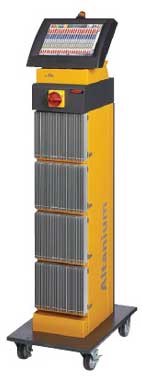
The medical market is driven by complex applications that require reliable, repeatable moulding solutions. For medical moulders who must quickly and consistently manufacture high quality parts using difficultto- mould resins, as well as complex tooling that hold extreme tolerances, this leaves little room for error.
An ageing population and increasing demand for disposable medical devices present significant short and long-term opportunities for medical manufacturers of plastics components. But while medical moulding is a growing market, it is also a challenging industry characterised by lengthy product development processes, many clinical trials, demanding record keeping practices and greater regulatory oversight than other industries. These increased regulations are for the purpose of driving part quality, process stability and risk mitigation as a means to eliminate part failure and possible injury or death of patients. Maintaining the most accurate and repeatable temperature control in a moulding operation is key to producing high quality, highly complex medical parts consistently and reliably.
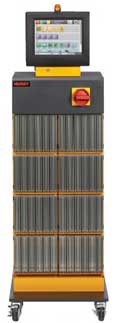
Husky Injection Molding System’s newly introduced Altanium Delta3 hot runner controller is specifically designed to provide solutions to help comply with the medical industry’s stringent requirements. Accurate and repeatable temperature control with minimised cavity-to-cavity and shot-to-shot variability is a key aspect of part quality and process stability. Altanium Delta3 delivers on this through the deployment of Active Reasoning Technology, also known as ART. Requiring no intervention by the user, ART is able to generate a parameter set to precisely fit each zone’s unique thermal response characteristics. Once the optimal control algorithm has been calculated, it utilises a modulation method that delivers a rapid, uniform flow of power, minimising the amount of time that energy is not being delivered to heaters. Using a technique known as oversampling, the integrity of the temperature signal is preserved, allowing the algorithm to execute power changes based on the most accurate data. Additionally, isolated thermocouple inputs assure the reliability of incoming temperature measurement by providing a high degree of immunity to electrical noise. This eliminates the potential risk associated with electromagnetic interference emitted by the servo motor systems found on all electric moulding machines. The outcome is the industry’s most accurate and repeatable temperature control, regardless of the hot runner system or processing environment.
There are times when it is necessary for the controller to stop heating the mould or circumstances that require the machine to stop cycling. If this occurs, material could degrade, resulting in bad parts entering into the downstream process. Altanium Delta3 provides the following interlocks to mitigate this risk:
- At-Temperature Output – Inhibits injection until the mould is at processing temperature
- PCM Output – Stops the injection moulding machine from cycling if the controller stops heating the mould
- Remote Standby Input – Brings the processing setpoint to a lower temperature if the machine stops cycling
This connectivity enables the machine and controller to make informed decisions, based on the state of the other, which provides assurance against defective parts reaching end users.
Other aspects of medical manufacturing include rigid documentation of the process, including any changes or deviations from the original parameters used during the mould qualification. Altanium Delta3 ensures these parameters are retained by permanently storing them in a set-up file that is available for recall at the press of a button. To further enhance this capability, there is an optional remote load function that allows the corresponding mould set-up in the controller to be loaded from the injection moulding machine. The system also supports a wide range of file types for storing and managing critical documentation right from the controller’s screen. These can be imported or exported over a network or using a thumb drive.
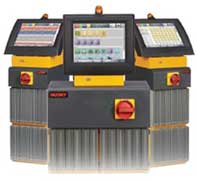
Altanium Delta3 also provides several process monitoring features, making it a powerful tool for analysing the system, optimising the moulding process, tracking errors, and finding the source of a recent error or predicting where future errors may occur. Altanium Delta3’s event log contains a complete record of all user interactions so that each step leading up to an issue can be followed. Additionally, the process history screen provides a visual summary of a mould’s recorded operation to map the behaviour of the system at the time of the error and search for potential causes. This data can be exported in a common file format and stored externally or used to create custom reports to further satisfy documentation requirements. For issues related to events occurring in real-time, the process trend screen plots data as it occurs and provides a graphical comparison of multiple zones in a single view to better understand the effects of the process and thermal relationship between zones. All of these variables are tracked through the process targets screen and compared against specification limits tied to thresholds that, if violated, trigger an alarm and digital output to alert operators to an issue while halting the molding operation or diverting the parts moulded during the last cycle.
Finally, there is a stand-alone program available that allows a user to access and monitor up to 50 controllers connected to a network. This server based application provides a dashboard view of all connected systems with the ability to drill down to the details of individual zones. Since it is a browserbased program, it is accessible from any webenabled device that supports Internet Explorer 9, Chrome, Firefox or Safari. This allows all controllers on the plant floor to be remotely monitored locally and in real-time within the same factory or by off-site personnel anywhere around the world.
For moulders who must produce the most precise, highly complex medical parts, Altanium Delta3 provides the ideal platform for achieving better part quality and process stability while mitigating the risk of bad parts entering the supply chain.
(PRA)