European tie-up for biobased products
Belgian Bio Base Europe Pilot Plant and Germany’s
Nova-Institute have formed a strategic partnership
that is ready to offer industrial customers development
work for biobased products. The companies offer
expertise in the choice of feedstock, life cycle analysis,
marketing strategy, development of a s calabl e
process, the production of the first sample material for
application testing and the custom manufacturing of
the first tonnes of product to enter the market. Bio Base
Europe Pilot Plant is a flexible pilot plant for developing
biobased products while Nova-Institute is a private
independent institute founded in 1994,specialising in
sustainable biobased chemicals.
In other news, Norwegian bioplastics maker BioBag International is tying up with Thailand's Thantawan Industry Public to manufacture its biobased products in Thailand. The companies announced the tie-up at the Inno Bioplast 2013 conference held in Thailand recently. The firms will focus on exporting the products to the US and will also jointly market the products in Thailand and Southeast Asia. Set up in 1959, BioBag introduced its biobased and compostable bags in 1993 and since 2003, has been totally focused on biodegradable bags that are made from Italy-based Novamont's Mater-Bi material.
Biocomposites in the arena
Dragonkraft Europe, an eco-conscious start up with
the backing of Akcros Chemicals, has launched a
new bio-resin system for the composites, coatings
and adhesives market. It promises manufacturers an
environmentally-friendly alternative to traditional oilbased
resins with many HSE benefits. The new epoxy
resin system boasts 100% renewable carbon content
whilst its hardener/booster package contains 20%
renewable matter. In addition, it has a 97% renewable
UV cure system that sets within 15-30 minutes in
natural daylight.
Dragonkraft also says it is BPA (Bisphenol A) free and has many health and safety benefits, including safer handling for workers and low odours.
The formulation can be used for many applications and the curing speed can be adjusted to suit user requirements. The system is a strong contender to traditional resins as it produces a high strength flexible-cured resin with a non-brittle finish. It has improved wet out and self-levelling properties, with low shrinkage and high temperature resistance. Its adhesion qualities onto many surfaces, including wood, plastics, metals and fibreglass, mark it down as an alternative to epoxy two-pack adhesives.
Biocomposite materials are heading for the slopes, after engineers at the University of Sheffield Advanced Manufacturing Research Centre (AMRC) composite centre produced a prototype snowboard from flax, cashew nut husks and recycled plastic. The team is investigating the potential use of these biocomposites for electric vehicles and other applications.
The aerospace and automotive sectors are increasingly using composite materials for their combination of low weight and high strength, which can provide significant improvements in fuel efficiency. These materials are usually made up of carbon or glass fibres embedded in an epoxy resin derived from petrochemicals. These materials are energy-intensive to manufacture, and are not easily recyclable or biodegradable when they reach the end of their lives.
Replacing some or all of these raw materials with sustainable alternatives can significantly improve the environmental performance of composites manufacturing.
The team produced two boards from flax fibres embedded in a resin containing 30% of cashew shell epoxy. The core is made from recycled PET foam, derived from old plastic bottles and other waste.
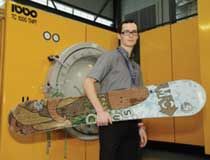
The AMRC team is continuing to develop biocomposites for a range of transport applications and researching how it can increase the concentration of fibres to give material properties that are at least a match for synthetic composites, as well as the design of the lay-up for a biocomposite component to optimise its performance. The team is also investigating other techniques to improve the energy efficiency of composites manufacturing, such as microwave curing, and whether these can be applied to biomaterials.
Algae to plastics
Chemists at the University of California, Davis,
have engineered blue-green algae to grow chemical
precursors for fuels and plastics — the first step in
replacing fossil fuels as raw materials for the chemical
industry.
Shota Atsumi, Assistant Professor of Chemistry at UC Davis and lead author of the study published in the Proceedings of the National Academy of Sciences, says the US Department of Energy has set a goal of obtaining a quarter of industrial chemicals from biological processes by 2025.
Biological reactions are good at forming carbon-carbon bonds, us ing carbon dioxide as a raw material for reactions powered by sunlight. It's called photosynthesis, and cyanobacteria, also known as "blue-green algae," have been doing it for more than 3 billion years.
Using cyanobacteria to grow chemicals has advantages as they do not compete with food needs, like corn’s role in the creation of ethanol.
The challenge is to get the cyanobacteria to make significant amounts of chemicals that can be readily converted to chemical feedstocks. With support from Japanese chemical manufacturer Asahi Kasei, Atsumi says he has been working on introducing new chemical pathways into the cyanobacteria.
The researchers identified enzymes from online databases that carried out the reactions they were looking for, and then introduced the DNA for these enzymes into the cells. Working a step at a time, they built up a three-step pathway that allows the cyanobacteria to convert carbon dioxide into 2,3 butanediol, a chemical that can be used to make paint, solvents, plastics and fuels.
Because enzymes may work differently in different organisms, it is nearly impossible to predict how well the pathway will work before testing it in an experiment, Atsumi said.
After three weeks growth, the cyanobacteria yielded 2.4 g of 2,3 butanediol/litre of growth medium — the highest productivity yet achieved for chemicals grown by cyanobacteria and with potential for commercial development, Atsumi said.
Atsumi hopes to tune the system to increase productivity further and experiment with other products, while corporate partners explore scaling up the technology.
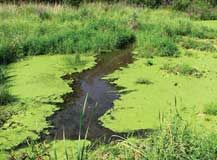
Co-authors of the paper are graduate student John Oliver, postdoctoral researcher Iara Machado and Hisanari Yoneda, a visiting researcher from Asahi Kasei.
Yet another project on algae-based polymers, known as SPLASH (Sustainable Polymers from Algae Sugars and Hydrocarbons), is being led by the Dutch Wageningen University and 20 partners from the EU. The four-year project will study the feasibility of developing a technology for using green algae, known as Botryococcus braunii, and green microalgae, Chlamydomonas reinhardti, to produce hydrocarbons and polysaccharides, which could be further converted into renewable polyolefins and polyesters. This specific algae produces long carbon chains, comparable to naphtha in the petrochemical industry, and sugars which are well suited for the purpose. Biomass cultivation is targeted to reach a pilot scale.
Elsewhere, US-based bioplastics maker Cereplast has commercialised algae bioplastics with the introduction of Biopropylene 109D. Cereplast identified a post-industrial algae source that does not rely on the commercialisation of biofuel production, allowing the company to introduce the material sooner than anticipated. In addition, Cereplast says it has discovered a post-industrial process that significantly reduces the odour that is typically inherent to algae biomatter.
Biopropylene 109D is an injection moulding grade manufactured with 20% post-industrial algae biomatter, which is a byproduct from algae biofuels and nutritionals, resulting from industrial processing to extract speciality chemicals . Biopropylene 109D can be processed on exist ing conventional electric and hydraulic reciprocating screw injection moulding machines, and is recommended for thinwall applications.
The company says it has several customers evaluating the technology and anticipates generating revenue from it during the first half of 2013.
(PRA)