Super plastics taking over conventional materials
Also, download this story from the electronic issue here
Super plastics, which include fluoropolymers, possess properties that may surpass those of conventional materials, which are required in key industries such as the building and construction sector, says Angelica Buan.
Reinforcements with plastics
Super plastic innovations have been going on for years, in response to major global challenges impacting major industries such as aerospace, automotive, oil and gas, to name a few.
For instance, in 2012, a higher-grade plastic was developed by a professor in Israel to provide materials option in construction and automotive applications. Moshe Kol, a professor at Tel Aviv's School of Chemistry, created the super plastic version of conventional polypropylene (PP), with the development of a new, higher quality catalyst for the polymer-production process. This, thus, resulted in a PP that has a uniform polymer chain and very high melting point. The super strong PP version can replace materials where steel, cement, or other heavy materials are required, but at a lower weight.
Super plastics are also known to be heat resistant. At the University of Michigan’s College of Engineering, a new super plastic is being developed, which exhibits thermal properties, enabling to direct heat away from its source that make it suitable for the aerospace, building and electronic devices applications.
The team, led by Associate Professors Jinsang Kim and Kevin Pipe, are using hydrogen bonding from two different liquid polymers to regenerate a continuous pathway for heat transfer. These same principles can be used to “fine tune” other thermal properties to design future heat resisting or insulating plastics, they said.
Last year, IBM scientists developed a new class of ultralight, strong and self-healing materials. The team said the fully recyclable new polymers resist fractures, and revert to their original shape.
Fluoropolymer coatings show promise
Currently, amongst the most promising super plastic is fluoropolymer. This new class of plastics opens up new potential opportunities for major industry applications that require durability; chemicals, weathering and thermal resistance; favourable mechanical properties; and at the same time light weight.
The consumption for fluoropolymers is expected to grow at a CAGR of 5.2%, in terms of volume through 2019, according to a report by Markets and Markets, which says the sector will be worth over US$8 billion by 2019.
Meanwhile, the global fluoropolymer coating additives market is expected to grow substantially over the forecast period of 2014-2019 on account of increasing application scope. Growing construction and automotive industries in Asia Pacific and Latin America particularly, in China, India and Brazil, are projected to augment the market in the near future.
The promising characteristics of fluoropolymer coating additives projects the product as a favoured solution for applications requiring high resistance to solvents, acids and bases, according to a report released by US research firm Grand View Research.
On the basis of products, fluoropolymer coating additives have been classified into fluorinated ethylene propylene, polyvinylidene fluoride (PVDF) and polytetrafluoroethylene (PTFE). Extensive application segments are anticipated to deliver enormous opportunities to various end-use industries on account of intrinsic properties such as high corrosion resistance and chemical inertness.
Highly priced fluoropolymer coating additives and volatile raw material prices are the major setbacks to the market expansion.
Construction was the largest end-use segment in 2014 and is expected to maintain its dominance in global market over the next seven years. Improving infrastructure coupled with rising speciality polymer coatings requirement in mature economies is expected to augment fluoropolymer coating additives demand in the segment over the foreseeable future.
In terms of demand, Asia Pacific holds the largest market share of fluoropolymer coating additives and is expected to remain the market leader over the next seven years. Increasing demand in construction industry in emerging economies such as India and China is expected to drive the market penetration in the region over the forecast period.
The coating additives market is moderately consolidated with key market players accounting for over 50% of the market share. Major players include Dow Chemical, Eastern Chemical Company, AkzoNobel and BASF.
Feedstocks used
Fluoropolymers can be manufactured using various raw materials and different manufacturing processes. The value chain spans from basic fluorochemicals and mineral products to end-users. Fluorspar, hydrogen fluoride, hydrogen sulphide, ethylene, and fluorocarbons are the key feedstocks.
Based on a review published in 2012 by researcher, Hongxiang Teng of the Polymer Research Institute, Department of Chemical and Biological Sciences, Polytechnic Institute of New York University, there are two fluoropolymer materials, perfluoropolymers, whereby all the hydrogen atoms in the analogous hydrocarbon polymer structures were replaced by fluorine atoms; and the partially fluorinated polymers, whereby there are both hydrogen and fluorine atoms in the polymer structures.
