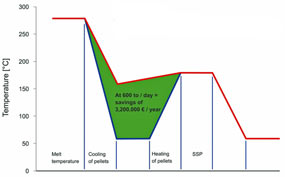
Assuming an average energy cost of 12 cents/kWh, Nordson estimates that the CrystallCut system yields energy savings of up to 125 kWh or EUR15 per tonne of PET in a modern PET polymerisation plant. Since such a plant can achieve a production capacity of 600 tonnes per day, these savings amount to EUR9,000 daily and EUR3,200,000 per year. This represents an annual energy saving of more than 26 gigawatt hours, or 26,000 megawatt hours.
Another example cited by Nordson is that of an extrusion line, which recycles PET bottle flakes at a rate of 1,500 kg/hour. The savings achievable with the CrystallCut system exceed 180 kWh, or more than 1.4 cents/kg. In a 365/24 operation this equates to EUR190,000 per year.
(PRA)