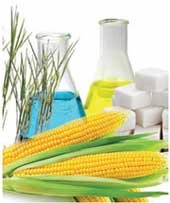
Relatively at a nascent stage, bioplastics are already trailing close behind conventional oilbased plastic products in terms of demand. The bioplastics market is projected to unleash a growth of 20% a year in Europe and in Asia Pacific, it is expected to reach a market value of US$167 million by 2018, says Angelica Buan in this report.
Previously an unpopular traditional plastic option due to its higher cost and alleged threat to food source, the global wide pressure towards sustainability and environment protection has eclipsed these ostensible limitations of bioplastics.
The new breed of organic resins are currently generating public interest for their “green” value, with biobased plastics expected to cut down consumption of petroleum for plastic by 10-15% by 2018, according to Transparency Market Research.
Conquering limitations
Some of the weak points attributed to bioplastics to enable wider acceptance include what Washington-headquartered Institute for Local Self-Reliance (ILSR) has said regarding the use of genetically modified organisms (GMOs) as feedstocks, a need to develop composting programmes and infrastructure as well as contamination of recycling systems.
Currently, there have been major developments that address some of the above restraints. The US-based Bioplastic Feedstock Alliance (BFA), an organisation formed in November last year by eight major consumer products firms (Coca-Cola, Danone, Ford, H.J. Heinz, Nestle, Nike, Procter & Gamble and Unilever) together with the World Wildlife Fund (WWF), are pushing for responsible selection of feedstocks for bioplastics, such as sugar cane, corn, bulrush and switchgrass.
The organisation aims at assessing the potential impact of developing these first generation feedstocks on land use, food security and biodiversity.
Meanwhile, Belgium-headquartered PRO Europe (Packaging Recovery Organisation Europe) says there are grey areas in the use of bioplastics. “Consumers are confused with the different labels describing packaging as biodegradable, home compostable, compostable and degradable. They rate them as favourable but mostly ignore the exact meanings, whether and how they should sort them and which sustainable waste management options to treat them,” it has stated.
US bioplastic resin supplier Bioplastics International’s President/CEO, Garrett Valentino, in an email interview with PRA, shared that while bioplastics have many benefits over petroleum-based plastics, they are also fraught with limitations.
"They cost substantially higher than petroleum resins and also disrupt the recycling stream. Furthermore, they are not a compatible choice for products that require exposure to high heat, extreme cold, or a prolonged shelf life. Plus, bioplastics may contain liquids that may have an issue with oxygen permeability, evaporation and oxidation," said Valentino.
Fixing the recycling woe
However, Valentino says that bioplastics also have plus points. "They can be composted, biodegraded in a landfill or incinerated. When petroleum-based plastics are incinerated, as in the medical industry, dioxins are released into the environment, unlike bioplastics that incinerate completely clean."
The issue of recycling bioplastics such as polylactide (PLA) is a point of concern.
Lee Chee Kiong, Sales Director Asia, Sorting Division, S+S Inspection Asia, told PRA that the company offers several sorting systems, including a near infrared (NIR) spectroscope sensor for sorting bioplastic materials from the PET bottle stream, such as PLA, PVC or PET-G labels.
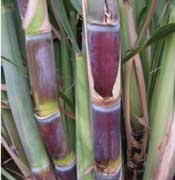
"When we look at the separation of plastics beverage containers in a recycling process, there are basically two elements to it: separation at the full bottle stage (before the bottles are granulated into flakes). This is a lower investment approach for recyclers as the sizes (though compacted into flat shape) are larger than flakes and do not require a very high resolution scanning sensor as in the case of scanning very small flakes. The second is the final separation at the flakes stage (before packaging of the flakes into bags or transfer to another machine). A flake sorting process is required especially when the processors are dealing with high quality flakes or further processing into food grade packaging, or bottle-to-bottle grade rPET resin."
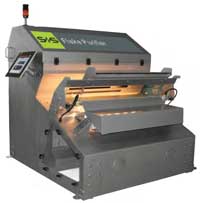
For the NIR sensors, Lee says that the working principle is anchored on the reflection of illumination lights off the surface of particles. Hence, the NIR sensor will be able to detect bottles, labels on the bottles and flakes. "Labels are more complicated. As labels are very light and flexible, they cannot be effectively ejected by the automatic air valves on the sorting systems. Hence, most of the PET bottle washing plants have a mechanical stage to remove the labels from the PET bottles, before the “stripped naked” bottles are sent to an automatic bottle sorting system for separation of the bottles," explained Lee.
He also says that for multi-layer bottles, just like labels, the inner layer (EVOH or PA) is typically very thin and flexible and light. "As such, while the NIR sensor on the flakes sorting system can detect these inner layers without any problem, it is the separation by eject air valves that is the 'bottle-neck'. We recommend air separation systems to remove the inner layer after the bottles are crushed into flakes."
Hunt for better solutions
US market researcher Freedonia estimates that world demand for biobased-resins is growing at 19% a year and will reach 960,000 tonnes to 2017. This projection indicates that bioplastics have established a grip, especially in commercial markets and applications, according to the study.
Moves to phase out the use of plastic bags, enforced recently in some countries in Europe, further highlight the value of bioplastics.
Recently, the European Parliament has moved to prohibit the use of lightweight plastic bags (maximum thickness of below 50 microns or 0.05 mm) by 2020, ergo, approving the EU Commission’s waste management proposal.
The premise is that these thin plastic bags, mostly used as grocery bags, accumulate in the environment and clog the water ways.
Meanwhile, Arizona-based Bioplastics International offers a fresh solution, which could change the way bioplastics are viewed.
According to Valentino, the company, in partnership with a US manufacturer, is offering a “US Governmentcertified biodegradable” material – a pure organic additive that will work for all plastics, including PE, PP, PS, PVC, PET, PC, and even rubber. “This is the finest organic additive available in the market that is approved for food contact by the FDA and EU and is also FTC and REACHcompliant. This type of technology that is duly validated and tested is fairly new to the polymer market.”
He explained that the specially formulated additive makes polymers biodegradable without sacrificing the beneficial properties of the primary polymer, including recyclability.
“To create the biodegradable material, the manufacturer adds specific renewable nutrients and organic compounds into the polymer which, once discarded, allows microbial action to colonise in and around the plastic and completely metabolise the polymer. The end result is: inert humus (biomass) and biogas (anaerobic) or CO2 (aerobic). Products with 1% of this organic additive are biodegradable in anaerobic (no oxygen, no light), and aerobic (with oxygen) environments, which include common landfills. In order for plastics to properly break down, tiny microscopic organisms must find the discarded products an irresistible morsel, and begin consuming it bite by bite. Only then, can the item be broken down entirely,” he said.
“Traditional plastics are unattractive to microbes and therefore inedible. This organic additive will allow plastic products to biodegrade at a rate of 33% every ten months, with some plastics at a faster rate. No additives will create compostable plastics,” he added.
Valentino assured that plastics made with the firm’s organic additives are completely recyclable and can also comingle with existing plastics recycling streams. “This assertion is backed by scientific data as well as affirmation from independent recyclers,” he added.
Despite the organic additive’s promising properties, Valentino said that it may not solve all plastic issues. “If all the plastic products on earth would soon completely biodegrade safely in landfills the world and our environment would be a much better place for us,” he concluded.
(PRA)