Conquering the building sector
Of the super plastics, the PTFE is one of the smoothest and toughest materials available, according to European trade association PlasticsEurope.
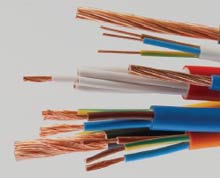
US materials firm DuPont discovered and pioneered industrial-grade Teflon PTFE, the compound found to be heat resistant and chemically inert, and that provides a nonstick surface.
It has now moved on to its latest offering, ECCtreme ECA (Epitaxial Co-crystallised Alloy), a new family of meltprocessable high-temperature perfluoroplastics (HTP) that can withstand continuous-use temperatures of up to 300°C, exceeding the previous performance limits of 260˚C.
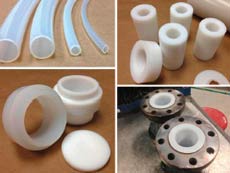
The firm says that this super plastic offers the benefits of good chemical and permeation resistance, dielectric properties and a low coefficient of friction. The company has also confirmed that US standard organisation, UL, after comprehensive mechanical, electrical and fire tests at thicknesses of 0.75 mm and above, has classified ECCtreme ECA in class V-0, and confirmed electrical and mechanical Relative Temperature Index (RTI) values of 300°C, said to be the highest RTI value of all plastics registered in the UL database.
Among the main applications for ECCtreme ECA are moulded parts, pipes and hoses, as well as sheathings for cables, wires and sensors for very harsh ambient conditions. Three types are available with different melt flow rates (before and after heat treatment) for a broad range of applications.
Meanwhile, Belgium-based Solvay has also embarked on producing fluoroplastics via its plant in Changshu, China. The facility, the company’s third fluoroplastics unit worldwide, has recently started production of its FKM type Tecnoflon products, and sources raw materials from production partner Shanghai 3F New Material. Solvay says its Tecnoflon is resistant to chemicals and heat exceeding 250°C.
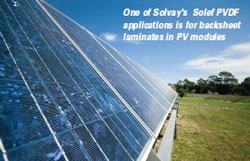
Meanwhile, Solvay is building a polyvinylidene fluoride (PVDF) plant on the same site, which is expected to come on-stream by early 2017. The plant will be producing its Solef PVDF for various applications that include backsheet laminates used in photovoltaic modules, gas sampling bags, pump and filter diaphragms, anti-graffiti covering films, and copper plenum cables and for plenum rated optical fibre jacketing.
Rigging up solutions for exploration platforms
The common nemesis for oil and gas exploration platforms is corrosion of equipment parts. Protection traditionally is delivered by applying coatings onto metallic parts. For this purpose, fluoropolymers can offer the same, if not more effective advantage to these parts.
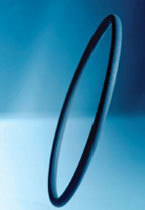
Minnesota-headquartered 3M, with its subsidiary, Dyneon, headquartered in Germany, says its 3M Dyneon fluoropolymers exhibit “impressive” resistance towards fuels, engine oils and elevated temperatures. According to 3M, its wide range of fluoropolymers can operate in temperature ranges from -200°C to +260°C; provide chemical resistance; have the lowest permeation rates; and are able to handle extensive pressure fluctuations where optimum performance is required. The typical applications are in chemical hoses, pipe linings, O-ring, high-pressure pipes, and other components used in deep-sea, offshore or land-based oil exploration.
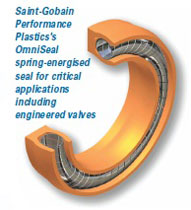
US-based Saint-Gobain Performance Plastics offers its OmniSeal spring-energised seal product line that can be used for a wide range of critical applications from cryogenic to high temperature and high pressure for engineered valves in the upstream and downstream sectors. During the design process, finite element analysis (FEA), including advanced material models for PTFT and polymers, is utilised.
The product addresses industrial challenges, particularly in ultradeepwater production, high pressure and high temperature, harsh chemicals, rapid gas decompression resistance, long durability at extreme temperature and sour gas concentrations via proprietary fluoropolymer compound qualifications.
(PRA)Copyright (c) 2015 www.plasticsandrubberasia.com. All rights reserved.