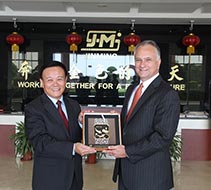
China’s manufacturer of blown film equipment, Guangdong Jinming Machinery is globally recognised for its collaborative efforts. Among other companies that Jinming has worked with (including Dow Chemical, Davis-Standard and BASF), ExxonMobil Chemical recently recognised the long-time partnership it has had with the Chinese firm. The US firm accorded Jinming a Global Strategic Development Partner award, which was presented by Larry Gros, Global Polymers Product & Applications Development Manager.
Since 2000, ExxonMobil’s polyolefin films products have utilised Jinming’s extrusion equipment to provide solutions for film converters. Further, senior managers from the two companies participated in several visits in 2013 and 2014, and likewise reiterating their cooperation on development projects and promotion of value- added solutions.
Remarking on the citation, Ma Zhenxin, President of Jinming said that the cooperation with ExxonMobil has helped enhance the company’s capabilities. ExxonMobil’s Gros commented that the relationship with Jinming has led the company to many opportunities to optimise polyolefin film solutions.
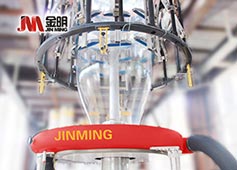
New air ring on Superex
Meanwhile, Jinming continues to develop its line of products. Recently it introduced the Superex series to meet customer demands for automatic control and high-end performance.
Jinming says its Superex blown film lines use advanced processing technology, dies and a new-generation high-efficiency multi-outlet cooling air ring independently developed and produced by Jinming to achieve high productivity. Jinming claims to be one of the few blown film equipment manufacturers using this technology in the world. Air ring cooling is crucial to the output, quality and physical properties of blown film products, it says.
The air ring design has been improved from the traditional one outlet and two outlets to multiple outlets. The air volume of each outlet is adjusted automatically. It can be lifted and lowered along the die axle centre. The air flows through several sections to increase the contact surface with the film bubble, and thus prolong the cooling time and improve the cooling efficiency. Besides, the pre-cooled film bubble will have higher melt strength. The air volume of the upper outlet can be increased without causing instability of the film bubble.
According to Jinming, the Superex cooling air ring increases the cooling efficiency by more than 40% compared with common air rings (or automatic air rings) with double outlets in the China market. As a result, the output of the production line will increase by 40-50% when the extrusion capacity is ensured. Testing data show that the production capacity of a 300-mm die is up to 420 kg/hour.
Superex also improves physical properties of film. After coming out of the die, the film bubble will first be pre-cooled at the lower air ring, and then blown up at the upper air ring so that the film bubble will have high strength and the products will have a high blown-up ratio. This cooling technique is similar to the POF and HDPE blow-up method.
Steady product precision control is also rendered with Superex. Automatic air ring technology is used in the design of the upper air ring for blow-up cooling control and an online film thickness measuring system is used for automatic film thickness control. Because the upper air outlet is away from the high-temperature die and the film bubble is pre-cooled, the precision control of the automatic air ring is less affected by external factors to achieve control stability and efficiency.
Likewise, Superex warrants improved product quality. Different from the process in which the film bubble is blown up after being out of the die, the film bubble will not be blown up until it is pre-cooled. High polymer materials if stretched in quasi-viscous flow state will have a lower degree of crystallisation, and thus the film transparency and mechanical properties will be improved.
Last but not the least, Jinming says Superex offers cost-efficient manufacturing with cost increasing only by 40%; and which can be recovered by savings from electricity expenses within six months.
(PRA)