Roll out of new technologies -- Battenfeld-Cincinnati
Also, download this story from the electronic issue here
At the recently concluded Chinaplas 2015 show, extrusion machinery manufacturer Battenfeld-Cincinnati Extrusion Systems, which has been active in China for 19 years, exhibited new machinery, outlined its strategic plans and also introduced the new management of the company.

Open house to showcase machinery
Running concurrently with Battenfeld-Cincinnati’s participation at the exhibition, was an open house where it welcomed 210 visitors at its Shunde plant for presentations and extrusion line demonstrations.
Battenfeld Cincinnati also introduced its new management line-up, which took effect from this year.
Early this year, Toni Bernards was appointed CEO and Bruce Lamont as COO of Battenfeld-Cincinnati China. In addition, Bernards also serves as Head of Global Sourcing for the group. Germany-born Bernards was formerly General Manager of machine maker Milacron’s Chinese subsidiary.
Bernards commented, “We see that the Chinese market needs both – top performance solutions for highend applications and turnkey lines for standard products that are simple, easy to handle and quickly available. We were able to show our customers both on the booth and at the demonstration in our plant that we can do both and so can deliver tailor-made solutions for every company.”
The company had two demonstrations, where it presented two lines in production: a high-output (1,200 kg/hour) line for 400 mm gas pipe extrusion and a LeanEX high-speed line for 20 mm PE-RT pipe that ran with a line speed of 40 m/minute.
The 400 mm line for gas pipe extrusion features the solEX 75 single-screw extruder, which includes as standard, an AC motor that saves 20% energy compared with a DC motor and is able to achieve the higher outputs with a low noise level of below 80 db.
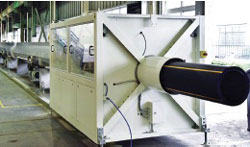
The proven helix 400 VSI-T pipe head with inner pipe cooling EAC (efficient air cooling) also ensures melt homogeneity and pipe quality, with minimised sagging. This is why the combination of solEX and helix VSI-T is also ideal for large diameter solid wall PO pipe extrusion – diameters up to 2.6 m are currently possible.
The inner cooling in the pipe head also enabled a 45% reduction in line length from 85 m to 47 m. The PE material BorSafe 3490LS was sponsored by Borouge and the dehumidifying and conveying system came from Piovan. This energy reclaim system was used for preheating of the material, saving 30% energy, bringing the line’s combined energy consumption per tonne of PE processed down to 268 kWh.
The 400 mm PE-RT line was sold to Hebei BlucicinPlastic Industry, located at Guan, Hebei Province, before the open house. The Chinese company produces PVC, PPR, PE and PB/PBOB pipes. It also bought the first 32 mm PBOB pipe line from Battenfeld-Cincinnati China in 2013.
The second line on display, LeanEX line, is available in five sizes. The LeanEX concept stands for “lean extrusion”, ie simple, turnkey lines for standard PO pipe applications built with European technology and locally sourced screws, barrels, motor and drive.
The LeanEX series was first launched in 2009 with a 63-mm model and Following customer demand in South East Asia, South America, Africa, the Middle East and Russia. It has now expanded to 160 mm and 250 mm, with the 400 mm model shown at the exhibition. The company has also introduced a 600 mm line since then.
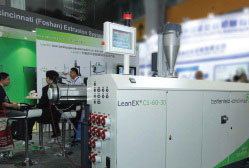
Bernards pointed out, “The line is designed for customers seeking a low cost line for small, standard pipe applications.” The lines come in a basic package with limited options, and a smaller control panel and power control system. The pipe heads are from the standard battenfeld-cincinnati helix series.
“The components for the lines come from Europe and China and the price is 10-15% lower than other lines,” he explained.
The line shown at the open house was a LeanEX 63 mm, with a LeanEX C1-60-30 single screw extrusion extruder producing a PE-RT pipe with dimensions of 2.3 mm at a high line speed of 40 m/minute and an output of 320 kg/hour. The HDPE XSene XRT 70/PE-RT Type II material for this line was sponsored by Total Refining & Chemicals.
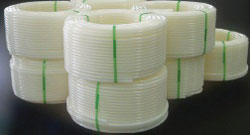
New strategies to keep growth momentum
The new CEO of the company’s Chinese operations said during a group interview that the company is aiming to grow 10-15% in China this year. Bernards also said that the company will be extending its customer base to small/ medium companies.
“The trend for small/medium customers is energy savings,” he said. “We will double the sales force over the next few months all over China and also pump up engineering capacity.”
According to Mark Feng, Group Vice President of Sales for Asia Pacific (previously General Manger and Sales Director for China), the company expects good growth in Shangdong, Szechuan, Guangdong and Hebei “where we see good business since there a lot of pipe and profile producers located there.”
It is for this reason that the company will double its sales force in China to push its lines in the domestic market.
Feng also added that the company is seeing strong growth for its export markets in Asia in countries like Vietnam, Thailand and Malaysia as well as Japan.
First PO solid-wall pipe line for 2.6 m pipes
Meanwhile, Battenfeld-Cincinnati (Austria/Germany) has sold its first large solid-wall PO pile line, with a diameter of up to 2.6 m, to South Korean pipe manufacturer Hyundai Pipe Co from Sang Ju City.
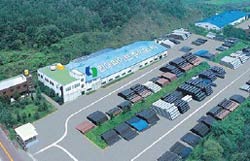
Hyundai Pipe is among the five largest manufacturers of pipes in South Korea and currently produces them in dimensions ranging from 100 to 1,500 mm for transporting fresh and waste water and for applications in the petrochemical industry. The company, which is certified according to DIN ISO 9001 and 14001, supplies both large companies, such as ExxonMobil and Shell, as well as small companies. It already has three lines from Battenfeld- Cincinnati in its production plant, which is equipped with eight extrusion lines in total, and has a production capacity of 22,000 tonnes/year.
To be able to manufacture pipes with huge diameters, the extrusion line needs an extruder with a suitably high plasticising capacity.
In the line ordered by Hyundai, this is made possible by means of a solEX 120-40 extruder, which achieves an output level of 2,200 kg/hour with its processing length of 40 D.
Alongside the extruder, the tooling is the second key component of this line. This has the task of ensuring minimum ovality and minimum sagging, particularly for thick walls of more than 100 mm. The helix VSI-T+ system ensures low pressure build-up and operation independent of viscosity with its tried-and-tested combination of a spiral mandrel for initial melt distribution and a compact lattice basket for fine dispersion.
Meanwhile, the EAC (efficient air cooling) internal pipe cooling system assures high line speeds and pipe quality. It also results in a shortened cooling section and thus a shorter total line length, which was also very important for Hyundai Pipe.
(PRA)Copyright (c) 2015 www.plasticsandrubberasia.com. All rights reserved.